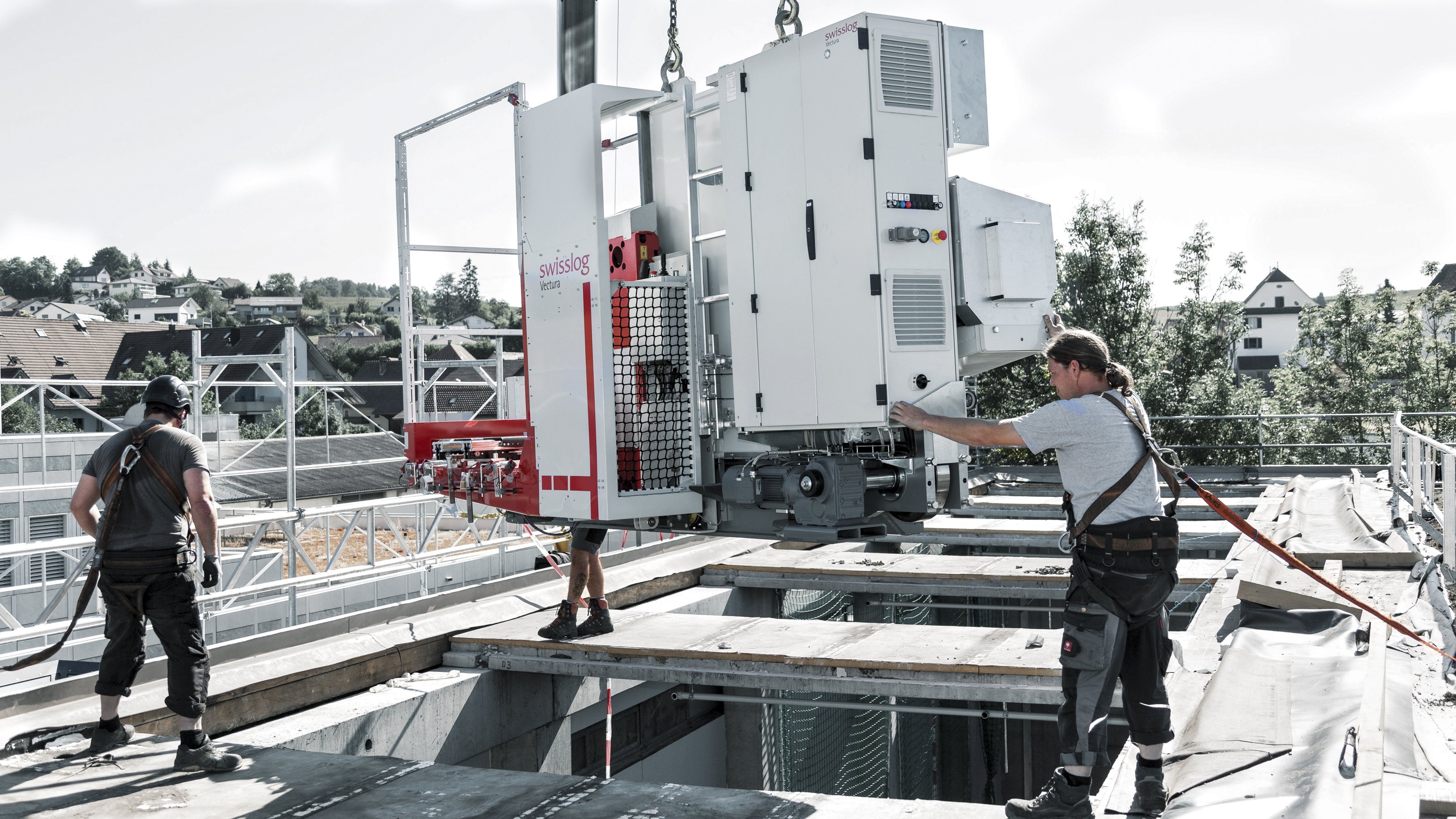
Key considerations for retrofitting a warehouse with AS/RS
What to consider before retrofitting a warehouse with AS/RS. Understand the types and configurations available. How to choose the systems to suit your business operation and existing structures.
