Warehouse shuttle systems maximize density and throughput
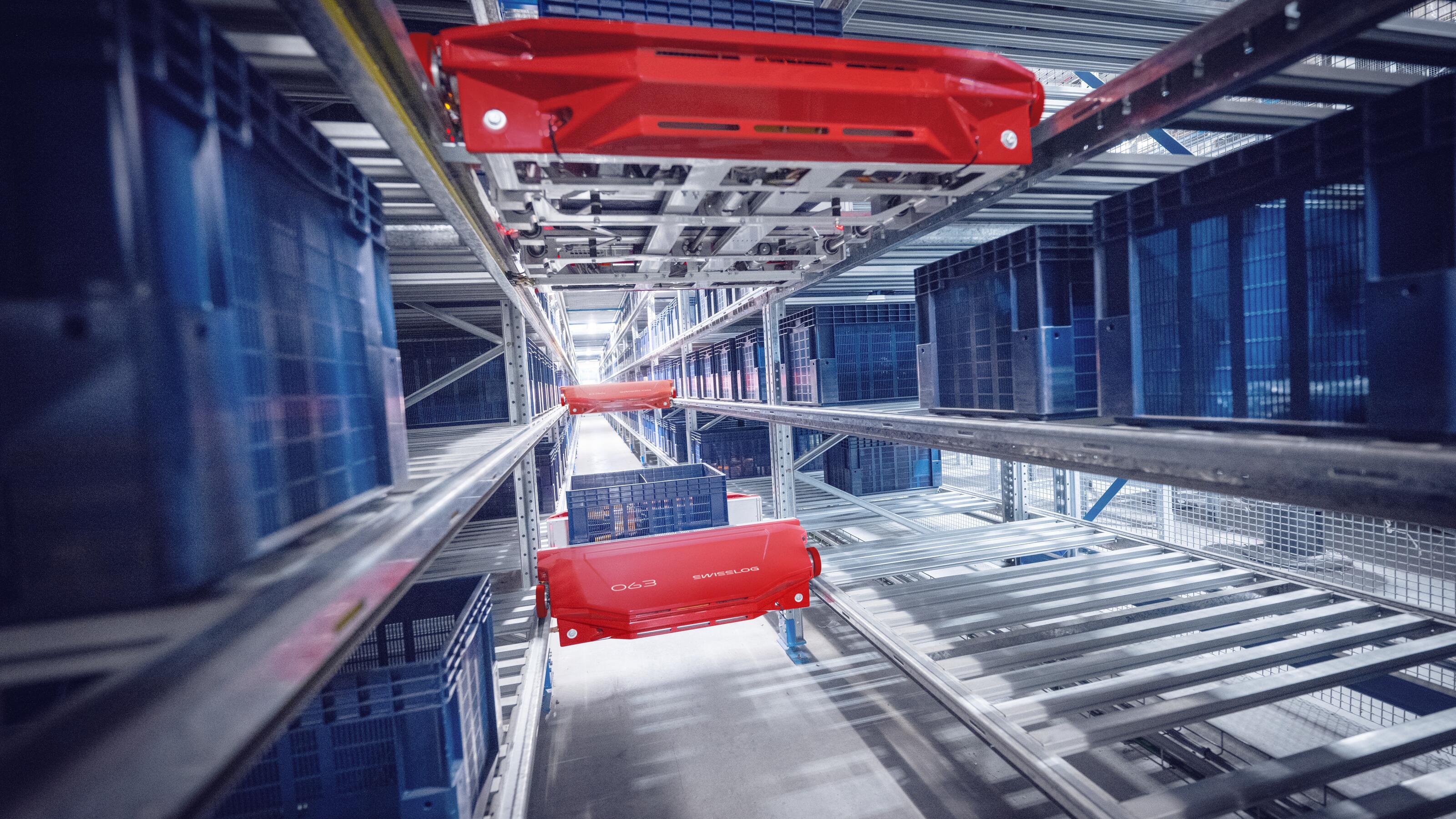
Why use a warehouse shuttle system?
Shuttle systems often provide the right balance of flexibility, throughput and storage density for general merchandise retailers seeking to automate store replenishment and direct-to-consumer fulfillment processes.
