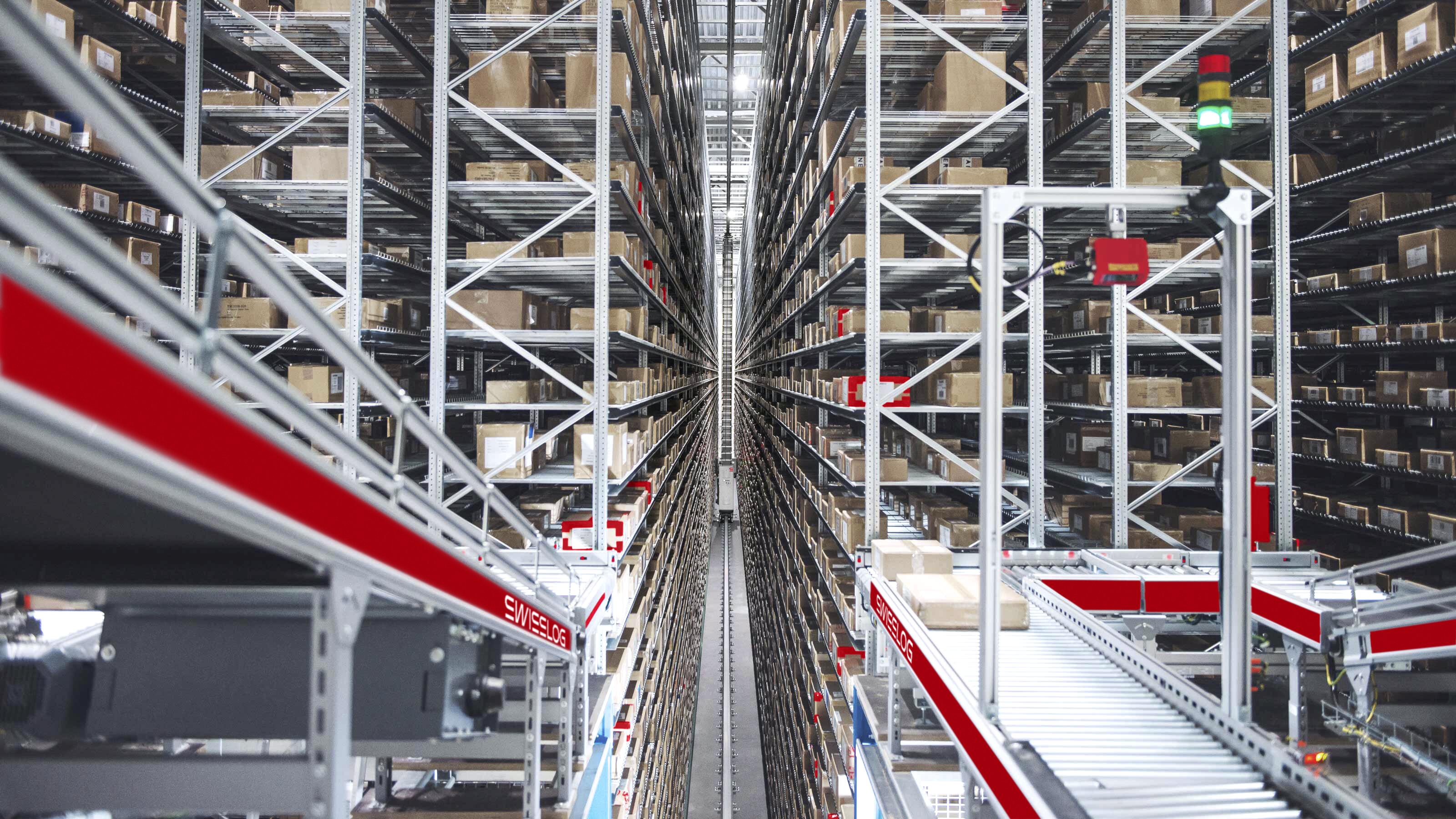
Mini-load AS/RS systems for smaller items storage
Mini-load AS/RS for the storage of smaller items such as totes, cartons and trays. Latest cutting-edge technologies explored in detail. Choosing the right Mini-load system for your warehouse.
