Understanding warehouse shuttle systems and their applications
Bob Hoffman
2 de diciembre de 2021
Reading Time:
5 minutos
Common questions about warehouse shuttle systems.
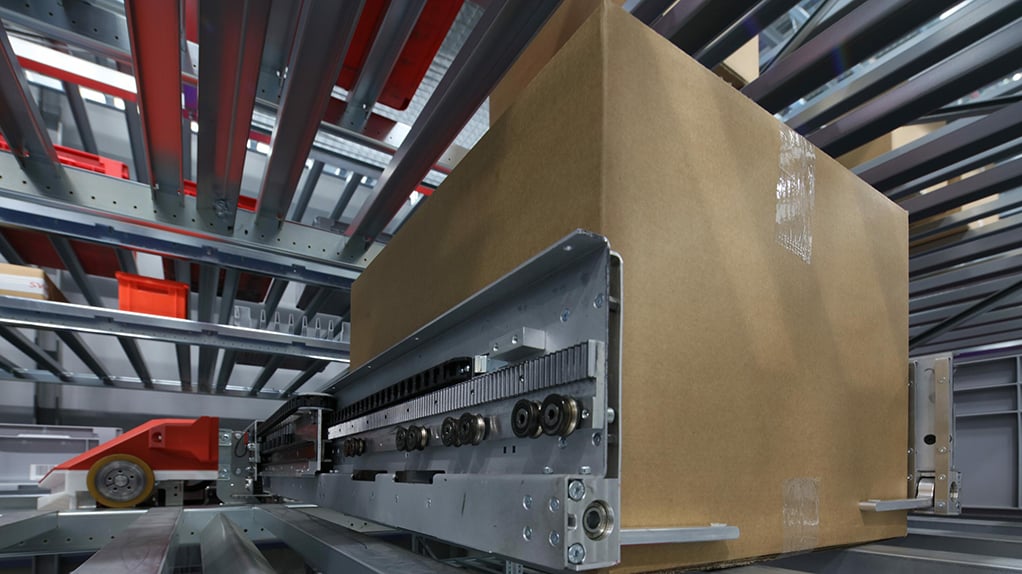
Warehouse automation continues to evolve and with more choices now on the market, warehouse operators face an increasingly complex decision when selecting the automation that is right for their warehouse and application. To help simplify things, we asked Bob Hoffman, Senior Director, Consulting at Swisslog Americas E-Commerce/Retail, to answer some common questions about warehouse shuttle systems.
Q. What are warehouse shuttle systems?
BH: Shuttles are a type of automated storage and retrieval system (AS/RS) that use mobile robots or “shuttles” to travel horizontally down rows of products. These shuttles are equipped with arms that allow them to retrieve product based on instructions from the automation control system and deliver the selected products to vertical lifts that transport the products to a conveyor or other system.
Shuttle systems typically consist of multiple aisles with each storage level served by its own shuttle and each aisle by dedicated lifts. That means each shuttle has access to all products in the storage level and because you have multiple shuttles and lifts working together, shuttle systems enable high performance retrieval of large inventories of stored products in totes, bins, cases, or cartons. The technology has also been adapted for pallet handling. Pallet shuttles use the same approach as carton and tote shuttles but are designed with the power and lift capacity to store and retrieve full pallets.
Q. How are warehouse shuttle systems used?
BH: Warehouse shuttle systems are particularly well suited to support the following applications:
- E-commerce fulfillment: When equipped with goods-to-person pick stations, shuttle systems serve as a powerful engine to enable fast fulfillment in high-volume, dynamic e-commerce environments. In this application, the shuttle systems store products in totes that are delivered to stationary pickers as they are needed, creating dramatic improvements in pick speeds by eliminating the need for pickers to walk the warehouse floor.
- Store replenishment: In omni-channel or dedicated retail replenishment warehouses, shuttles are ideal for supporting mixed case palletizing. The shuttle software provides the ability to release cases or cartons based on different criteria, supporting faster manual palletizing. Shuttles can also work with robotic palletizing systems to fully automate the palletizing process.
