Quattro domande per capire se AutoStore è adatto alla vostra attività
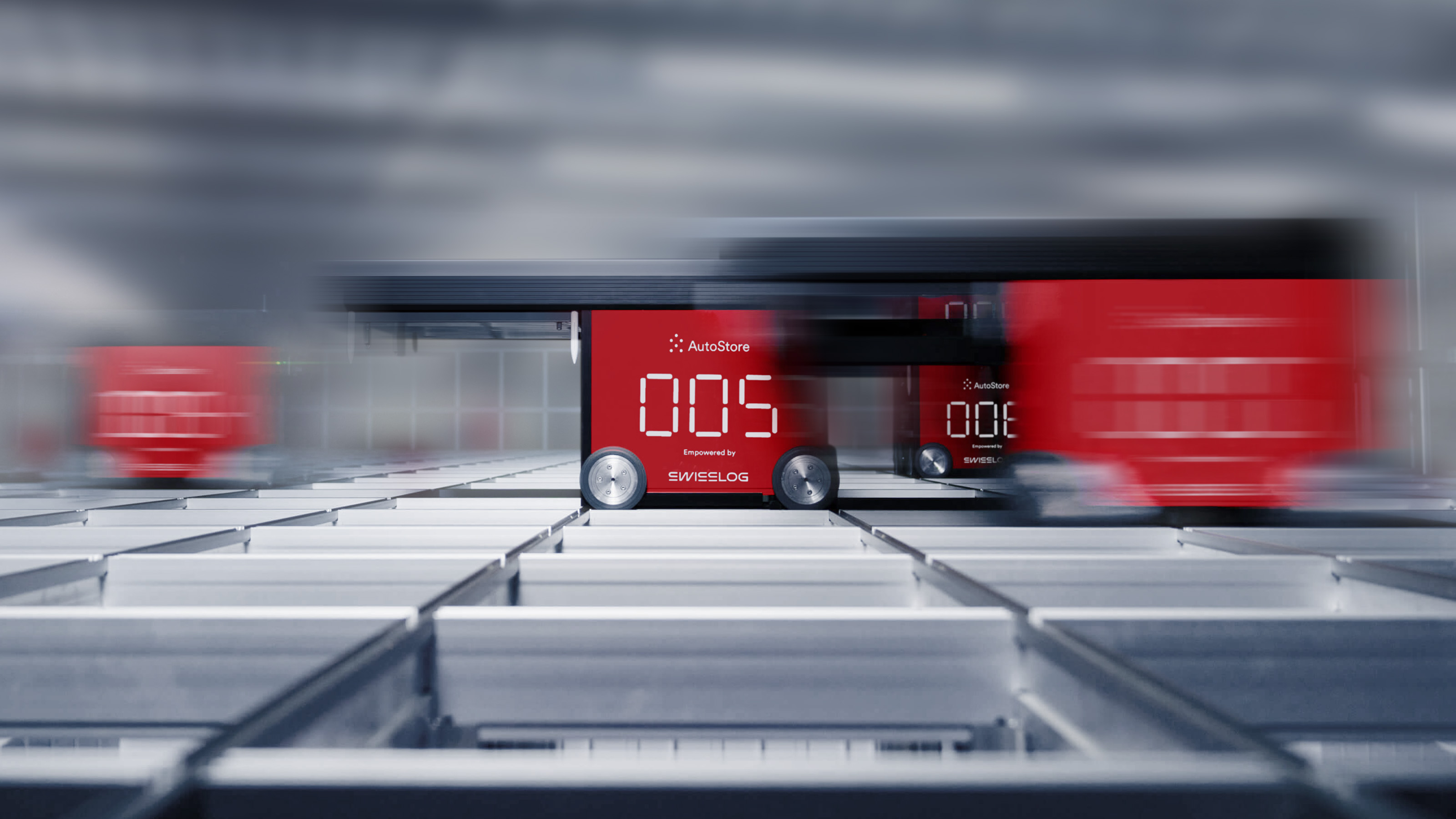
Il vostro inventario è adatto a un sistema AutoStore?
AutoStore è un sistema per piccole merci che utilizza contenitori standardizzati disposti in una griglia 3D per immagazzinare e recuperare i prodotti. Si noti che, sebbene AutoStore sia un sistema per piccole merci, la sua applicazione non è limitata a ordini di piccole dimensioni, come si può vedere suggerito in altri luoghi. Funziona ugualmente bene con ordini grandi o piccoli. La chiave è la percentuale di inventario che può essere prelevata dal sistema e che è determinata dalle dimensioni dei prodotti.