- Mini-load AS/RS: streamlining the storage of smaller items
- Exploring the cutting-edge technologies in mini-load AS/RS
- Shuttle-based systems: the agile workhorse of storage
- Carousel-based systems: rotating for rapid access
- Vertical lift modules (VLM): elevating storage efficiency
- Robotic cube storage: the grid of the future
- Vertical buffer modules: speed and scalability
- Autonomous mobile robots (AMR) and automated guided vehicles (AGV): the movers of modern warehousing
- Choosing the right AS/RS: key considerations for mini-load systems
- Storage density needs: maximizing your space
- Load types and sizes: tailoring the system to your inventory
- Throughput requirements: keeping up with demand
- Software reliability: the backbone of operations
- Scalability and flexibility: preparing for the future
- Cost considerations: balancing investment and return
- Adaptability and technical support: ensuring continuous operation
- Energy efficiency: reducing long-term costs
- Making th right choice for your warehouse
- Is AutoStore the best mini-load AS/RS?
- Typical frequencies of maintenance
- Conclusion
- The strategic advantage of mini-load AS/RS
1 Mini-Load AS/RS: Streamlining the Storage of Smaller Items
Mini-Load Automated Storage and Retrieval Systems (AS/RS) are specifically designed for handling smaller items such as totes, cartons, or trays. Capable of managing loads up to 1,000 pounds, these systems are ideal for environments that require high-speed picking and efficient storage of small items. Commonly found in settings like order picking, e-commerce fulfillment, and parts storage, Mini-Load AS/RS offers a combination of speed, accuracy, and space efficiency.
These systems are particularly effective in maximizing space utilization, especially in facilities where vertical space is leveraged. The compact design of Mini-Load AS/RS allows for the storage of many smaller items in a reduced footprint. This makes them a preferred choice for operations where the rapid retrieval and precise handling of items are critical to maintaining high throughput.
Several advanced technologies drive the efficiency of Mini-Load AS/RS. Shuttle-based systems, for instance, use autonomous shuttles that navigate along tracks within storage racks to retrieve and place items. These systems are highly adaptable, accommodating various load sizes and weights, which makes them suitable for high-density storage environments. Similarly, carousel-based systems, which can be either horizontal or vertical, rotate storage locations to a picking station, allowing quick and easy access to stored items. This technology is particularly beneficial in retail, parts storage, and healthcare, where swift access to inventory is essential.
Vertical Lift Modules (VLMs) offer another sophisticated solution by storing items in vertically arranged trays within a compact module. An automated inserter/extractor retrieves these trays as needed, making VLMs highly effective in space-constrained environments. Additionally, robotic cube storage systems, such as AutoStore, utilize a grid of bins stacked vertically and horizontally. Robots move across the grid to retrieve bins and deliver them to picking stations, maximizing storage density and adapting to various operational needs.
Despite their numerous advantages, Mini-Load AS/RS systems are not without limitations. One of the primary constraints is their load capacity, as they are designed for smaller and lighter items, unlike the larger, heavier loads managed by Unit-Load AS/RS systems. Furthermore, while Mini-Load systems are generally less complex than their Unit-Load counterparts, they still require significant investment in technology and infrastructure. The initial setup costs can be substantial, particularly for facilities requiring custom configurations or high levels of automation.
However, the benefits often outweigh these challenges. The automated nature of Mini-Load AS/RS ensures high accuracy in storage and retrieval, significantly reducing errors and enhancing overall inventory management. Real-time tracking and management of items become feasible, contributing to more efficient and streamlined operations.
Mini-Load AS/RS systems are ideally suited for environments where high volumes of small items need to be managed efficiently. They are particularly prevalent in e-commerce fulfillment centers, manufacturing facilities with numerous small parts, and distribution centers handling consumer goods or pharmaceuticals. In these settings, where speed, accuracy, and space optimization are paramount, Mini-Load AS/RS stands out as a critical component in achieving operational success.
In conclusion, while both Unit-Load and Mini-Load AS/RS systems serve the purpose of automating storage and retrieval processes, the Mini-Load AS/RS is distinctly tailored for handling smaller, lighter loads. Its ability to offer speed and precision in environments that demand these qualities makes it an invaluable tool in the modern landscape of warehousing and distribution.
2 Exploring the Cutting-Edge Technologies in Mini-Load AS/RS
Automated Storage and Retrieval Systems (AS/RS) have become essential in modern logistics and warehousing, especially when it comes to managing smaller, lighter items. Among the various technologies that power these systems, a few stand out for their innovation and efficiency. Let's dive into the key technologies that make Mini-Load AS/RS a game-changer in industries that require high-density storage and rapid item retrieval.
