3 factors that reduce total cost of ownership for a deep-freeze pallet ASRS
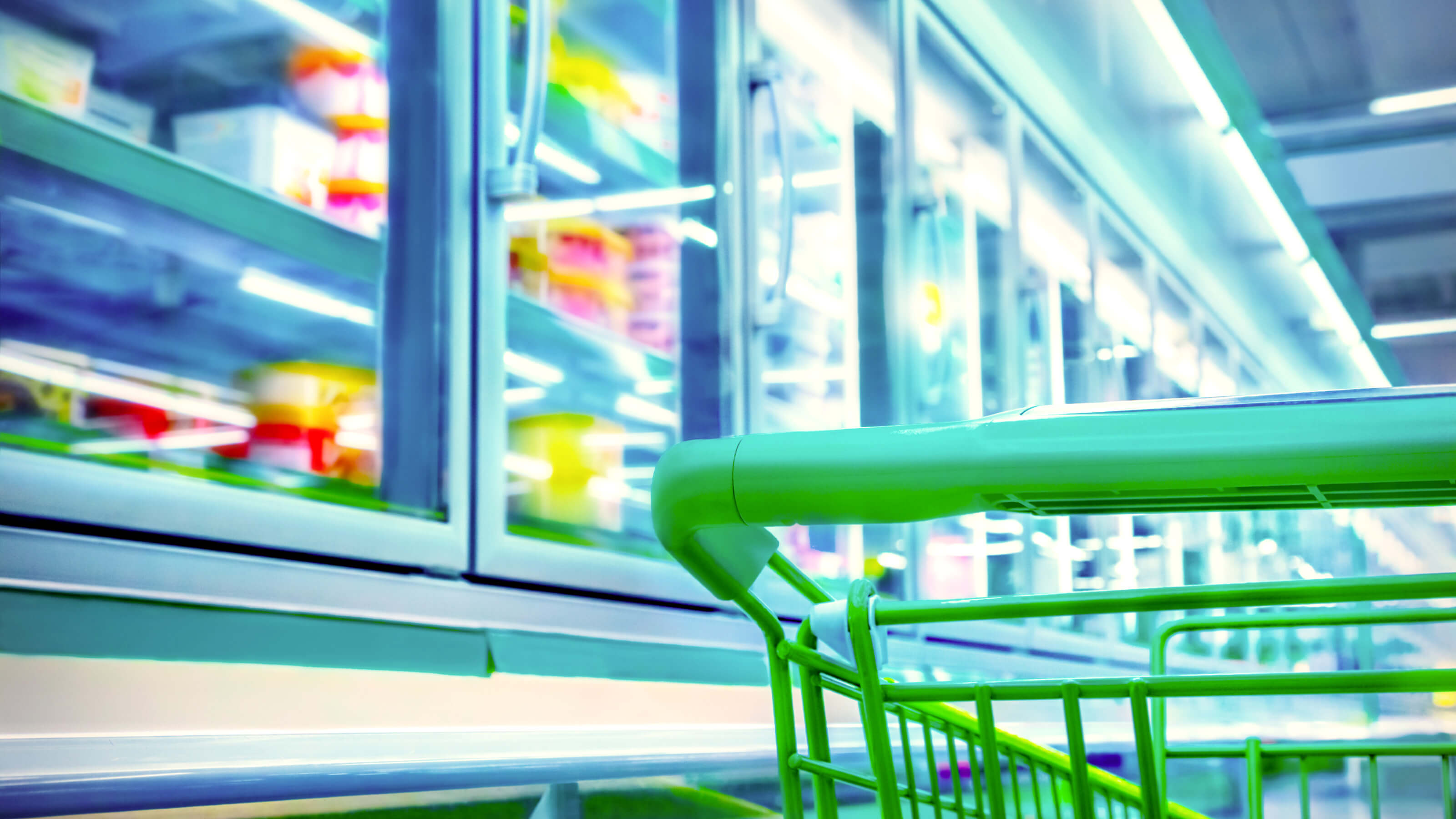
There are more companies than ever offering ASRS solutions for the cold chain and that can lead to varying system costs for what, on the surface, look like similar solutions. However, a holistic view of system costs and capabilities can reveal hidden costs not reflected in the procurement price. Savings realized on the front end will quickly evaporate if the system fails to deliver the expected value or is more expensive to operate. Similar to the automation systems deployed in their manufacturing plants, food and beverage companies should prioritize total cost of ownership and lifetime value when selecting an automation solution for pallet storage and retrieval. Here are three factors that can increase lifetime value and reduce total cost of ownership.