AutoStore può essere configurato con tre dimensioni di contenitori. Ogni dimensione di cassetta ha la stessa larghezza e lunghezza e varia solo in altezza. La larghezza interna di tutte le cassette AutoStore è di 403 mm (15,87“) e la lunghezza interna è di 603 mm (23,74”). Le tre altezze disponibili per i contenitori sono:
- 220 mm (8,66")
- 330 mm (13")
- 425 mm (16,73")
Attualmente, non è possibile utilizzare contenitori di dimensioni diverse nello stesso sistema; se si desidera utilizzare contenitori alti per alcuni prodotti da immagazzinare nel sistema, il sistema dovrà essere configurato con tutti i contenitori alti. Inoltre, ricordate che tutti i contenitori hanno una capacità massima di stoccaggio di 30 kg e che i contenitori possono essere suddivisi con divisori per ospitare più SKU nello stesso contenitore.
Un'altra cosa da considerare quando si valuta quanto il proprio inventario può essere inserito in un sistema AutoStore: più prodotti si possono inserire in un contenitore, più si beneficerà dell'efficienza e della densità del sistema AutoStore. Se un prodotto è così grande che solo un articolo può stare in un contenitore, non ha senso conservarlo in AutoStore. Con il tempo necessario per travasare e prelevare un prodotto da un contenitore, sarà probabilmente più efficiente prelevare quel prodotto manualmente.
Con queste limitazioni, AutoStore è un sistema estremamente versatile che si è dimostrato efficace nella gestione di un'ampia varietà di prodotti per i clienti Swisslog nei settori della moda, del general merchandise, delle parti e dei componenti elettronici e industriali, dei generi alimentari e delle forniture sanitarie.
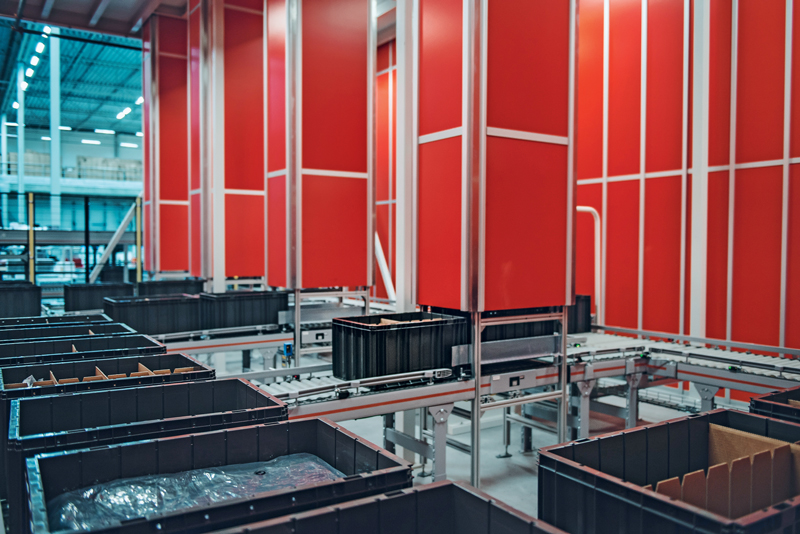
Come si inserisce AutoStore nel vostro magazzino?
Il risparmio di spazio è uno dei vantaggi più importanti del sistema AutoStore. Secondo AutoStore, il suo sistema “può aumentare la capacità di stoccaggio fino a quattro volte rispetto a un magazzino manuale”.
Inoltre, AutoStore presenta diversi vantaggi rispetto ad altre tecnologie “goods-to-person”, in quanto è in grado di adattarsi ai magazzini esistenti. In primo luogo, il suo design consente di configurarlo intorno a pilastri e altre ostruzioni che potrebbero rappresentare una sfida per altre tecnologie. In secondo luogo, può raggiungere un'elevata densità di stoccaggio in magazzini con soffitti bassi. Per i magazzini con soffitti di altezza inferiore a circa 13 metri (40 piedi), AutoStore offre la più alta densità di stoccaggio di qualsiasi altro sistema ASRS per la movimentazione di merci.
Un integratore esperto di AutoStore, come Swisslog, può darvi rapidamente un'idea di quanta metratura consumerà un sistema AutoStore di dimensioni adeguate nel vostro magazzino. In alternativa, se preferite fare i vostri calcoli prima di contattare un integratore, ecco una formula che vi permetterà di fare un calcolo approssimativo.
