How standardized G2P workstation designs enable efficiency and flexibility
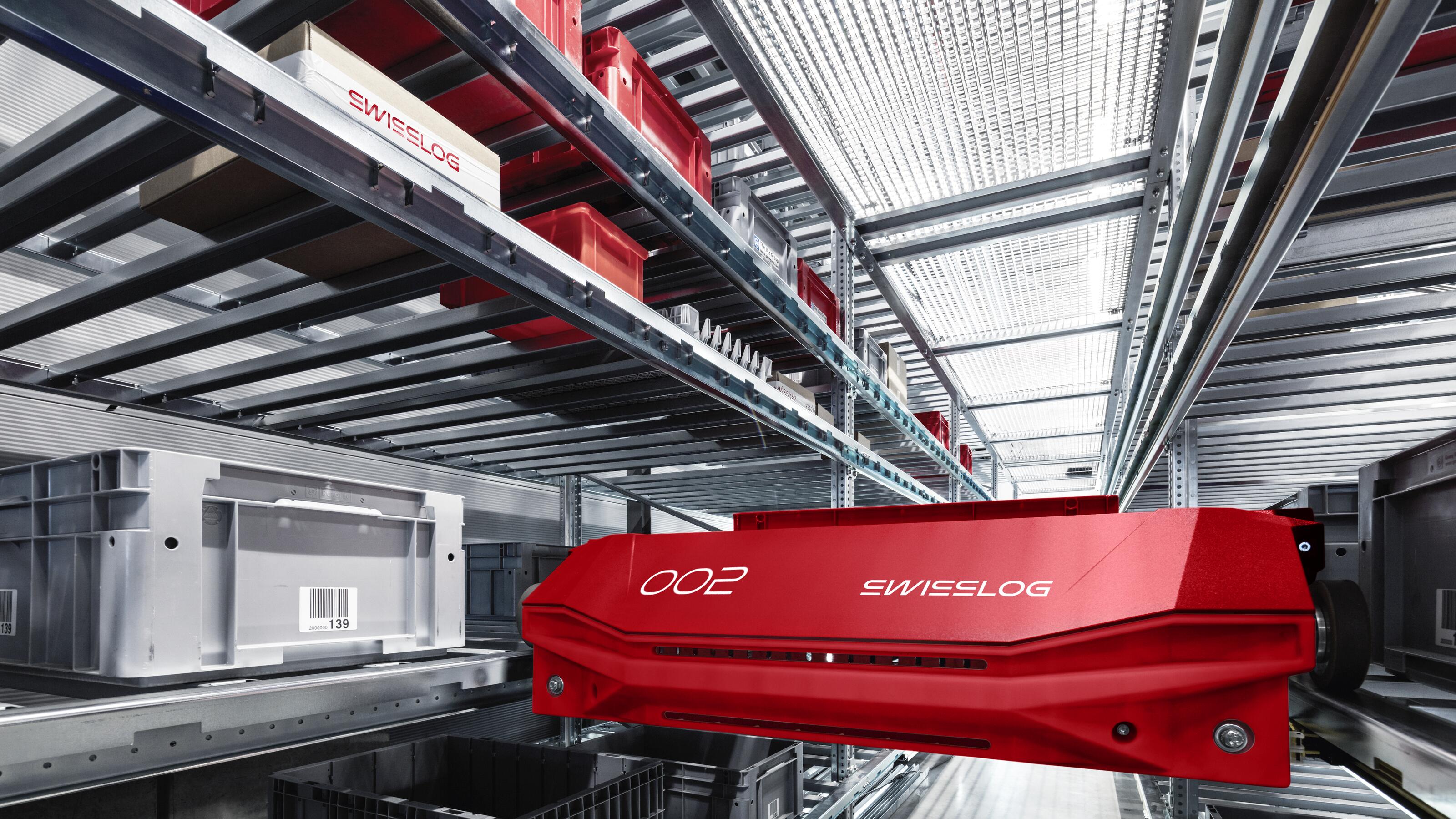
Key principles for G2P workstation design
Regardless of the specific function of a workstation, there are some basic principles that guide design. The first of these is minimizing operator movement within the station. The goods-to-person solution itself, of course, is designed to eliminate the need for operators to walk the warehouse floor to pick products, increasing picker productivity by a factor of three to five times.
But a poorly designed workstation can take back a percentage of these savings by forcing operators to move back and forth within the station as they pick products and place them in the appropriate order. A well-designed workstation will always minimize operator movement by providing easy access to bins presented by the picking engine and orders being filled.