1. Solution and equipment design
Pallet ASRS solutions should be designed to maximize system availability and operating flexibility. Automation providers that take the time to understand your priorities and future plans can configure solutions to current and future requirements. For example, configuring a pallet ASRS with either multi-deep or double-deep storage, or even a combination of both, allows capacity, throughput and inventory management to be optimized over the life of the system. Solution design should also anticipate and support possible extremes in pallet weights and sizes and future automation plans. The position and orientation of the solution within the warehouse can facilitate – or impede – future expansion for volume growth or the addition of complementary automation systems.
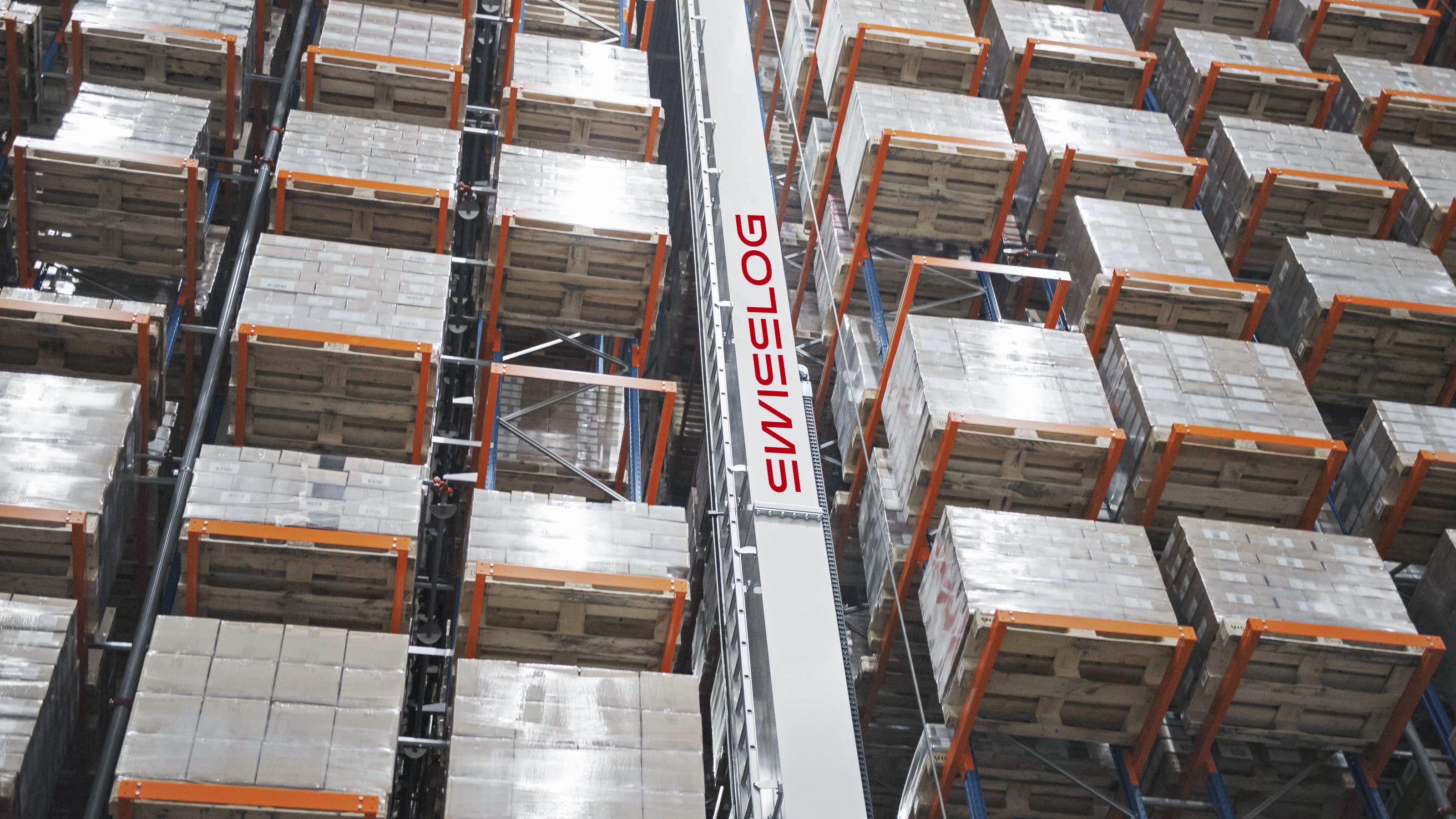
Equipment design also has a direct impact on total cost of ownership and lifetime value. One area to consider is energy costs. Deep-freeze warehouse operators who implement a pallet ASRS will experience significant savings in cooling energy costs compared to conventional warehouse designs due to the density enabled by the ASRS. Crane design can add to these savings. Swisslog Vectura cranes have a mast that is up to 20% lighter than competitive cranes with the same load-bearing capability, requiring less energy to operate.