2.1 Shuttle-Based Systems: The Agile Workhorse of Storage
Shuttle-based systems are a cornerstone of Mini-Load AS/RS, known for their remarkable flexibility and speed. These systems employ small, autonomous shuttles that glide along tracks within storage racks, efficiently retrieving and placing items such as totes, bins, and cartons. The agility of these shuttles allows them to handle various load sizes and weights, making them ideal for high-density storage environments. Whether in a bustling e-commerce warehouse or a tightly packed manufacturing facility, shuttle-based systems offer the speed and precision needed to keep operations running smoothly.
2.2 Carousel-Based Systems: Rotating for Rapid Access
For environments that demand quick access to a diverse range of items, carousel-based systems provide an elegant solution. These systems, which can be configured horizontally or vertically, rotate storage locations to bring items directly to the operator. Horizontal carousels are particularly effective in high-speed picking environments, where small items need to be retrieved rapidly. Vertical carousels, on the other hand, maximize storage efficiency in facilities with limited floor space by utilizing vertical room. Common in retail, parts storage, and healthcare, carousel-based systems ensure that every item is within easy reach, minimizing downtime and boosting productivity.
2.3 Vertical Lift Modules (VLM): Elevating Storage Efficiency
Vertical Lift Modules (VLMs) are engineered to make the most of vertical storage space, a crucial advantage in compact environments. These systems consist of a series of trays stored within vertical columns, with an automated inserter/extractor mechanism that retrieves trays as needed. VLMs are particularly useful for storing small to medium-sized items in settings where space is at a premium. The ability to deliver items to an ergonomic access point not only improves retrieval efficiency but also enhances worker safety by reducing the need for bending or stretching. From spare parts storage to order picking, VLMs offer a sophisticated solution for maximizing space and efficiency.
2.4 Robotic Cube Storage: The Grid of the Future
In the realm of high-density storage, robotic cube storage systems, such as AutoStore, represent the cutting edge. These systems organize items in a grid of bins stacked both vertically and horizontally. Autonomous robots move across the top of the grid, retrieving bins and delivering them to picking stations. This innovative approach maximizes storage density and adapts easily to various operational needs. Particularly favored in e-commerce and retail fulfillment centers, robotic cube storage systems excel in environments where space is limited, and the need for rapid, accurate order fulfillment is high.
2.5 Vertical Buffer Modules: Speed and Scalability
Vertical Buffer Modules (VBMs) take storage efficiency to another level by using robotic shuttles that independently travel from level to level, retrieving stored items at high speeds. These modules are designed for scalability, making them suitable for operations that expect to grow over time. VBMs are especially useful in handling cases, totes, or trays in environments where rapid access to stored items is essential. Their modular design allows for easy expansion, ensuring that the storage system can evolve alongside the business.
2.6 Autonomous Mobile Robots (AMR) and Automated Guided Vehicles (AGV): The Movers of Modern Warehousing
While not traditional AS/RS systems themselves, Autonomous Mobile Robots (AMRs) and Automated Guided Vehicles (AGVs) play a crucial role in modern warehouses by complementing AS/RS operations. AMRs navigate autonomously within the warehouse, transporting goods between storage locations and picking stations with impressive flexibility. They are particularly valuable in dynamic environments where storage needs change frequently. AGVs, which follow fixed paths guided by wires, magnetic strips, or sensors, are more suited to predictable, repetitive tasks. Both AMRs and AGVs enhance the automation and efficiency of material handling, reducing reliance on manual labor and boosting overall throughput.
3 Choosing the Right AS/RS: Key Considerations for Mini-Load Systems
When selecting an Automated Storage and Retrieval System (AS/RS), especially a Mini-Load AS/RS, it's crucial to evaluate several factors to ensure the system aligns with your specific warehouse needs. Mini-Load systems, tailored for smaller, lighter loads, offer distinct advantages but also come with specific considerations that differ from Unit-Load or Micro-Load systems.
3.1 Storage Density Needs: Maximizing Your Space
One of the primary advantages of Mini-Load AS/RS is its ability to maximize storage density, particularly in environments where vertical space is abundant. These systems are designed to utilize both vertical and horizontal space efficiently, allowing for the storage of a large number of small items in a compact footprint. However, it's essential to assess your available warehouse space carefully. If your operation requires the storage of a high volume of smaller items, Mini-Load systems are ideal, but they may not be the best choice if your needs evolve to include larger, heavier items that demand a Unit-Load AS/RS.