Innanzitutto, calcolate il volume cubo dell'inventario che sarà immagazzinato nell'AutoStore. Dividere quindi il volume totale per l'utilizzo del cubo di stoccaggio, che in genere è compreso tra 0,22 e 0,27. Infine, dividere il volume per l'altezza prevista della griglia per ottenere una stima dello spazio richiesto.
L'utilizzo del cubo è una misura di quanto il volume disponibile nella griglia sia effettivamente riempito di prodotto. L'utilizzo dei cubi è influenzato dall'intervallo di riempimento dei contenitori, dalle caratteristiche dei prodotti e dalla distribuzione delle scorte nel sistema.
Questi calcoli danno un'idea approssimativa di quanto spazio consumerà l'AutoStore. Tuttavia, Swisslog dispone di una serie di strategie e strumenti che utilizza per ottimizzare l'utilizzo e la densità, per cui tali calcoli non dovrebbero essere utilizzati oltre la fase iniziale di esplorazione. Grazie ai nostri strumenti e alla nostra esperienza, i sistemi AutoStore configurati da Swisslog utilizzano costantemente un numero inferiore di cestini rispetto ai nostri concorrenti, senza compromettere le prestazioni. Questa maggiore efficienza può essere utilizzata per ridurre i costi del sistema o per aumentare i giorni di giacenza (DOH) o il numero di SKU immagazzinate nel sistema senza aumentare i costi.
AutoStore può soddisfare i vostri requisiti di produttività?
La facile configurabilità di AutoStore consente di adattare la produttività del sistema ai requisiti dell'applicazione, ottimizzando i costi di investimento. Ad esempio, se avete bisogno di una maggiore produttività, potete investire in più robot, sia come parte della configurazione iniziale sia dopo che il sistema è già stato installato.
Una delle cose che apprezzerete di più di AutoStore è il modo in cui gestisce l'inventario per consentire un più rapido recupero dei contenitori. Con AutoStore, i prodotti in rapido movimento salgono naturalmente in cima alla griglia, creando un approccio dinamico e automatizzato alla suddivisione delle scorte che ottimizza la produttività.
È inoltre possibile scegliere il numero e il tipo di porte in base ai requisiti di produttività. La porta standard AutoStore Conveyor supporta 50-150 prelievi all'ora, mentre la porta Carousel può supportare fino a 350 prelievi all'ora. La nuova porta Fusion consente velocità fino a 500 prelievi all'ora e permette anche di rinviare al sistema gli ordini completati per il buffering. Per migliorare la velocità e l'accuratezza dei prelievi è possibile utilizzare tecnologie supplementari come pick-to-light e put-to-light.
Un problema da tenere presente, tuttavia, è la potenziale “contesa dei contenitori”, che può limitare la produttività e il rendimento in alcune applicazioni se non viene gestita correttamente. La contesa dei contenitori si verifica quando due porte hanno bisogno dello stesso prodotto nello stesso momento. Anche se il prodotto è distribuito in più contenitori nel sistema - una pratica ottimale per i prodotti ad alta richiesta - la logica di AutoStore sceglierà il contenitore con il minor numero di articoli per ottimizzare la densità. Se il contenitore con il minor numero di articoli è già in fase di recupero per un altro ordine, le altre porte che necessitano di quel prodotto rimarranno inattive finché il contenitore non sarà disponibile.
Il software di controllo SynQ AutoStore di Swisslog ha soluzioni integrate per la contesa dei contenitori. Il software può raggruppare dinamicamente gli ordini e indirizzare gli ordini contenenti lo stesso prodotto alla stessa porta, riducendo al minimo la contesa e aumentando la produttività, consentendo all'operatore di prelevare più ordini dallo stesso contenitore. SynQ per AutoStore offre inoltre agli utenti la flessibilità di indirizzare la logica di AutoStore a dare priorità alla produttività rispetto alla densità, scegliendo il contenitore che può essere presentato più velocemente piuttosto che quello con il minor numero di articoli. Questa funzionalità può essere attivata durante i periodi di picco della domanda e disattivata quando i volumi tornano alla normalità.
