Three ways to maximize flexibility in deep-freeze automation systems
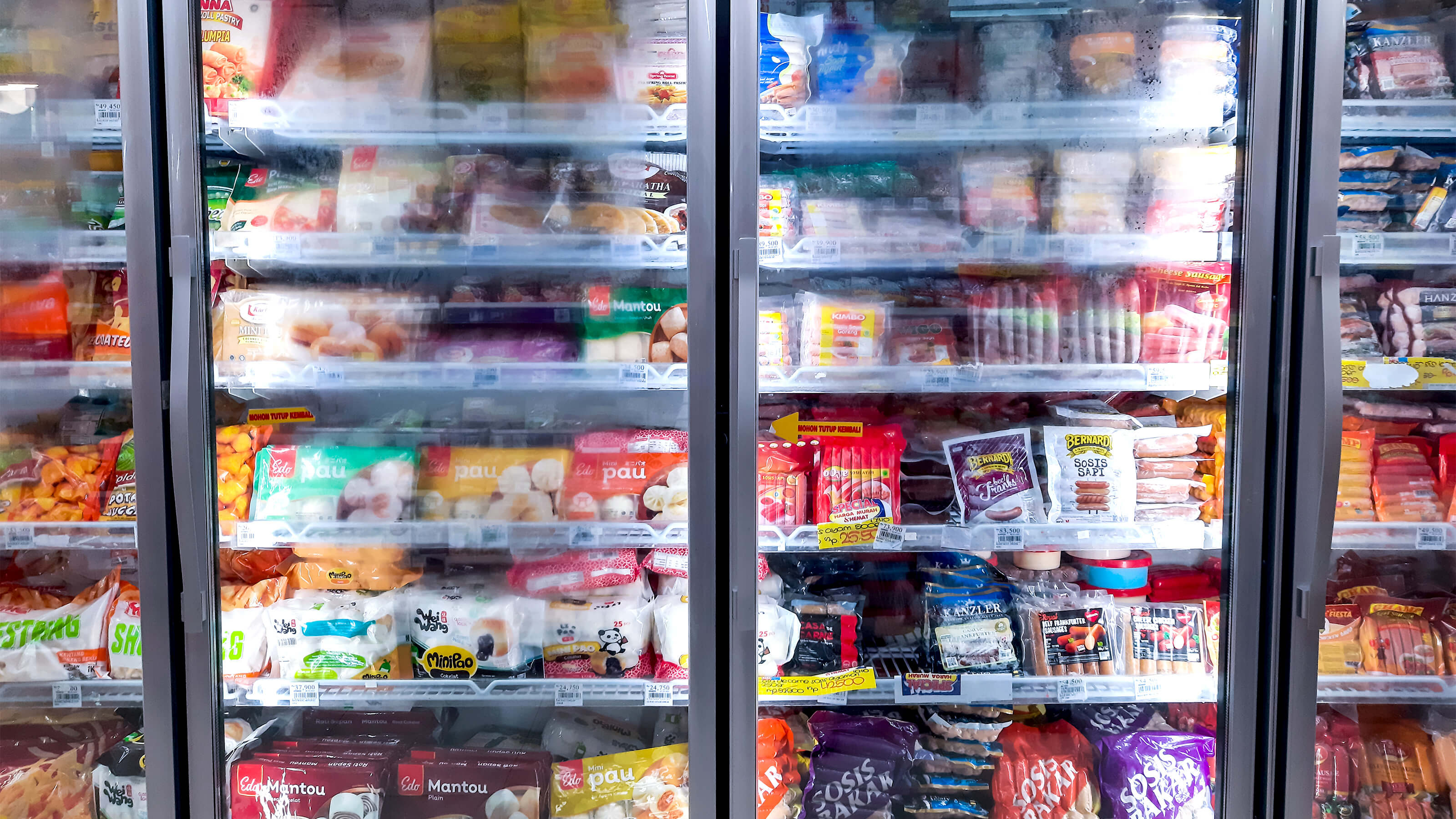
1. Designing flexibility into the deep-freeze ASRS
Flexibility takes multiple forms in automation solution design, but it starts with the capabilities of the ASRS itself. Automation solution designers will typically seek to optimize a system’s throughput and storage capacity based on specific business and product requirements. For example, if a company is seeking to maximize capacity and density, a multi-deep solution might be recommended whereas a company prioritizing throughput and SKU flexibility might be better served by a double-deep solution.