- Buffering and consolidations: Shuttles are ideal for receiving applications where buffering is required and for order consolidation in e-grocery fulfillment.
- Cold storage: Some vendors, such as Swisslog, have designed their shuttle systems to operate in cold storage environments, enabling storage and retrieval of cases, cartons, or pallets in cold storage warehouse to improve productivity and minimize the time warehouse workers are exposure to harsh environments.
Q. What are the benefits of warehouse shuttle systems?
BH: The biggest benefit of shuttle systems is the high-performance they deliver to item picking, carton handling and pallet handling applications. Shuttles offer the highest peak throughput of any AS/RS, making them ideal for dynamic, high-volume applications. They also offer excellent storage density, particularly in high-bay warehouses where the system can be configured to utilize the full building height.
Shuttles provide excellent application flexibility through a modular design that enables the number of aisles and levels, with variable storage depth, to be tailored to the available space. Shuttles are also extremely versatile as they can handle cases, cartons, bins and totes – within the same system
Q. What are the alternatives to shuttles?
BH: Warehouse shuttle systems are just one type of AS/RS. Similar functionality is provided by cranes and cube-based storage systems. The specific requirements of the application will dictate which system is the best fit.
In smaller environments, where the height of the automation is limited, such as in-store micro fulfillment centers (MFCs), a cube-based system such as AutoStore can provide better density than a shuttle system. In these applications, AutoStore provides sustained throughputs similar to shuttles if the system is configured to minimize “digging.” AutoStore’s density advantage diminishes as building size increases and the system can only store products in specific bins, so it isn’t applicable for direct carton or case handling. Mini-load cranes, such as the Swisslog Tornado, can provide a cost-effective automation solution where throughput and density are not a priority.
Shuttles should be strongly considered in applications with the following characteristics:
- The height of the warehouse enables more vertical storage
- Products in storage need to be immediately available without digging as in order consolidation
- Peak throughput is a high priority for the automation system
- The system is required to handle cases or cartons or needs to handle products outside of bins or totes
Q. What other warehouse technologies do shuttle system work with?
BH: Shuttle systems’ modular design makes them ideal for configuring with other warehouse automation systems. The two most common examples are using shuttles for order consolidation in e-grocery fulfillment and for creating mixed-case pallets for store replenishment.
- Shuttles and AutoStore: At Swisslog, we’ve analyzed the requirements of e-grocery MFCs and determined AutoStore is the preferred goods-to-person automation for this application. But that doesn’t mean shuttles don’t have a role in e-grocery fulfillment. In larger MFCs as well as regional or central fulfillment centers, shuttles can work with the AutoStore system to streamline order consolidation. Completed orders from the ambient and chilled AutoStore systems can be loaded into a shuttle system, along with the frozen portion of the order. When the order is schedule for pickup or delivery, the three components of the order can be dispatched by the shuttle and quickly consolidated.
- Shuttles and ACPaQ: Warehouse operators can implement shuttle systems to improve manual palletizing and then later add a robotic palletizing system, such as Swisslog ACPaQ, to fully automate the process.
One of the benefits of working with Swisslog is that our global automation control software, SynQ, integrates control of multiple automation systems into a single platform.
Q: What are the key features to look for in a shuttle system
BH: It can be easy to get bogged down in somewhat irrelevant “features” such as the speed the shuttle travels down the row. In reality, this has little impact on system throughput. What’s more important is how the system is configured and its ability to effectively handle product with minimal intervention. In applications where high throughput is required, the ability to configure the system with multiple lifts down an aisle can eliminate bottlenecks at the lifts and enable system throughput to be maximized. Error correction through auto repositioning allows the shuttle to recognize when products are misaligned within the system and use its arms to reposition and retrieve those products without manual intervention. Condition monitoring can also be a valuable feature for shuttle systems. Between the lifts and the shuttles, shuttle systems have a lot of moving parts and the ability to continuously monitor these components can maximize system availability.
Q. Where can I learn more about shuttle systems?
BH: To learn more shuttles systems, visit our shuttles web page or contact Swisslog.