One of the benefits of shuttle systems is that they can use the full height of the warehouse for storage, enabling excellent density in higher-ceiling buildings. In fact, shuttles provide higher density than any other goods-to-person ASRS in buildings with ceiling heights above 12 meters. Swisslog’s CycloneCarrier light-goods shuttle, for example, can be built up to 25 meters high.
Shuttles also excel at supporting the high throughputs retailers need during peak seasons. They provide the highest throughput of any goods-to-person technology, potentially enabling retailers to meet demand peaks with fewer shifts and temporary workers. They can also deliver high availability through built-in redundancy and intelligent stock allocation that allows orders to continue to be filled if a workstation or aisle goes offline.
In addition, some shuttle designs offer the flexibility to handle both totes and cases. Swisslog’s adjustable arm shuttles can adapt to different load sizes, allowing cases and totes to be stored in the same system, so orders can be picked directly from the case or cases can be sequenced for store replenishment. We also offer a fixed-arm shuttle design that uses a standardized tote size to simplify configuration and reduce initial costs.
Both versions incorporate our “housekeeping” feature, which enables the load carrier to recognize and adjust totes that are out of alignment. With other shuttles, totes that have shifted their position due to system vibration or small seismic events will trigger an error when the system is trying to retrieve them. Resolving that error requires a stoppage until a technician can climb into the system and manually adjust the tote.
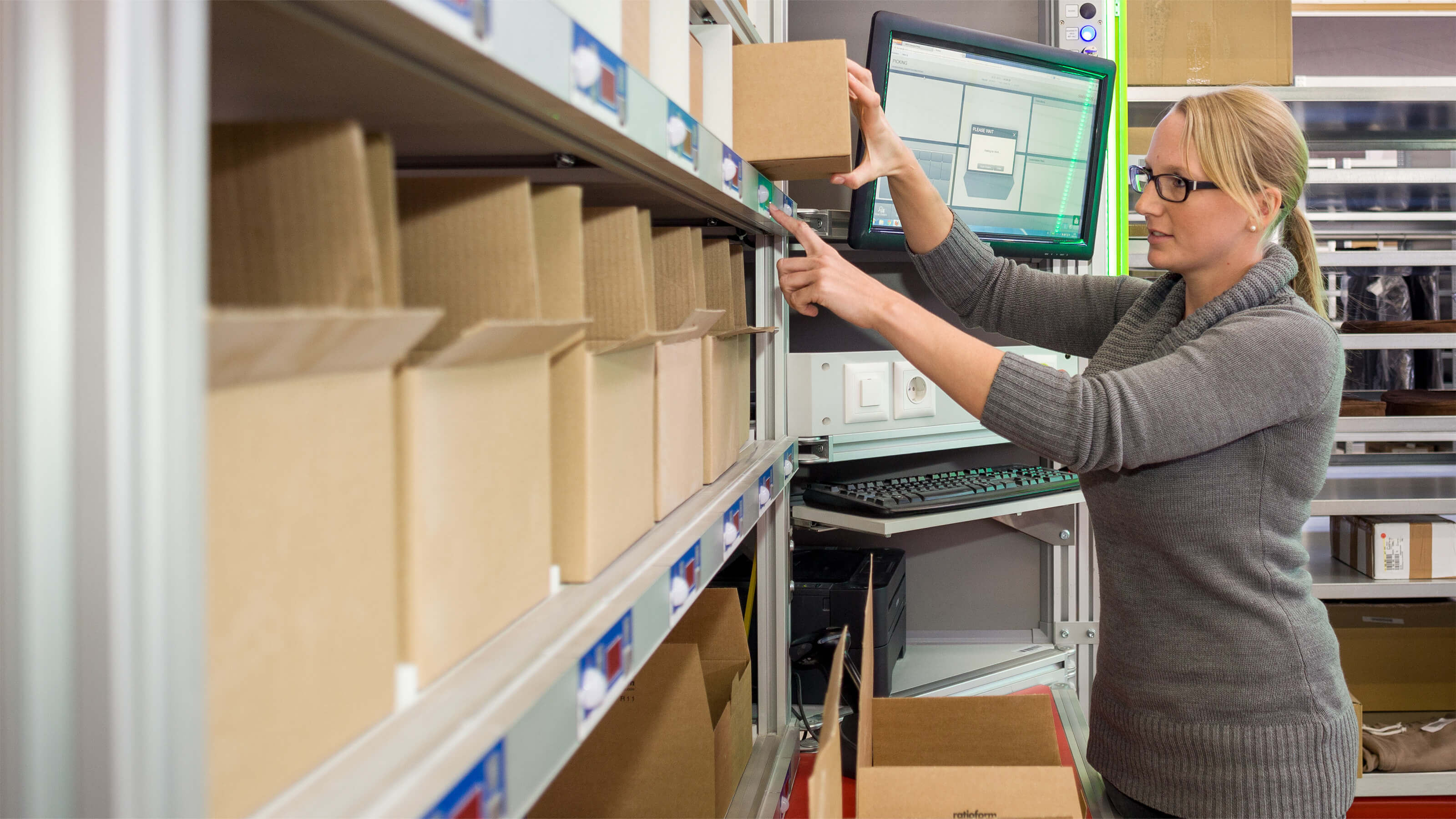
Configuring warehouse shuttles for omnichannel fulfillment
The benefits of shuttle systems are enhanced by expert configuration that optimizes shuttle performance and material flows in omnichannel warehouses.