In our experience designing solutions for shared-use warehouses, using automated double-deep storage often strikes the right balance between the needed throughput and storage density – particularly when the SKU range can flex.
3PLs also need to make sure their system is flexible enough to handle the full range of pallet weights and dimensions that might be encountered over the life of the site. A crane with a load capacity of 1,000 kg may meet the requirements of current customers, but will it limit future opportunities? To ensure the automation system doesn’t restrict customer acquisition, consider deploying cranes with a capacity of 1,300 kg and load handlers that can handle the full range of pallet dimensions.
Additionally, pallet storage location height should be considered carefully, that is, allowing for a more generous height locations in the design phase can greatly impact on future operational flexibility. Whereas designing specific locations height for current state might seem more space efficient in the short-term but will lead to future inflexibility. System capacity and energy efficiency can be achieved by increasing facility height, often utilizing a rack-clad solution of height greater than 40m if permitted.
Another consideration that shouldn’t be ignored is pallet quality. 3PLs have little control over the quality of the pallets they receive, and weak or broken pallets can create downtime in automation systems. You want to avoid having your engineers go into the freezer and work at height to resolve pallet quality issues. The use of Pallet exchangers on inbound allow for the replacement of incompatible pallets, whilst pallet support boards have emerged as a practical solution for supporting or replacing weak or broken pallet components that would otherwise create downtime. Be sure to work with your automation provider to develop a plan for dealing with poor quality pallets.