- Retrofitting your warehouse: key considerations for integrating AS/RS systems
- Key considerations for retrofitting a warehouse with AS/RS
- Leveraging BIM for warehouse retrofitting
- Managing mixed pallet types in a warehouse retrofitting process
- Preparing for a successful retrofit
- Evaluating infrastructure and selecting the right AS/RS
- Integration, space optimization, and cost management
- Implementation, training, and continuous improvement
1 Retrofitting Your Warehouse: Key Considerations for Integrating AS/RS Systems
Retrofitting an existing warehouse with an Automated Storage and Retrieval System (AS/RS) is a complex process that can significantly enhance operational efficiency, but it requires careful planning and consideration. When updating a warehouse, several critical factors need to be addressed to ensure a seamless integration of the AS/RS technology into the existing infrastructure.
When considering retrofitting your warehouse with an Automated Storage and Retrieval System (AS/RS), the first critical step is understanding the types and configurations of AS/RS available. These systems are highly adaptable, capable of being tailored to meet various warehouse needs. Technologies such as shuttles, cranes, autonomous mobile robots (AMRs), and vertical lift modules (VLMs) offer different capabilities, and the specific configuration—whether it’s single deep, double deep, or dual crane setups—will depend on your storage requirements and the space available in your facility. Selecting the right configuration is crucial to ensuring that the AS/RS maximizes both efficiency and effectiveness within your warehouse environment.
Once the appropriate system is chosen, the benefits of implementing AS/RS become apparent. One of the most significant advantages is the increased storage density that these systems offer. By making optimal use of vertical space, AS/RS allows warehouses to maximize storage capacity without the need for horizontal expansion, which is often more costly and logistically challenging. Beyond space utilization, AS/RS enhances inventory accuracy by automating the placement and retrieval of goods, thus reducing the chances of human error. This automation not only lowers labor costs by minimizing the need for manual handling but also improves safety and ergonomics within the warehouse, which is especially beneficial in environments where labor shortages are a concern or where precision and safety are critical to operations.
In essence, by carefully selecting the right AS/RS configuration and understanding its operational benefits, warehouse operators can significantly enhance the overall efficiency and productivity of their facilities.
2 Key Considerations for Retrofitting a Warehouse with AS/RS
Retrofitting a warehouse with an Automated Storage and Retrieval System (AS/RS) involves several critical considerations to ensure a successful transformation. Among the core components of such systems, stacker cranes stand out as essential tools that provide precise control over the storage and retrieval of goods. These cranes automate tasks traditionally prone to human error, such as incorrect item placement, retrieval mistakes, and inventory management inaccuracies. By reducing the potential for these errors, stacker cranes contribute to more efficient warehouse operations, minimizing delays and enhancing overall reliability. Additionally, stacker cranes are designed to withstand various environmental conditions, including extreme temperatures and high humidity, making them suitable for specialized environments like cold storage facilities.
One of the primary goals when retrofitting a warehouse is to maximize space efficiency. AS/RS technologies, including stacker cranes, are designed to operate in narrow aisles and reach significant heights, enabling high-density storage solutions. This not only optimizes the use of available space but also increases throughput, a critical factor for high-volume warehouses that require rapid and efficient handling of large loads. The ability of modern stacker cranes to operate at high speeds further enhances their suitability for environments where speed and accuracy are paramount.
Integration with advanced Warehouse Management Systems (WMS) is another vital aspect of a successful AS/RS retrofit. A robust WMS provides real-time data and control, allowing for better coordination between storage and retrieval processes, inventory management, and other warehouse operations. This seamless integration ensures that all systems work together effectively, optimizing overall operational efficiency.
For warehouses with outdated Warehouse Management Systems, upgrading or replacing these systems is often necessary to ensure compatibility with new AS/RS technology. Whether upgrading the existing WMS, implementing warehouse optimization solutions, or migrating to a modern cloud-based system, each option offers benefits such as improved scalability, enhanced functionality, and better integration with new technologies.
Cost, flexibility, and scalability are also crucial considerations when retrofitting a warehouse with AS/RS technology. While the initial investment can be significant, the modular design of many AS/RS solutions allows for phased implementation and scalability. This means that the system can grow and adapt as your business evolves, offering a flexible solution for a wide range of operational needs. Balancing upfront costs with potential long-term savings in labor, space utilization, and operational efficiency is essential to justify the investment.
Retrofitting a warehouse comes with its challenges, particularly when it comes to assessing the existing infrastructure. Evaluating the current layout, the types of goods handled, and the desired level of automation are critical steps in determining the compatibility of AS/RS technologies with your facility. Special storage needs, such as temperature control, must also be addressed to ensure the system meets all operational requirements.