The other principle that can’t be ignored is ergonomics. While G2P solutions address the fatigue that can result from walking across the warehouse all day, the picker in a G2P solution is repeating the same movements throughout the day and poor ergonomics can create unnecessary fatigue or discomfort. Poor positioning of source bins, for example, could force operators to bend too far to make every pick. Similarly, a display that is positioned too high can result in operators having to tilt their head back before each pick, increasing the potential for neck strain. Careful attention to the height and angle of each component within the station pays dividends throughout the life of the system in increased productivity and reduced discomfort.
Swisslog offers a family of standard G2P workstation designs that have been optimized for efficiency and ergonomics. Our Corporate Solution Center also has the capability to use advanced motion capture and 3D modelling to evaluate and optimize the design of non-standard workstations.
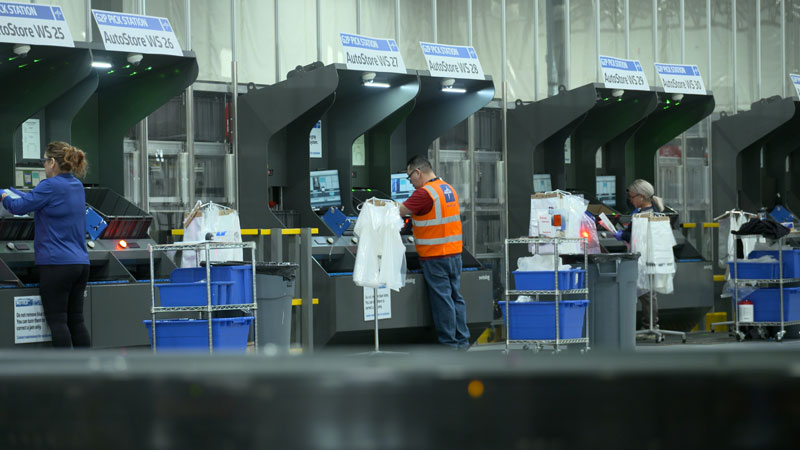
Matching G2P workstation design to channel requirements
Goods-to-person automation solutions are used across a wide range of industries to support fulfillment of everything from electronics to apparel to groceries. General merchandise retailers often support all of these categories and more in a single warehouse while also providing direct-to-consumer fulfillment and store replenishment from the same facility. In addition, each warehouse has different throughput goals and order profiles. All of these factors must be considered in the solution design.
At Swisslog, we have standardized workstation designs for the most common scenarios in omnichannel distribution that can then be optimized to the specific requirements of an operation. For example, our one-to-one workstation is designed for speed and efficiency and is typically used to support direct-to-consumer fulfillment in distribution centers with a high number of SKUs.
For warehouses with a lower number of SKUs or workstations supporting store replenishment, our one-to-N design, where N equals the number of open orders at the workstation, increases opportunities for operators to pick for multiple orders from the same bin. The base one-to-N workstation can also be expanded to two-to-N and N-to-N. I’ll explain how our SynQ software maximizes picker productivity in one-to-N and N-to-N workstations through dynamic order grouping in the next section.
In omnichannel warehouses, we can use several different workstation designs to enable efficient e-commerce fulfillment and store replenishment from the same automation system. With our CycloneCarrier shuttle system, which can handle cases as well as bins or totes, some aisles or storage levels can also be configured to support manual, semi-automated or automated mixed-case palletizing, with the shuttle providing precise sequencing of the cases to robots or humans. Shuttles are also an ideal solution for buffering of completed orders for release at a later time. As with palletizing, orders can be released sorted and sequenced.
