3 questions food and beverage manufacturers should ask automation suppliers
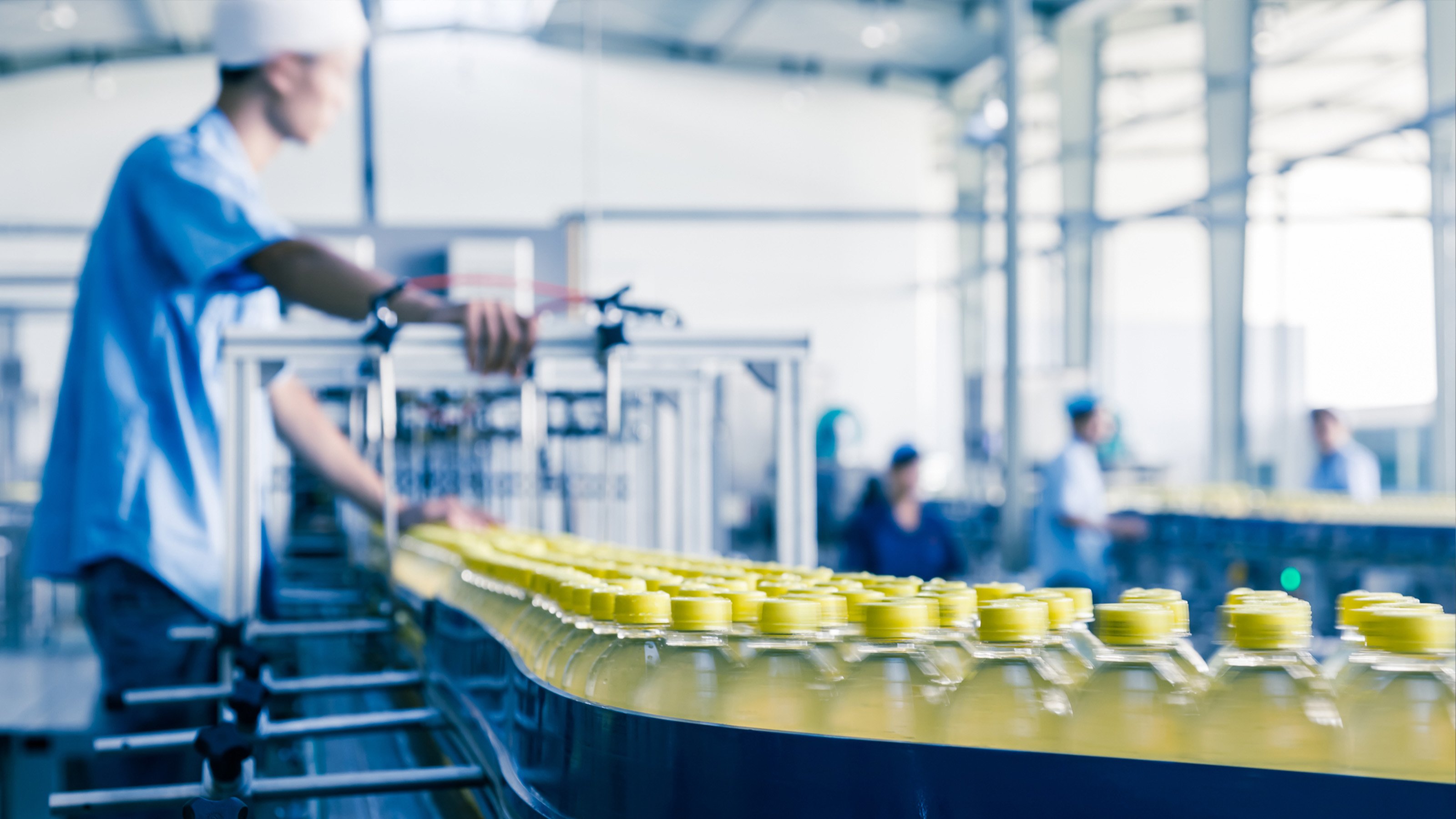
By automating key supply chain processes, food and beverage manufacturers can delay or eliminate the need to open new facilities and reduce their exposure to labor uncertainty, helping future proof the food and beverage supply chain while potentially reducing operating costs.