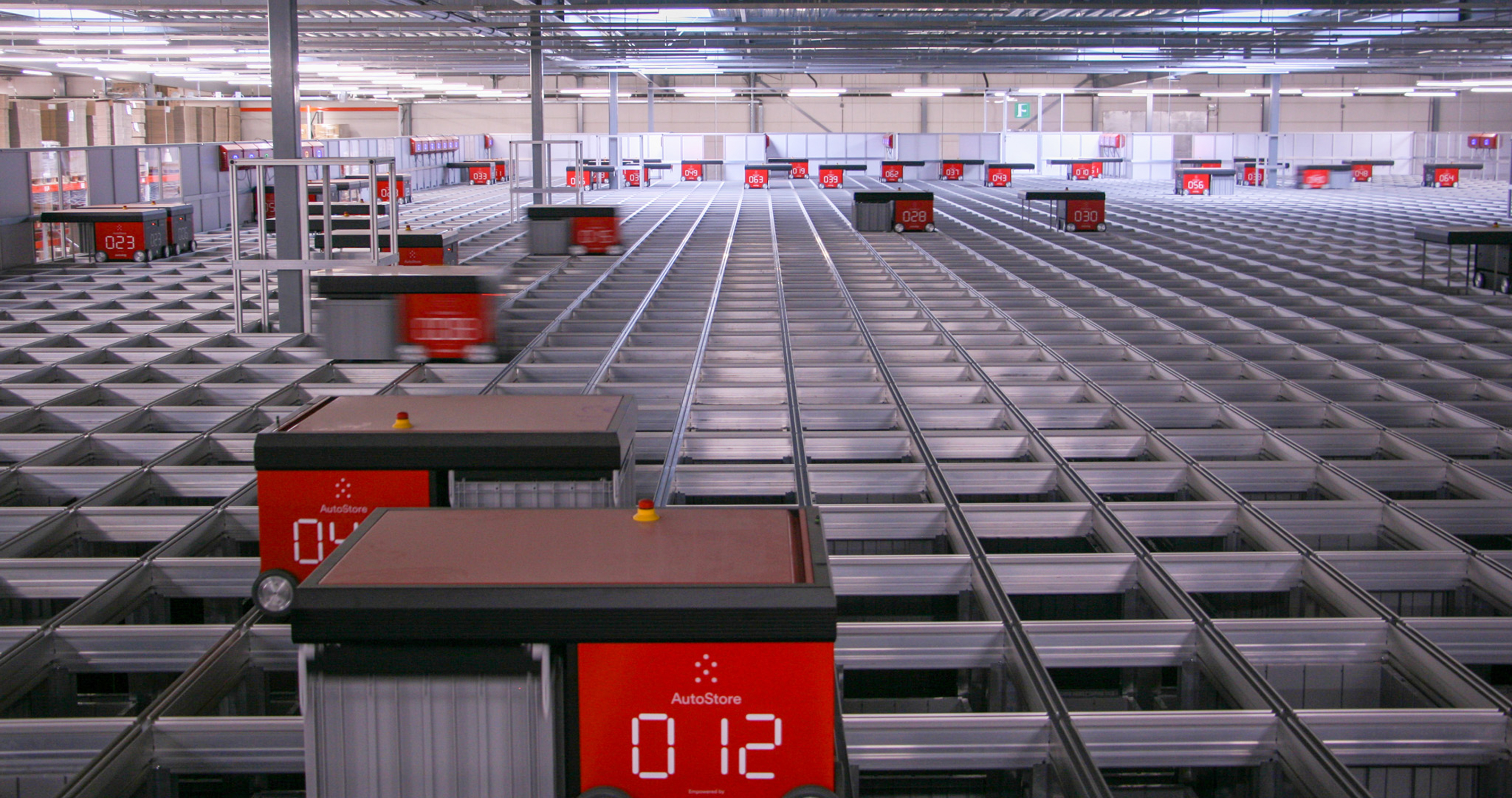
Quale ROI ci si deve aspettare?
Il ROI di ogni azienda sarà diverso in base alle dimensioni del sistema, ai processi di picking esistenti e ad altre variabili. In generale, il ROI di un sistema AutoStore si baserà principalmente sul risparmio di manodopera, sulla maggiore precisione di prelievo e sul migliore utilizzo dello spazio.
Secondo AutoStore, un operatore AutoStore può fare il lavoro di quattro o cinque addetti al picking manuale e noi vediamo regolarmente una precisione di picking superiore al 99% nelle nostre implementazioni AutoStore. Con la densità fornita dal sistema AutoStore, i nostri clienti spesso scoprono di poter prolungare la vita del loro attuale magazzino, evitando costi di locazione più elevati o di sviluppo del magazzino, nonché le spese e i disagi legati al trasferimento del magazzino.
In quasi tutti i casi in cui AutoStore è adatto all'azienda, vediamo che il ROI è inferiore a cinque anni e che il ROI è comunemente inferiore a tre anni. Nell'ambito del nostro processo di configurazione, possiamo aiutarvi a calcolare il ROI previsto per la vostra attività.