The other consideration, of course, is minimizing unplanned downtime. Maintaining high availability over the life of a solution requires selecting equipment that has proven reliability in cold chain applications, is easy to service, and is properly maintained. In deep-freeze environments, serviceability is especially important. Look for cranes that position the controls and major components on the floor rather than in the cabin as this provides safer accessibility, reduces the time-to-service, and minimizes the time technicians have to spend in the freezer environment.
2. Automation software capabilities
By automating pallet storage and retrieval, manufacturers and 3PLs can virtually eliminate the human errors that contribute to stockouts and overstock. They also eliminate product damage from forklift interactions, which can result in losses of 10% or more in many warehouses, and improve warehouse safety and ergonomics. But the value of managing inventory with automation should go beyond these savings.
The right automation software can bring greater intelligence to inventory and order management. For example, Swisslog’s SynQ software can manage inventory by batch, expiry date, best-by date or other factors. SynQ also enable inventory separation in multi-client environments with each client’s inventory managed to their business rules, eliminating the need for separate storage areas, increasing system utilization, and enabling common material flows across client boundaries.
SynQ can also calculate the remaining shelf life at delivery for each order to enable product for a particular order to be retrieved based on expected delivery times and customer priority. The speed and predictability of order fulfillment is also improved through capabilities that optimize picking and routing based on order priority, inventory availability and resource capacity, along with sequenced load management and automated staging to outbound shipping for efficient, single-touch trailer loading. If product recalls are required, SynQ can locate impacted products – including those already shipped – based on batch, best-by date, or other information and block and store affected products while issues are being resolved.
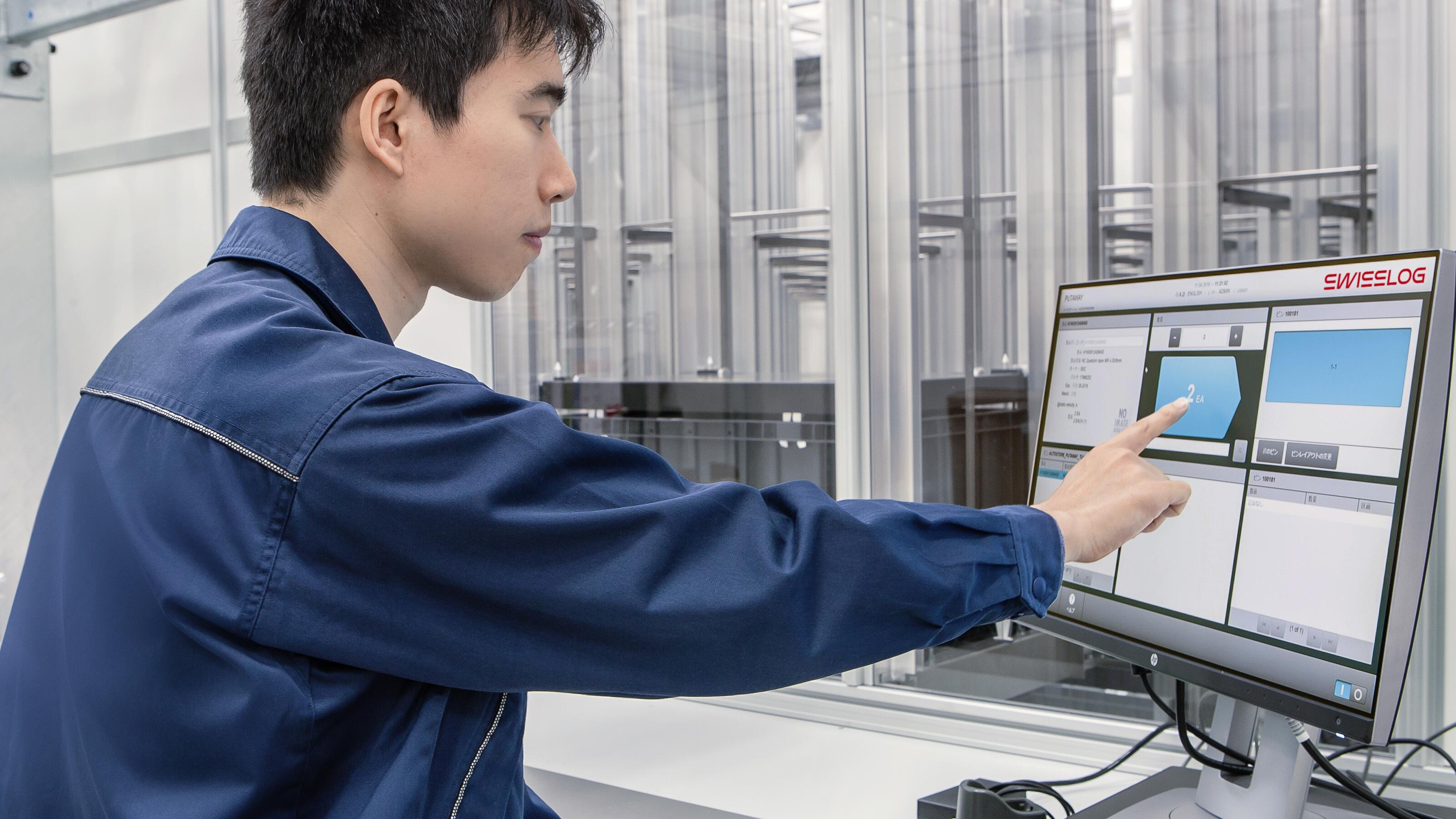
3. Installation support and lifecycle services