Space constraints are a common challenge in retrofitting projects. Conducting a comprehensive space assessment is crucial to identify potential areas for equipment placement and determine where reconfiguration may be necessary. Utilizing advanced modeling and simulation tools, such as Building Information Modeling (BIM), can help optimize space utilization and system layouts before implementation, reducing the risk of costly errors.
2.1 Leveraging BIM for Warehouse Retrofitting
Building Information Modeling (BIM) has become a crucial tool for retrofitting warehouses, offering a sophisticated approach to upgrading existing structures. When a warehouse needs to integrate new systems, like Automated Storage and Retrieval Systems (AS/RS), or improve its efficiency, BIM provides a detailed digital model that streamlines the entire retrofitting process.
BIM starts by creating an accurate 3D representation of the existing warehouse, capturing every structural element and system. This comprehensive model allows project teams to assess the current state of the warehouse and identify how new upgrades can be seamlessly integrated. By simulating various design scenarios within this model, architects and engineers can visualize the impact of proposed changes, ensuring that new systems fit well within the existing space.
One of the standout features of BIM is its ability to detect potential clashes between new and existing infrastructure. For instance, if a new AS/RS system might interfere with current utility lines, BIM identifies these conflicts before construction begins, saving time and money by avoiding costly on-site corrections.
Cost estimation is another area where BIM excels. By incorporating financial data directly into the model, project managers can forecast the costs associated with materials, labor, and timelines, allowing for more accurate budgeting and financial planning.
Phased implementation, often necessary in retrofitting projects, is made easier with BIM. It helps plan construction in stages, ensuring minimal disruption to ongoing operations. Whether it’s upgrading energy systems, adding new technology, or reconfiguring storage layouts, BIM provides a roadmap that keeps the project on track.
Even after the retrofit is complete, BIM continues to serve as a valuable resource for facility management. The digital model reflects all the changes made, providing a detailed reference for future maintenance or upgrades, ensuring that the warehouse operates efficiently long after the retrofit is finished.
In essence, BIM is not just a design tool but a comprehensive solution for managing the complexities of warehouse retrofitting, making it an indispensable asset in modern warehouse management.
Another challenge in older warehouses is managing mixed pallet types, which can disrupt automated equipment.
2.2 Managing Mixed Pallet Types in a Warehouse Retrofitting Process
When retrofitting a warehouse with an Automated Storage and Retrieval System (AS/RS), one of the significant challenges that often arises is managing mixed pallet types. Older warehouses frequently use a variety of pallet sizes and materials, which can disrupt the efficiency of automated systems. To ensure smooth operation and optimize the benefits of AS/RS, it is essential to address this issue carefully.
Understanding the Challenges of Mixed Pallet Types
Mixed pallet types can pose several problems in an automated environment. Variations in size, material, and condition can lead to operational inefficiencies, such as misalignment in automated racking systems, increased wear and tear on equipment, and higher rates of pallet jams or misfeeds. Different pallet types may not interact uniformly with automated handling equipment like conveyors, stacker cranes, or shuttle systems, resulting in inconsistent performance and increased downtime.
Conducting a Comprehensive Pallet Assessment
The first step in managing mixed pallet types is to conduct a thorough assessment of the existing pallet inventory. This involves cataloging the different pallet types currently in use, including their dimensions, material (wood, plastic, or metal), and condition. Identifying the frequency of use and the specific areas where different pallet types are deployed will provide insights into how these variations might impact the new automated system.
During this assessment, it’s also important to evaluate the condition of the pallets. Damaged or worn pallets can cause significant disruptions in automated processes, so it’s crucial to identify and remove any pallets that are no longer suitable for use. Standardizing pallet quality within your operations can reduce the risk of equipment malfunctions and improve overall system reliability.
Upgrading to Compatible Pallets
One of the most effective ways to manage mixed pallet types is to transition to a more standardized pallet system. This may involve upgrading to pallets that are specifically designed for compatibility with automated systems. For example, plastic pallets are often preferred in automated environments because they offer uniformity in size and shape, are less likely to splinter or break, and provide better consistency for automated handling equipment.
Switching to a standardized pallet type can be a significant investment, but it pays off by reducing operational disruptions and improving the efficiency of the AS/RS. Moreover, plastic pallets tend to have a longer lifespan than wood pallets, which can result in cost savings over time.