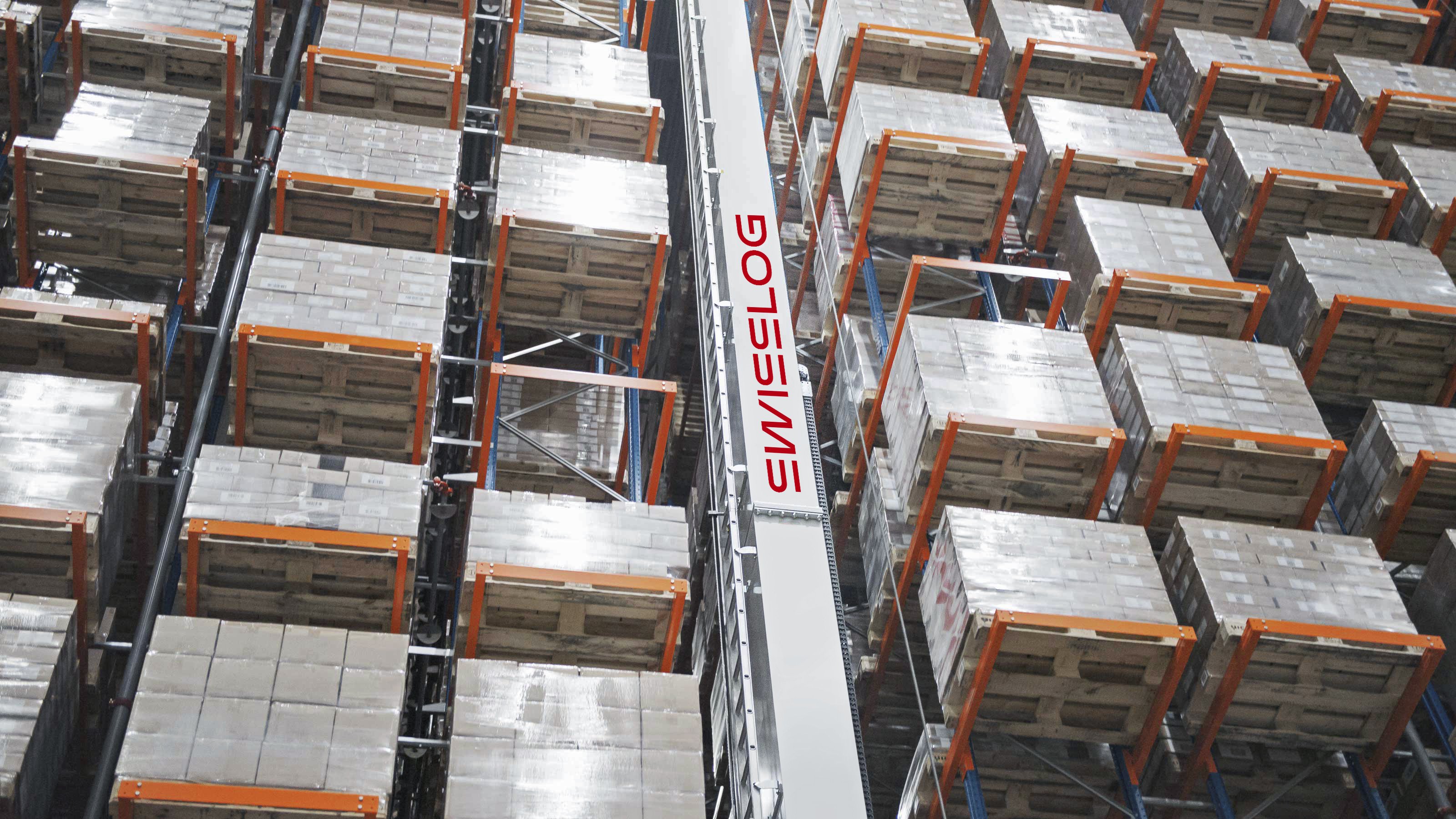
2. Choosing software that enables operating flexibility in shared-use deep-freeze warehouses
The software that controls the automation system plays an important role in enabling operating flexibility. One key is the ability to manage inventory for different customers to different business rules. Swisslog’s SynQ software not only enables real-time inventory tracking and management to ensure accurate stock levels and locations, but it can also assign ownership and management rules to each pallet to enable 3PLs to effortlessly manage different customer requirements within the same solution.
SynQ also supports enhanced operating flexibility by including WMS, WES and ACS functionality in a single platform. This allows single-system management of manual and automated processes across the warehouse, which can be especially valuable for 3PLs preparing mixed-SKU pallets. With SynQ, you can effectively orchestrate ASRS operations with manual, semi-automated or fully automated palletizing.
Finally, SynQ’s modular architecture enables flexibility by allowing operators to deploy only the modules they need today and add other modules later as needs change.
3. Managing pallet movements in the deep-freeze warehouse
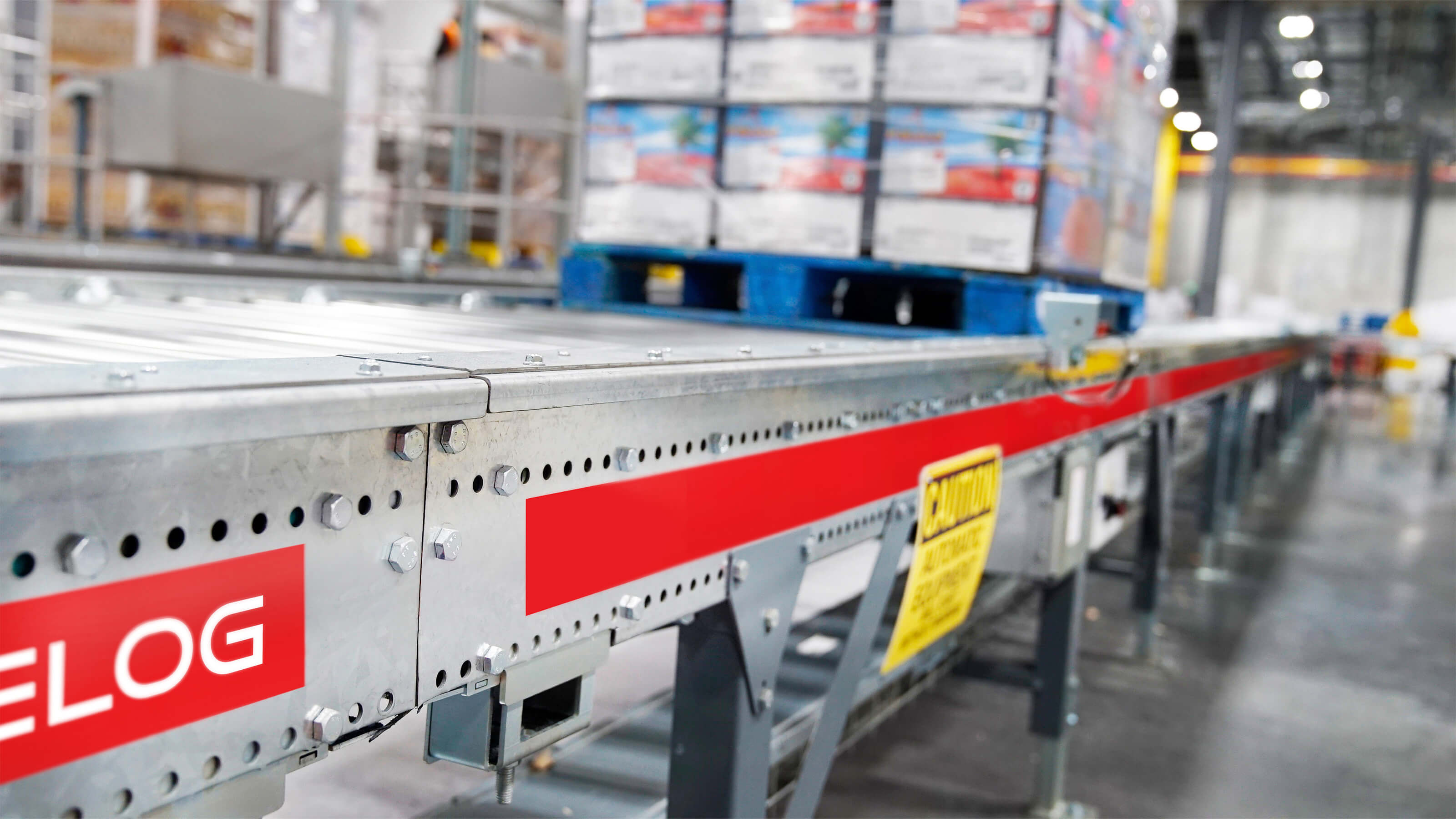