Lifetime value starts at installation so be sure the provider you select has disciplined and well-defined implementation, testing, and startup processes and a track record of delivering solutions on-time and on-budget. Start-ups that get delayed due to problems with software integration or commissioning can add to a solution’s costs through missed commitments or supply chain disruption.
How ASRS solutions are maintained and supported has a major impact on system availability and lifespan. If possible, determine upfront whether maintenance will be handled in-house or outsourced as that decision has accounting and tax implications. In either case, equipment manufacturers that provide a robust service organization and work with their customers to enact service strategies that leverage internal resources while providing high-value services from local specialists will help ensure any issues encountered can be resolved quickly.
Whether you’re planning to maintain the system yourself or rely on the equipment manufacturer for service, it's a good idea to plan for two-to-three years of OEM resident service to ensure a smooth transition to automated pallet handling support and maintenance. Also pay particular attention to how a solution provider supports its software. Software issues can generally be resolved quickly and remotely if the solution provider has a stable platform and has invested in the training and resources to provide fast, efficient 24 x 7 help desk support.
Protecting your investment
Automating temperature-controlled warehouse operations through a pallet ASRS represents a major opportunity for food and beverage manufacturers and 3PLs to reduce labor dependencies and operating costs, improve retention and safety, and enhance customer service levels. But not every solution delivers the same value and systems that are unreliable will be much more expensive to operate than ones that deliver high reliability.
Swisslog ASRS solutions are proven reliable in temperature-controlled warehouses, and add value to your operations through the robust capabilities of our SynQ software platform with single-point-of-control. And they are backed by a company you can rely on for single source automation, software, maintenance and support over the life of your solution.
To learn more, speak with our automation specialists.