Automated storage and retrieval systems (ASRS), for example, enable manufacturers to significantly increase storage density and throughput for inbound packaging materials and outbound pallets, which is particularly valuable as real estate and warehouse development costs continue to escalate. Automated or semi-automated palletizing systems provide similar benefits—reducing the space and labor required to create mixed-SKU pallets—to help manufacturers adapt to changing order profiles.
So, the business case for automation has never been stronger and the challenge shifts to choosing among the multitude of automation suppliers to ensure you get a solution that meets current needs while delivering high value over a long life. Here are three questions to help separate the contenders from the pretenders.
1. "What’s your track record in our industry?"
Automation has a long history in the food and beverage supply chain so it’s not unreasonable to expect an automation provider to have a track record in the industry that stretches back several decades. Swisslog, for example, has automation systems that have been in continuous operation for more than 30 years at multiple food and beverage manufacturing sites.
That experience does more than demonstrate equipment quality and reliability. It ensures a supplier is well-grounded in the industry and understands requirements and how they have changed over time. It also serves as the foundation for building deep organizational expertise. From solution design through lifecycle support, a supplier’s industry experience adds value to every phase of a manufacturer’s automation journey.
The impact can be especially noticeable in installation and commissioning where experience can make the difference between going live on time and on budget and missed deadlines and expensive delays. Customer references are essential to the vendor selection process, but it can also be worth the time to look beyond the references provided to get a sense of a company’s depth of experience and reputation in the industry.
2. "How well does your automation software support process efficiency, inventory management, and traceability?"
The software that controls automation is at least as important to the success of a project as the automation technology itself and that importance should be reflected in the supplier selection process.
Key software requirements for food and beverage manufacturers tend to center on inventory management, traceability and process efficiency. Can the automation software manage inventory based on batch, expiry date, best-by date or any other factors important to your customers? Can it support detailed tracking of movements within the warehouse, both in terms of stock changes and physical location, to ensure traceability? How does it enable efficiency across manual and automated processes, and does it allow you to access and control all aspects of the operation from a single interface?
A mature, modular software platform that includes WMS, WES and ACS functionality, such as the Swisslog SynQ platform, will have all of these capabilities included in the standard offering.
Beyond functionality, take the time to learn how software is developed and managed as these “behind-the-scenes” processes can have a direct impact on operations. Software is continually evolving so be sure your provider has a multi-year product roadmap, integrates security into design and implementation processes, and has a well-defined plan for technical upgrades. Also, find out if the same platform is used in all regions. A global platform enables software standardization across locations and also allows the provider to focus resources on advancing and supporting one platform rather than allocating resources and expertise across multiple systems.
3. "How are solutions supported across their lifecycle?"
Every automation system requires regular maintenance and ongoing software support. But it’s easy to overlook the importance of these capabilities until a site is down for days while you’re waiting for a technician to travel in from another region or hours because of slow response from software support specialists.
At minimum, food and beverage manufacturers should ensure that local hardware support is available and compare average response times and first-time resolution rates for the suppliers they are considering working with.
The other factor that should be considered in lifecycle planning is how automation deployed today will adapt to future product and market changes, which may be unknown at the time the system is installed. Can the system be scaled to provide more storage or higher throughputs; can it be easily integrated with complementary automation systems, such as those used in automated or semi-automated mixed-SKU palletizing; and does the supplier have standardized modernization programs that can extend solution life as technology advances?
With today’s automation technologies, solutions can be designed to meet current requirements cost effectively while maintaining the flexibility to continue to deliver value as supply chain requirements change.