Fare il passo successivo
In Swisslog abbiamo installato più di 400 sistemi AutoStore e grazie a questa esperienza abbiamo continuamente aggiunto nuove funzionalità al nostro software di controllo, semplificato i processi di installazione e messa in servizio e sviluppato configurazioni standard che funzionano per la maggior parte delle aziende. Se siete pronti a fare il passo successivo e a vedere come configurare AutoStore per la vostra attività, contattateci.
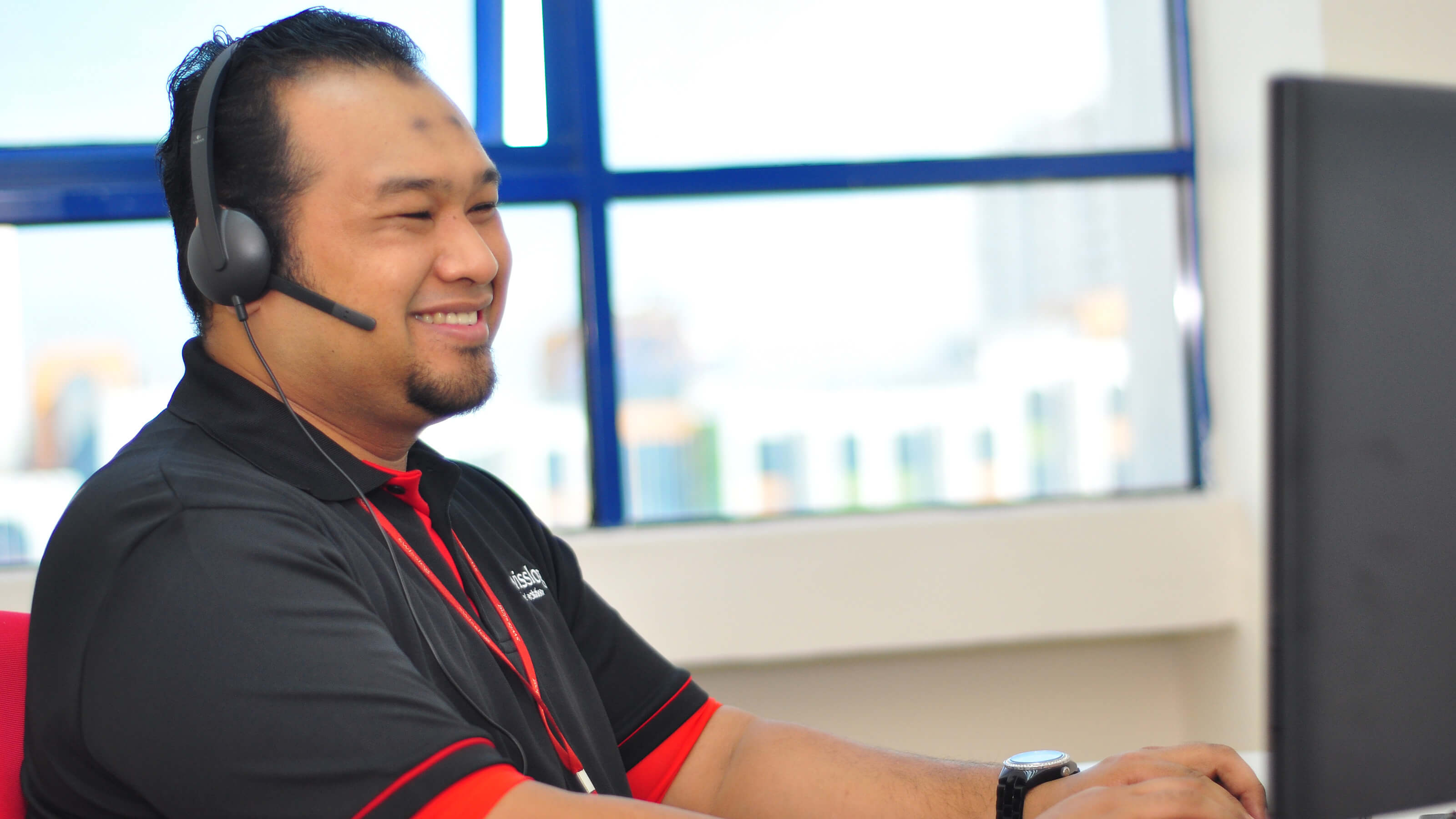
Scoprite il ruolo cruciale della manodopera specializzata nell'automazione del magazzino. Scoprite come i team dedicati all'assistenza clienti gestiscono e mantengono sistemi all'avanguardia.