Implementing Pallet Segregation and Labeling Strategies
If transitioning to a single pallet type is not feasible, implementing segregation and labeling strategies within the warehouse is essential. This approach involves designating specific areas for different pallet types and ensuring clear labeling to minimize confusion. By segregating pallets according to type and ensuring that each area of the warehouse uses only compatible pallets with the local AS/RS equipment, you can significantly reduce the risk of operational issues.
Clear labeling and signage are also critical to ensure that warehouse staff can easily identify the correct pallet types for different areas of the operation. This minimizes the risk of mix-ups, which could lead to automated system failures or inefficiencies.
Utilizing Pallet Changers and Adaptors
In cases where multiple pallet types must be used, investing in pallet changers or adaptors can be a practical solution. Pallet changers allow for the quick and efficient transfer of goods from one pallet type to another, ensuring that the correct pallet type is used with automated systems. This can be particularly useful in facilities where goods are received on different types of pallets but need to be transferred to a standardized pallet for internal processing.
Pallet adaptors are another option that can allow certain non-standard pallets to be used within an automated system. These adaptors can modify the pallet’s footprint to make it compatible with the AS/RS, reducing the need for complete pallet replacement.
Training and Best Practices
Training warehouse staff on the importance of using the correct pallet types and following proper handling procedures is vital for maintaining system efficiency. Staff should be well-versed in the warehouse’s pallet segregation and labeling strategies and understand how to use pallet changers and adaptors effectively.
Regular training sessions and updates on best practices can help ensure that everyone involved in warehouse operations is aligned with the goal of minimizing disruptions caused by mixed pallet types.
Long-Term Strategy: Moving Toward Standardization
While immediate solutions like pallet changers and segregation can mitigate issues, the best long-term strategy is to move towards greater standardization of pallet types. Standardizing pallets across the warehouse reduces complexity, lowers the risk of errors, and enhances the overall efficiency of the automated system. It also simplifies maintenance and reduces the wear and tear on automated equipment, as the system is optimized for a single pallet type.
Standardization should be approached gradually, starting with the most critical areas of the warehouse and expanding as budget and operational constraints allow. Over time, this strategy will lead to a more streamlined, efficient, and cost-effective operation.
By understanding the challenges posed by different pallet types, upgrading to compatible pallets, implementing segregation and labeling strategies, and investing in tools like pallet changers, you can significantly reduce operational disruptions. Ultimately, moving towards standardization will offer the greatest long-term benefits, ensuring that your automated systems run smoothly and efficiently, supporting the overall goals of your warehouse operations.
3 Preparing for a Successful Retrofit
Strategic Priorities for Retrofitting a Warehouse with AS/RS
3.1 Evaluating Infrastructure and Selecting the Right AS/RS
The foundation of a successful warehouse retrofit with an Automated Storage and Retrieval System (AS/RS) lies in a thorough evaluation of your existing infrastructure. This process involves a detailed assessment of the current layout, identifying structural limitations and potential areas for optimization. This evaluation informs the selection of the most appropriate AS/RS technology—be it stacker cranes, shuttles, or vertical lift modules—that best suits your operational needs. Scalability is a crucial consideration, ensuring the chosen system can grow alongside your business and adapt to future demands.
3.2 Integration, Space Optimization, and Cost Management
Once the ideal AS/RS technology is selected, the focus shifts to seamlessly integrating it with your existing Warehouse Management System (WMS) and other operational technologies. Effective integration is vital for maintaining streamlined operations. Additionally, optimizing your warehouse space by maximizing vertical storage and fine-tuning aisle configurations can significantly enhance storage density and throughput. A strategic approach to cost management is also essential balancing the initial investment with anticipated long-term savings, such as increased efficiency and reduced labor costs, ensures the retrofit delivers substantial value over time.
3.3 Implementation, Training, and Continuous Improvement
The final priority in retrofitting your warehouse is executing a smooth implementation process. A phased rollout of the AS/RS minimizes disruptions and allows for testing and refinement before full deployment. Comprehensive training for your staff is critical to ensure they are well-prepared to operate the new system effectively. Beyond implementation, continuous monitoring and regular updates are necessary to maintain system efficiency and support ongoing growth. This commitment to continuous improvement will ensure that your warehouse remains competitive, efficient, and capable of meeting future challenges.