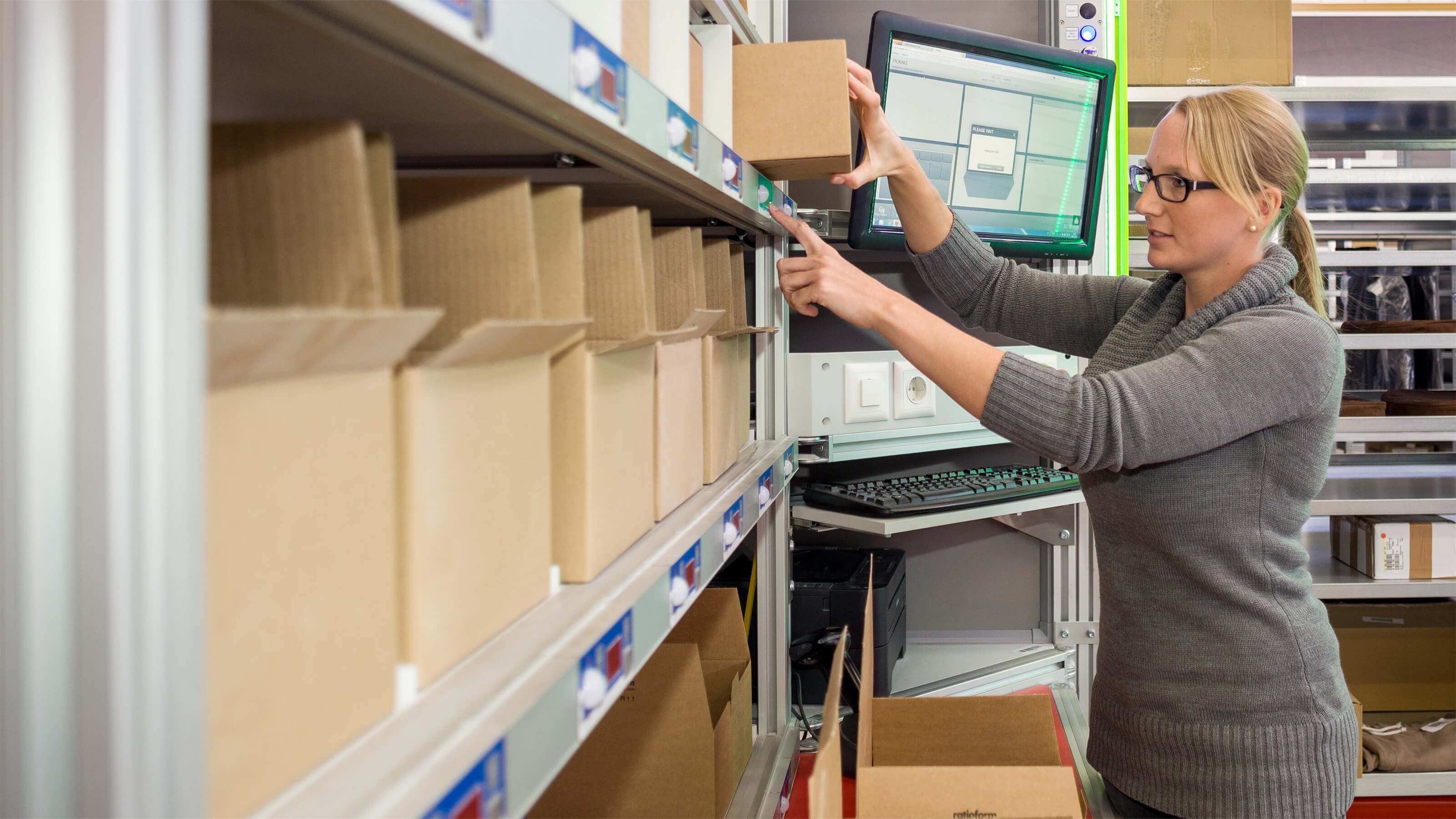
Enablers of G2P workstation station productivity
Swisslog SynQ software has multiple features that can enhance the productivity of pickers at G2P workstations in omnichannel warehouses. SynQ’s dynamic order grouping capability, for example, can measurably improve picker productivity in workstations that support picking to multiple orders by grouping orders based on common orderlines. This maximizes the operator “hit rate” or the number of orderlines that can be filled from the same source bin. The more you increase the hit rate above 1, the more efficient your fulfillment operation is. This feature is also available as a design tool that enables Swisslog engineers to estimate the improved hit rate based on customer order data, ensuring an optimized system configuration from the early stages of the project.SynQ has also been successfully integrated with Packsize packaging systems that produce on-demand cartons sized to order requirements. Through this integration, operators can pick directly to right-sized shipping cartons at the workstation, reducing packaging materials and freight costs.
Another enabler of productivity is the automation system’s user interface. It needs to provide operators with exactly the right information to pick quickly and accurately in an easily digestible form. Too much or too little information on the display can force operators to pause during the process, reducing efficiency. In many cases, displaying photos of the product to be picked can increase speed and accuracy. In one-to-N workstations, put-to-light technology can enhance speed and accuracy. With this technology, lights above or below the open orders on the put wall direct the operator to the right order as each product is picked.
