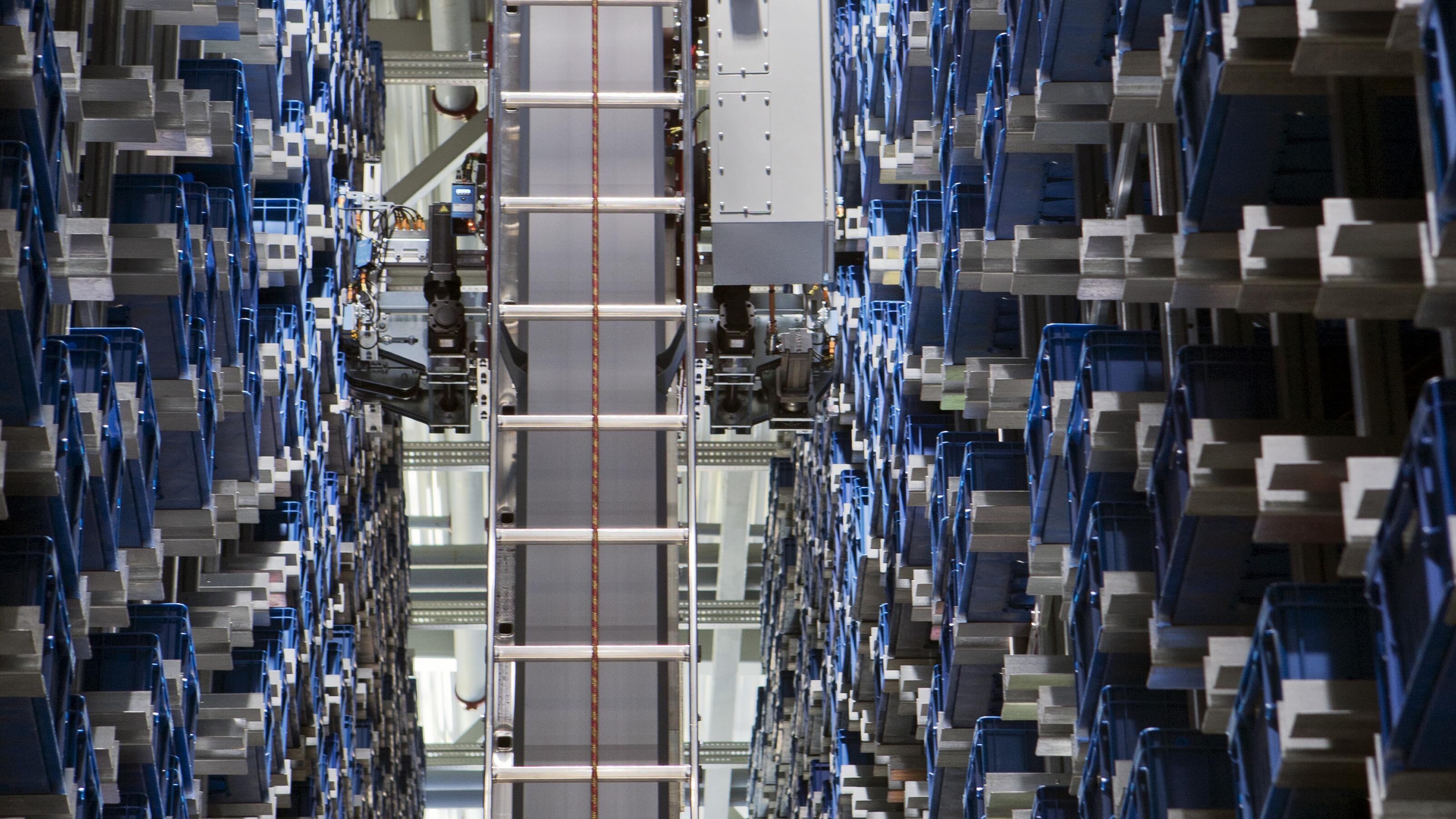
Differences and applications of Micro-load and Mini-load ASRS
Understand how miniload and micro load AS/RS systems differ. Advanced technologies in Micro-load AS/RS for small item storage. Advantages of Micro-load and key applications revealed.
- Key differences and applications of mini-load and micro-load AS/RS
- Advanced technologies in micro load AS/RS: optimizing small item storage
- Drawer systems: precision and density in small item storage
- Very small shuttles: agility and speed for lightweight items
- Carousels: optimizing micro item storage with vertical and horizontal rotation
- Integrating floor robots, AMRs, and AGVs into AS/RS systems
- Floor robots: versatility in material handling
- AMRs and AGVs: enhancing automation in AS/RS
- Advantages and disadvantages of micro load AS/RS technologies
- Industries thriving with micro-load AS/RS solutions
- Electronics manufacturing: precision and compact storage
- Medical supplies storage: safe and efficient management
- Small parts distribution: high-density and high-speed
- The strategic value of micro-load AS/RS
- Applications, products, and industries utilizing micro-load AS/RS systems
1 Key Differences and Applications of Mini-Load and Micro-Load AS/RS
Mini-load and micro-load Automated Storage and Retrieval Systems (AS/RS) are specialized technologies designed to optimize the storage and retrieval of goods in warehouses and distribution centers. While both systems aim to increase efficiency and storage density, they differ in their handling capacities, storage methods, and application environments.