3.2 Load Types and Sizes: Tailoring the System to Your Inventory
Mini-Load AS/RS is specifically designed for handling smaller, lighter items, such as totes, bins, and cartons. When choosing a system, it's critical to consider the dimensions and weights of the items you'll be storing. Mini-Load systems excel in managing a variety of small items efficiently, but if your inventory includes items that vary significantly in size or weight, you may need a more versatile solution. This focus on smaller load types is a strength of Mini-Load systems, but it also limits their applicability in environments that require the handling of larger or heavier goods.
3.3 Throughput Requirements: Keeping Up with Demand
In fast-paced environments, the speed at which items are retrieved and stored—known as throughput—is a critical factor in maintaining productivity. Mini-Load AS/RS systems are designed with high throughput in mind, ensuring quick retrieval and storage of small items. This makes them particularly beneficial in industries like e-commerce, where rapid order fulfillment is essential. However, it's important to match the system's capabilities with your operational demands. If your business experiences fluctuating demand or seasonal peaks, ensure that the Mini-Load system you choose can scale its throughput accordingly without compromising efficiency.
3.4 Software Reliability: The Backbone of Operations
The reliability of the warehouse management system (WMS) that controls your Mini-Load AS/RS is vital for smooth and uninterrupted operations. Given the precision required in handling smaller items, the software must be robust and capable of seamless integration with your existing systems. A user-friendly interface is also essential, as it reduces the learning curve for operators and minimizes the risk of errors. Ensuring that your WMS is not only reliable but also scalable and adaptable to future technological advancements is a critical consideration when implementing a Mini-Load AS/RS.
3.5 Scalability and Flexibility: Preparing for the Future
One of the standout advantages of Mini-Load AS/RS is its scalability. As your business grows or changes, your storage needs may evolve, and a flexible AS/RS can accommodate these shifts without significant additional investment. Mini-Load systems can be scaled up or down depending on demand, making them an excellent long-term investment. However, it’s important to assess how well the system integrates with your current warehouse processes. Smooth integration is key to minimizing disruptions and enhancing overall efficiency, particularly when scaling operations.
3.6 Cost Considerations: Balancing Investment and Return
While Mini-Load AS/RS systems are generally less expensive than their Unit-Load counterparts due to their smaller scale, the initial investment can still be substantial. It’s essential to analyze the total cost, including installation, maintenance, and operational expenses, and evaluate the expected return on investment (ROI). Understanding the long-term benefits, such as improved space utilization, reduced labor costs, and enhanced order accuracy, will help justify the upfront costs and ensure the system aligns with your financial goals.
3.7 Adaptability and Technical Support: Ensuring Continuous Operation
Flexibility is crucial for handling diverse products and adjusting to evolving business needs. A Mini-Load AS/RS should be adaptable to changes in inventory types or operational processes. Additionally, consider the availability of maintenance services and technical support. Continuous operation depends on the system's ability to function reliably with minimal downtime, and having access to prompt technical assistance can make all the difference in maintaining productivity.
3.8 Energy Efficiency: Reducing Long-Term Costs
Energy consumption is another important consideration, particularly as businesses strive to meet sustainability goals. An energy-efficient Mini-Load AS/RS can reduce long-term operational costs and support environmental initiatives. As you evaluate different systems, consider their energy requirements and how they align with your overall sustainability strategy.
4 Making the Right Choice for Your Warehouse
Choosing the right Mini-Load AS/RS involves a careful balance of several factors, from storage density and load types to software reliability and energy efficiency. By thoroughly evaluating these considerations and aligning them with your specific operational needs, you can select a system that not only enhances your warehouse efficiency but also positions your business for future growth. As industries continue to evolve, the adaptability, scalability, and precision of Mini-Load AS/RS will remain critical in maintaining a competitive edge in the marketplace.
4.1 Is AutoStore the Best Mini-Load AS/RS?
AutoStore has emerged as a strong contender in the automated storage and retrieval system (AS/RS) market, offering distinct advantages over traditional mini-load systems. While it may not be the best solution for every scenario, its unique features make it a compelling choice for many businesses. Here’s a closer look at what sets AutoStore apart, particularly in terms of cost, operational efficiency, and maintenance.
Cost Comparison and Operational Costs
One of the most striking advantages of AutoStore is its cost efficiency, both in terms of initial investment and ongoing operational expenses. Although AutoStore generally requires a significant upfront investment, this cost can be offset by the system’s space efficiency and operational savings over time.
Initial Investment:
AutoStore’s unique cube-based storage infrastructure and specialized robotic technology contribute to its higher initial costs. However, this investment is balanced by the system’s ability to maximize storage density, particularly by utilizing vertical space more effectively than traditional mini-load systems. This efficiency can lead to substantial savings on warehouse expansion or relocation, making the system more cost-effective in the long run.