Complete automation solutions for omnichannel distribution
Well-designed, ergonomic workstations are an important component of the complete automation solutions Swisslog provides to general merchandise retailers. Our portfolio of solutions allows omnichannel warehouses to support every stage of distribution from pallet storage and retrieval to case handling and goods-to-person picking to automated sorting, sealing and labeling. And our modular SynQ software controls the entire process through a single, unified platform.
Contact us to learn more.
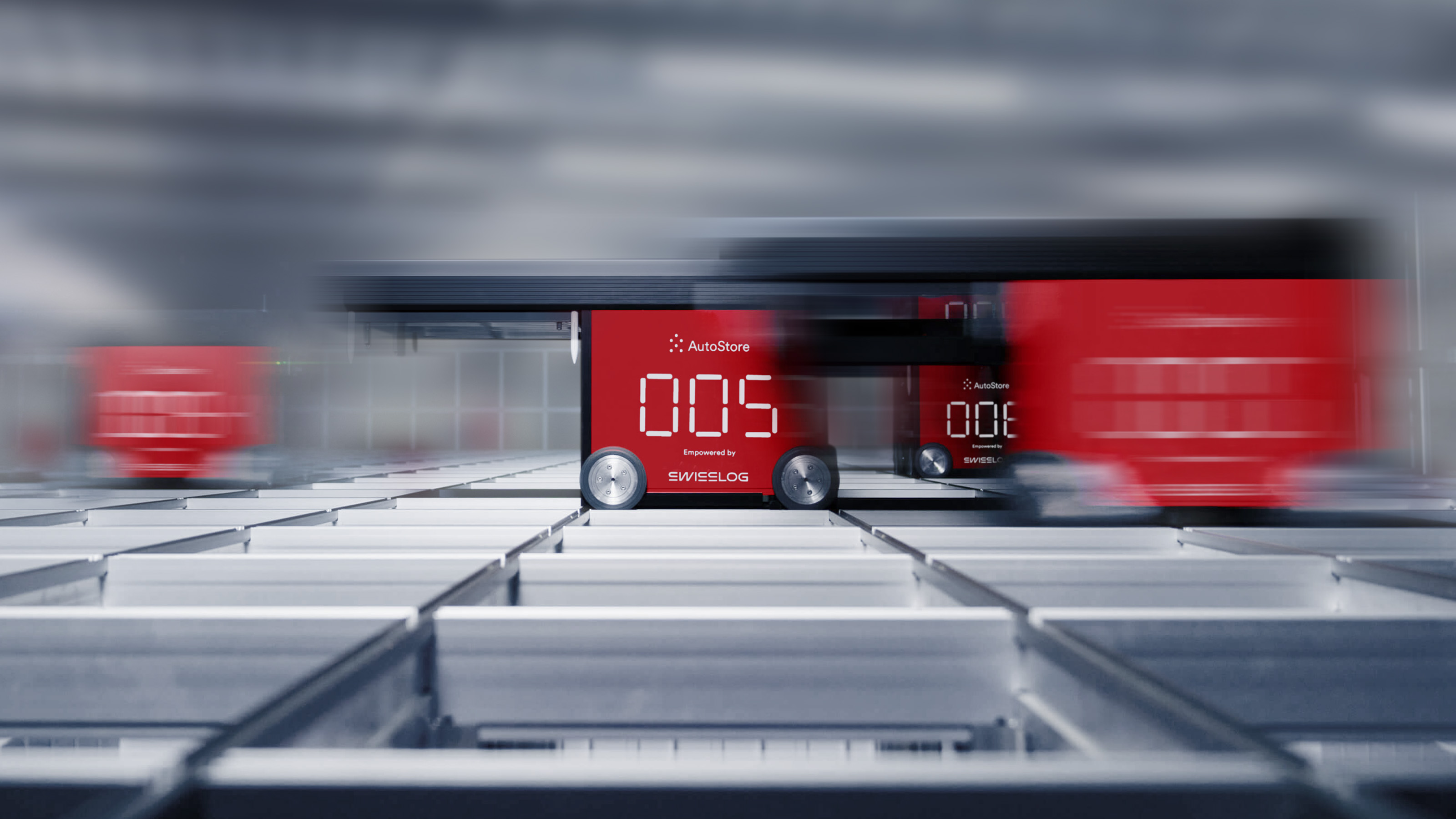
AutoStore offers superior density, throughput, and availability for warehouses. Powered by Swisslog’s SynQ software, it provides significant ROI where applicable, although it isn’t right for everyone.