For example, one best practice is to design a hybrid receiving/induction station with an interface to the WMS and WCS. This allows product to be received and inducted in one step, improving flows and minimizing touches.
Key decisions also need to be made around what products will be stored in the shuttle and how those products will be distributed within the shuttle. Swisslog design consultants are experts at allocating inventory to balance density, pick speeds, and inventory availability. They work with your inventory and order data to determine which products can be picked most efficiently through the shuttle and to eliminate the potential for “golden totes” that can delay order fulfillment if a shuttle component is offline.
Another critical consideration is workstation design. In many omnichannel environments, you’ll want workstations that can support e-commerce or store replenishment depending on order profiles. For example, during the first nine months of the year, half the workstations may be supporting store replenishment and half e-commerce. Then, during the holiday shopping season when stores are well-stocked, some or all of the workstations are used for e-commerce fulfillment. This flexibility enables the system to be sized closer to normal volumes while still being able to adapt to peaks, rather than sizing the system for peak demand.
Workstations should also be designed to optimize comfort, productivity and efficiency. The Swisslog 2-4 shuttle workstation—two source bins and four orders being picked to—is designed to minimize dwell time in bin presentation and maximize productivity and throughput. The shuttle control software also plays an important role in balancing workflows across stations to prevent “station starvation.”
Software ultimately plays the most critical role in the success of a shuttle system deployment. With a robust software control system, such as our SynQ platform, the system can organize SKUs based on velocity and optimize material flow and system efficiency through coordinated order management, inventory management, workflow processing, and wave management.
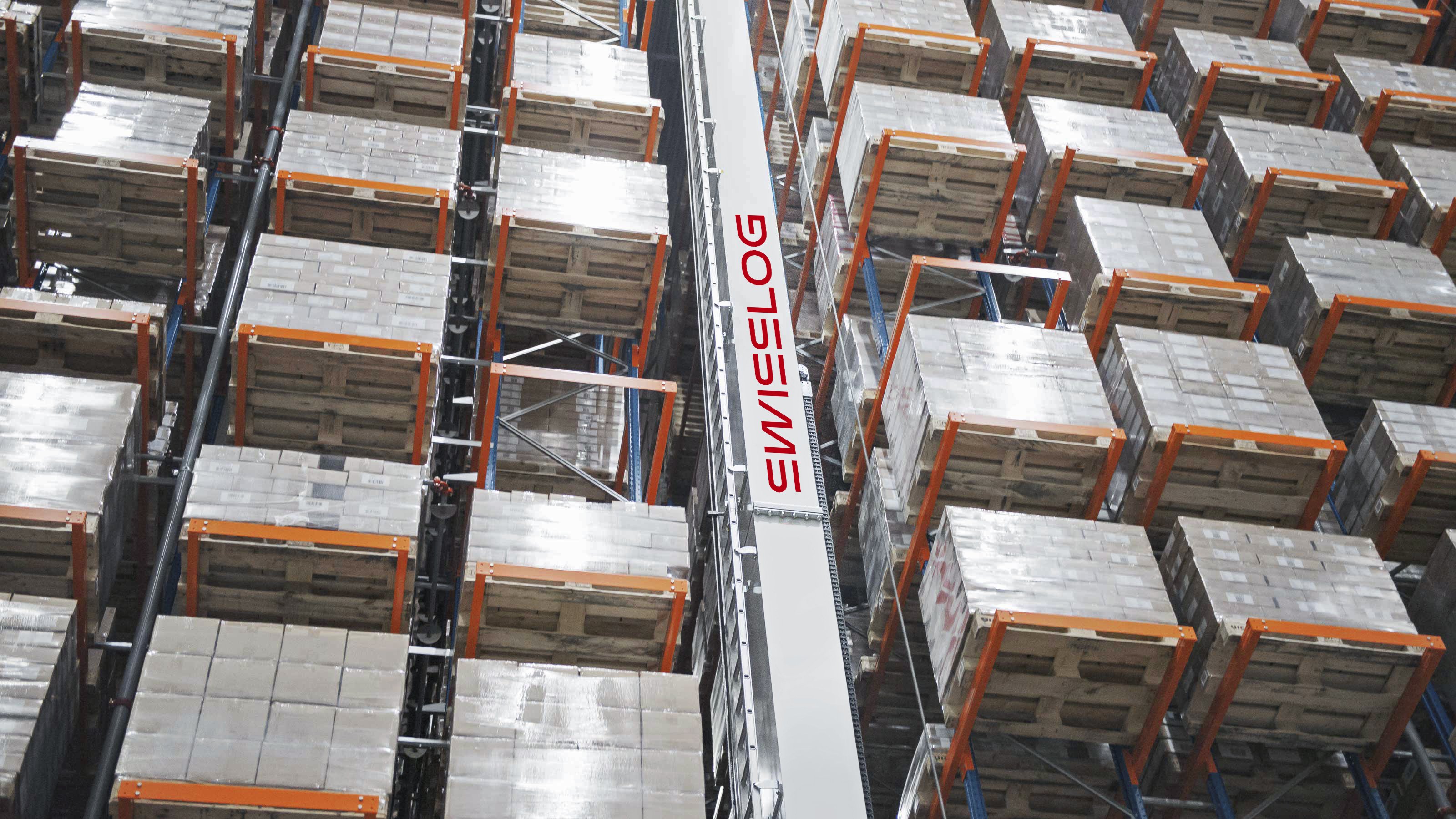
Complementary technologies for an automated shuttle system