Operational Costs:
AutoStore is designed to be energy-efficient, with robots that consume less electricity compared to the bulkier, crane-based systems of traditional AS/RS setups. This lower energy consumption translates into reduced operational costs. Additionally, the system’s modular design and use of standardized components contribute to lower maintenance costs and minimal downtime, further enhancing its cost-effectiveness.
Labor Costs:
AutoStore’s high level of automation significantly reduces the need for manual labor. Human intervention is primarily required at the item-picking stations, and even this process can be further automated with robotic arms. This reduction in labor dependency not only cuts costs but also allows businesses to allocate human resources to more strategic roles.
Long-Term ROI:
Despite the higher initial cost, AutoStore often delivers a strong return on investment (ROI) over time. The system’s increased storage density, improved order accuracy, and reduced labor and operational costs contribute to its overall value. For many businesses, these factors make AutoStore a financially sound choice over traditional mini-load AS/RS systems.
4.2 Typical Frequencies of Maintenance
Maintenance is a critical factor in evaluating any AS/RS system, and AutoStore performs well in this regard, offering both reliability and manageable upkeep.
Regular Maintenance:
AutoStore systems require regular maintenance to ensure optimal performance and longevity. Over time, as the system ages, maintenance needs may increase, but they remain within manageable limits. As a rough estimate, service costs typically range from 5% to 15% of the total capital expenditure (CAPEX) over a five-year period. This indicates that while regular maintenance is necessary, it is not overly burdensome.
Charging and Daily Maintenance:
AutoStore robots, such as the R5 and R5+ models, require at least four hours of charging daily, which is integrated into their typical working cycle of about 20 hours. This charging routine can be considered a form of regular maintenance, ensuring that the robots operate efficiently without interrupting the overall system performance.
System Uptime and Reliability:
AutoStore is known for its high reliability, with a reported uptime of 99.7%. This impressive figure suggests that while maintenance is necessary, it can often be performed without significant disruptions to the system. Additionally, AutoStore’s use of advanced control and data collection systems, such as logfiles, enables proactive maintenance based on real-time system performance data, reducing the likelihood of unexpected breakdowns.
Preventive Maintenance:
To further enhance system uptime and reduce lifetime maintenance costs, AutoStore recommends preventive maintenance programs. These programs are designed to stabilize the system’s performance over time, although specific frequencies for these activities can vary depending on factors such as system size, usage intensity, and environmental conditions.
Maintenance Complexity:
The complexity of maintaining AutoStore robots varies by model. For instance, the B1 robot has a simpler periodic maintenance process compared to the R5 and R5+ models, which could translate to lower maintenance complexity and costs over time.
4.3 Conclusion
AutoStore offers several key advantages over traditional mini-load AS/RS systems, particularly in terms of cost efficiency, operational savings, and maintenance. Its ability to maximize storage density, reduce labor costs, and maintain high reliability makes it an attractive option for many businesses. While it requires a significant initial investment, the long-term savings and ROI often justify the expense. However, as with any AS/RS system, it’s essential to evaluate your specific operational needs and long-term goals to determine the best solution for your business.
5 The Strategic Advantage of Mini-Load AS/RS
Mini-Load AS/RS systems are a specialized solution designed for environments that require the efficient storage and retrieval of smaller, lighter loads. These systems are particularly well-suited for operations like order picking, kitting, or buffer storage in warehouses and distribution centers. By leveraging technologies such as shuttle-based systems, carousel-based systems, VLMs, robotic cube storage, and VBMs, these systems offer unmatched speed, accuracy, and space efficiency.
However, it should be recognized that Mini-Load AS/RS systems do have some limitations. Their load capacity is inherently limited to smaller items, making them unsuitable for handling the larger, heavier loads managed by Unit-Load AS/RS systems. Additionally, while these systems are generally less complex than their larger counterparts, they still require a significant investment in technology and infrastructure. The complexity of the system can also increase maintenance needs and necessitate skilled personnel for operation and troubleshooting.
The Future of Efficient Storage
The technologies driving Mini-Load AS/RS systems represent the future of efficient, high-density storage. These systems are tailored for environments where speed, accuracy, and space optimization are paramount. Whether it's shuttle-based systems zipping through storage aisles or robotic cubes orchestrating a symphony of bins, the innovations in Mini-Load AS/RS are setting new standards in warehousing and logistics. As industries continue to evolve, the strategic adoption of these technologies will be key to maintaining a competitive edge in a fast-paced, increasingly automated world.