The final piece of the puzzle is automating pallet movement within the freezer. AGVs and AMRs provide the ultimate flexibility in pallet movement, but these systems aren’t currently recommended for deep-freeze environments due to the effect of cold temperatures on battery performance and life. Automated conveyors and monorail systems are better suited for deep-freeze environments and, when properly designed, can still enable flexibility.
Automated pallet conveyors, such as the Swisslog ProMove, offer flexibility in terms of layout and can be reconfigured to accommodate for future changes in warehouse operations. Swisslog monorail systems can support higher throughputs than conveyors and offer the flexibility to be configured as a hanging rail to free up floor space or fixed to the floor. They can also enable simpler routing, allow long- or short-side leading pallet orientation, and are less -susceptible to poor quality pallets. With a single track handling both inbound and outbound pallets, a monorail provides the flexibility to easily pull pallets back into the automation if trucks are delayed or there is a last-minute change to an order.
Both systems can be effective in the right environment, with the choice between the two often dependent on the overall system throughput requirements.
Conclusion
The deep-freeze environment puts some limits on automation system flexibility, but proper solution design combined with the right software can ensure 3PLs have the system flexibility to meet a broad range of customer requirements and the operating flexibility to streamline customer onboarding and inventory management. Swisslog has decades of experience providing automation solutions for frozen food warehouses and a proven portfolio of technologies that deliver the flexibility 3PLs need.