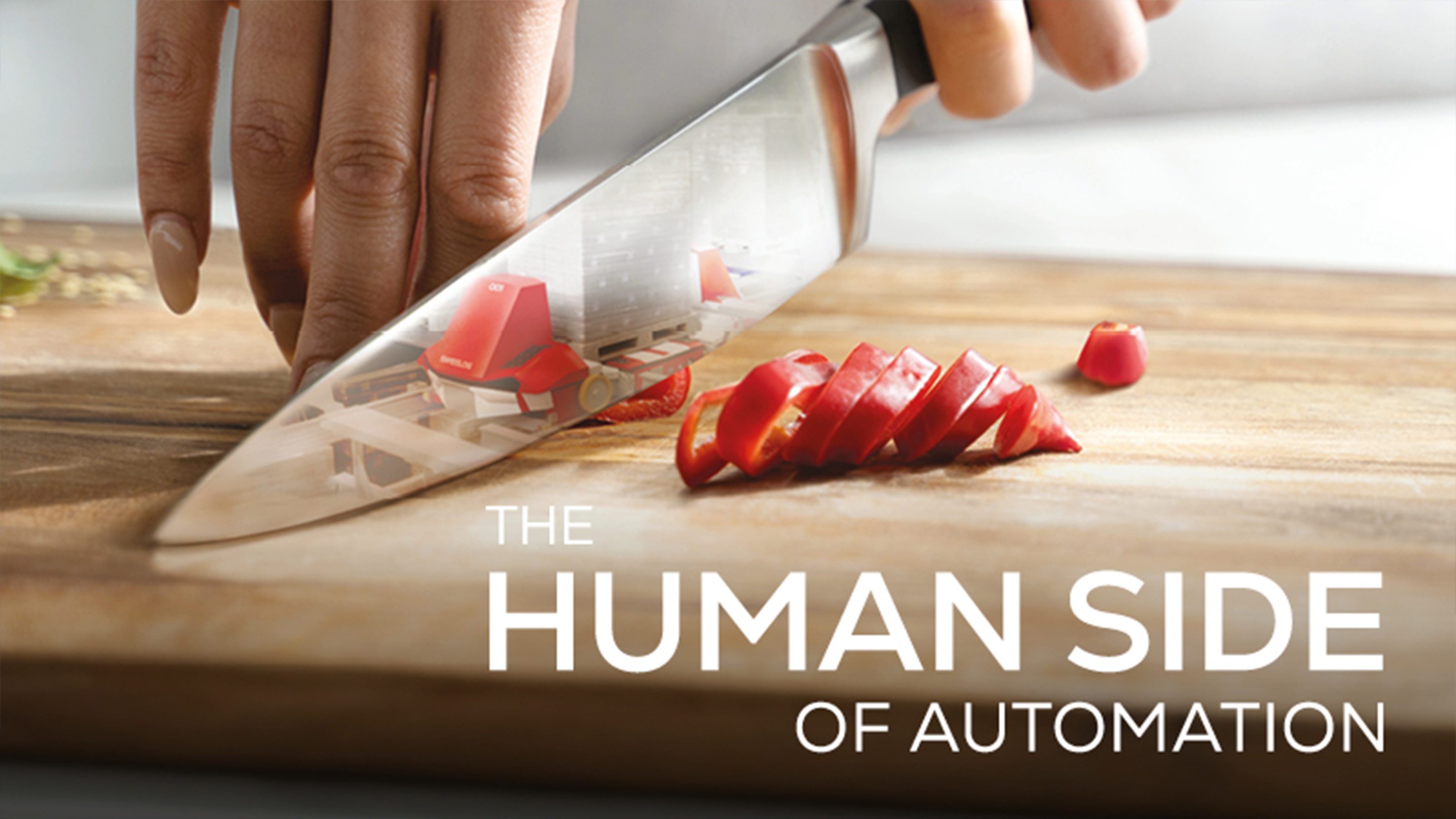
Automation that works for food and beverage manufacturers
Swisslog has decades of experience providing automation solutions for the food and beverage industry with hundreds of solutions in operation. Our mature and proven portfolio of technologies is designed to meet the needs of food and beverage manufacturers through standardized solutions that simplify operation, management and maintenance. And our modular hardware and software enables configurability, scalability and operating flexibility, backed by industry-leading lifecycle support.
To learn more, visit our website or contact us.