A well-designed shuttle can serve as the heart of an automated omnichannel warehouse. But, in many warehouses, there is an opportunity to automate processes beyond picking through technologies that support and work with the shuttle system. These can include:
- Automated Item Picking
Shuttle workstations can be equipped with item picking robots. Swisslog’s AI-based piece picking robot, ItemPiQ, is designed to handle repetitive item picking accurately and safely within a goods-to-person workstation. With its autonomous gripper exchange, ItemPiQ seamlessly adapts to various shapes and sizes, ensuring efficient handling of a wide range of items. - Packaging
Swisslog has successfully integrated our SynQ software with the Packsize custom packaging system. Through this integration, pickers can pick directly to right-sized cartons produced on-demand by the Packsize system. By picking directly to packages created based on the order, the need for extra packaging in cartons is eliminated and freight costs can be reduced. - Case Storage
Swisslog’s Tornado Miniload Crane is an ideal solution for reserve case storage in an omnichannel warehouse, enabling more efficient induction into the shuttle or directly supporting order fulfillment. Like the CycloneCarrier shuttle, Tornado cranes can make effective use of vertical space with heights up to 24 meters. Tornado cranes are also adept at handling a wide variety of product sizes and types, with a load-carrying capacity of up to 250 kg (550 lbs). - Pallet Storage
The Vectura crane is the ideal solution for warehouses seeking to automate pallet storage and retrieval. This energy-efficient system enables versatile and high-performance pallet storage and retrieval to support a light-goods shuttle system. - Automated Product Transport
Swisslog can integrate AGVs, pallet conveyors, and light-good conveyor systems with the shuttle system to automate product movement from receiving or storage to the shuttle and through downstream processes.
With our SynQ software, all these technologies can be managed as one solution, even if they are deployed in stages. SynQ is a modular platform that grows with you and provides a single point of control for your entire solution, ensuring streamlined material flows, efficient operation of each system, and centralized visibility and control of your automated warehouse.