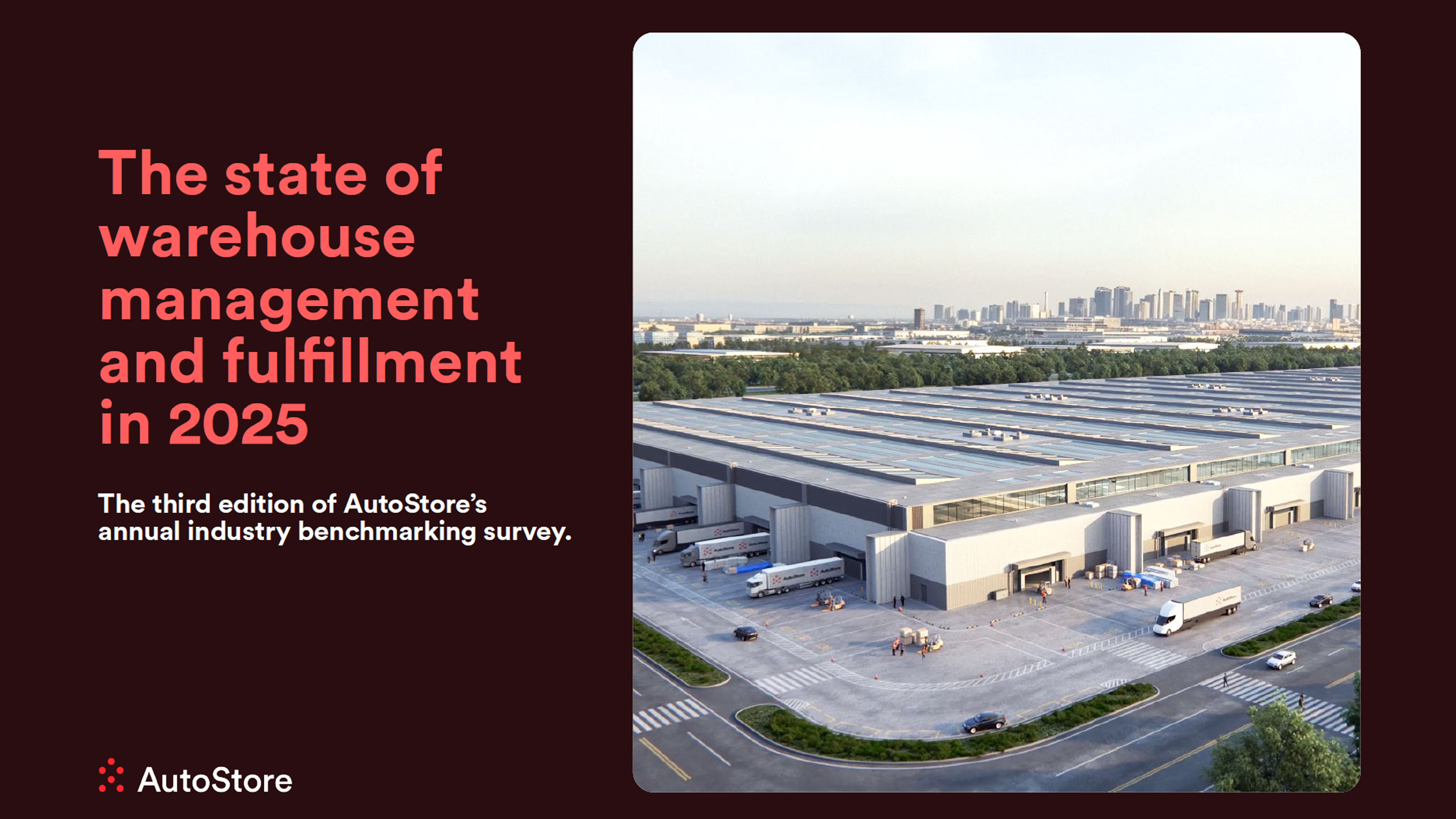
AutoStore’s latest State of Warehouse Management and Fulfillment report, based on insights from 300+ global supply chain leaders, highlights 2025 warehouse priorities & benchmarks automation adoption.