When configured properly and supported with the right software, a shuttle system provides an ideal solution to the challenges faced by general merchandise in keeping stores well-stocked and responding to e-commerce demand variability. Swisslog has the solutions and expertise to ensure you can automate omnichannel fulfillment processes successfully and cost-effectively. For more information on our solutions for omnichannel fulfillment visit our website or contact us.
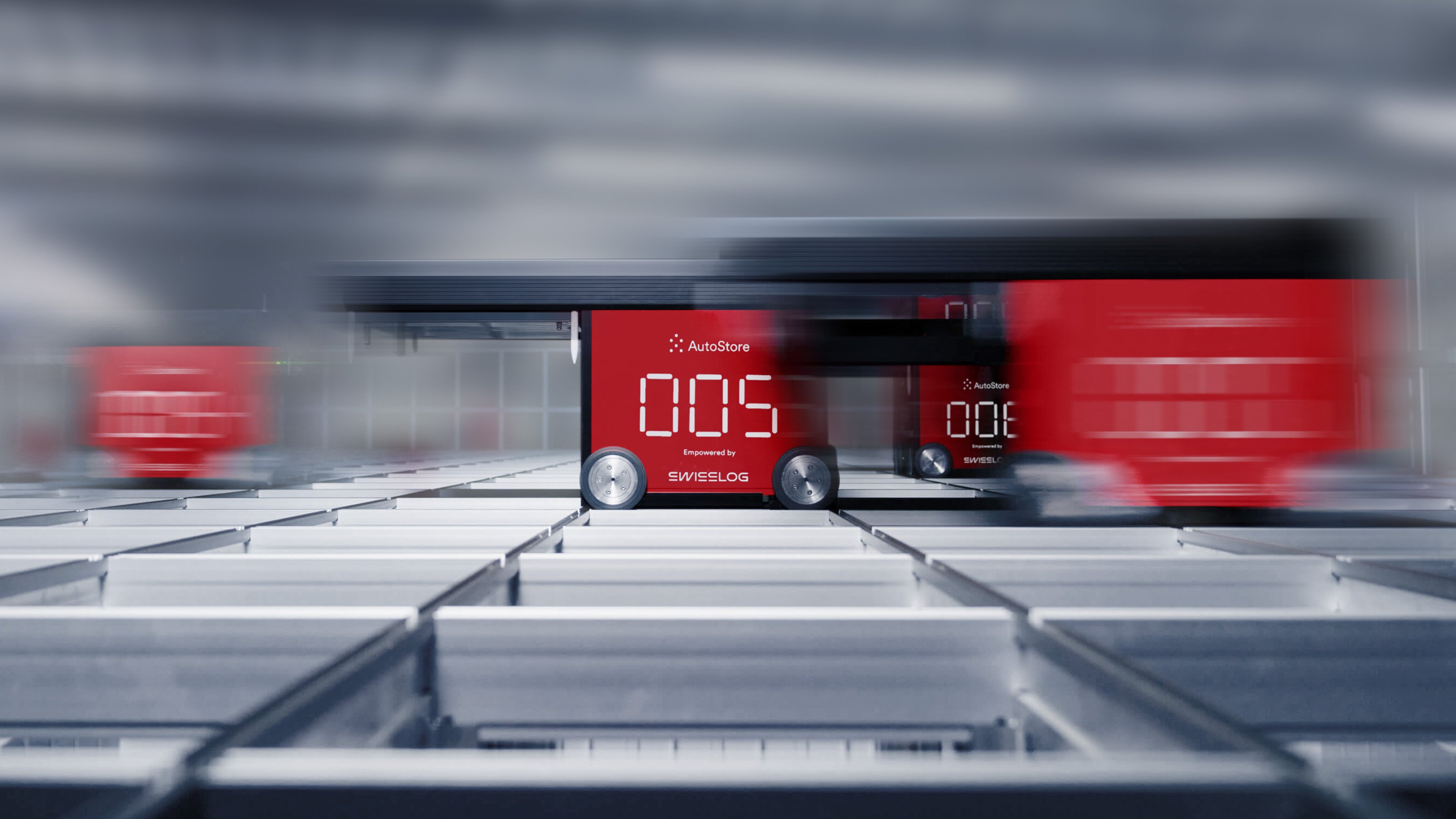
AutoStore offers superior density, throughput, and availability for warehouses. Powered by Swisslog’s SynQ software, it provides significant ROI where applicable, although it isn’t right for everyone.