Load Capacity is one of the primary distinctions between mini-load and micro-load AS/RS. Mini-load systems are designed to handle slightly heavier items, typically managing loads up to 75-100 pounds. These systems are commonly employed for storing totes, trays, and cartons, making them suitable for operations that involve medium-weight items. On the other hand, micro-load AS/RS are engineered for even lighter items, handling packages generally up to 100 pounds or less. This makes micro-load systems ideal for applications requiring the storage and handling of smaller, lighter goods.
Storage Methods also vary significantly between the two systems. Mini-load AS/RS typically use narrow aisles and storage rack structures to maximize space utilization. These systems often employ cranes to retrieve items from storage locations, enabling efficient handling of goods. In contrast, micro-load AS/RS utilize a storage rack structure that eliminates the need for building columns, allowing for a more flexible system layout. Micro-load systems generally use an extractor mechanism, which is designed to handle smaller items and work efficiently within the more compact storage structure.
2 Advanced Technologies in Micro Load AS/RS: Optimizing Small Item Storage
In the realm of Micro Load Automated Storage and Retrieval Systems (AS/RS), cutting-edge technologies have been developed to handle the specific demands of storing and retrieving small, lightweight items. These technologies not only maximize storage efficiency but also enhance the speed and accuracy of item retrieval, making them indispensable in industries that require the fast and precise handling of numerous small parts.
2.1 Drawer Systems: Precision and Density in Small Item Storage
One of the most effective technologies in Micro Load AS/RS is the drawer system. Designed for high-density storage, drawer systems utilize vertical space by stacking multiple drawers or trays within a compact footprint. This configuration allows for the storage of a large number of small items in a relatively small area, making it ideal for environments where space is at a premium.
The integration of automation technology is a key feature of drawer systems, enabling the automatic retrieval of specific drawers or trays. The system identifies the location of the required item and swiftly delivers the corresponding drawer to a pick station, whether for human operators or robots. This automated access significantly reduces the time required to locate and retrieve items, enhancing operational efficiency, particularly in high-throughput environments.
Another advantage of drawer systems is their flexible configuration. These systems can be tailored with various drawer sizes and depths to accommodate different types of small items, from tiny electronic components to tools or other products. This adaptability ensures that the storage solution can be customized to meet the specific needs of any operation.
In addition to efficiency, drawer systems offer robust inventory management capabilities. Integrated software tracks inventory levels, monitors item locations, and optimizes storage space, reducing errors and maintaining high accuracy in inventory control. Furthermore, the ergonomic design of drawer systems improves safety by minimizing the need for manual handling of items stored at heights or in hard-to-reach locations, thereby reducing the risk of injury.
2.2 Very Small Shuttles: Agility and Speed for Lightweight Items
Another innovative technology used in Micro Load AS/RS is the deployment of very small shuttles or robots specifically designed for lightweight items. These shuttles are engineered for agility and speed, efficiently navigating storage racks to retrieve and place small items with precision. Their compact size allows them to operate in densely packed storage environments, maximizing the use of available space while maintaining high throughput.
These small shuttles are particularly advantageous in industries where the rapid handling of numerous small parts is essential. By automating the retrieval process, these systems ensure that items are delivered quickly and accurately, minimizing delays and boosting overall productivity.
2.3 Carousels: Optimizing Micro Item Storage with Vertical and Horizontal Rotation
Carousels, both vertical and horizontal, are another technology commonly employed in Micro Load AS/RS. These systems rotate storage locations to bring items directly to the operator or automated picking station, ensuring quick access to stored items. Vertical carousels are particularly useful in environments with limited floor space, as they take advantage of vertical storage potential. Horizontal carousels, on the other hand, are ideal for applications where rapid, repeated access to small items is required.
The use of carousels in Micro Load AS/RS is prevalent in industries such as electronics manufacturing, medical supplies storage, and small parts distribution, where quick, reliable access to small, often high-value items is critical to maintaining operational efficiency.
2.4 Integrating Floor Robots, AMRs, and AGVs into AS/RS Systems
In addition to the core technologies of drawer systems, small shuttles, and carousels, other components such as Floor Robots, Autonomous Mobile Robots (AMRs), and Automated Guided Vehicles (AGVs) play a vital role in enhancing the functionality of both Mini-Load and Unit-Load AS/RS systems.
2.4.1 Floor Robots: Versatility in Material Handling
Floor robots are a versatile component that can be adapted for use in both Mini-Load and Unit-Load AS/RS systems. In Mini-Load environments, these robots are typically smaller and designed for lighter loads, focusing on the efficient movement of small items. They operate by retrieving and transporting portable storage shelving within the warehouse, making them ideal for slow to medium velocity inventory management. The scalability of floor robots allows for easy expansion with additional units, providing a flexible solution as storage needs grow.
2.4.2 AMRs and AGVs: Enhancing Automation in AS/RS
Autonomous Mobile Robots (AMRs) and Automated Guided Vehicles (AGVs) are integral to modern warehouse automation but are not standalone AS/RS systems. Instead, they complement AS/RS by facilitating material transport within the facility. AMRs navigate autonomously, moving items between storage locations and picking stations, which is particularly useful in dynamic environments where flexibility is key. AGVs, in contrast, follow fixed paths guided by wires, magnetic strips, or sensors, making them suitable for more predictable, repetitive tasks.
Both AMRs and AGVs are highly versatile and can be deployed in Mini-Load systems for handling smaller, lighter items or in Unit-Load systems for transporting larger, heavier loads such as pallets. Their integration into AS/RS systems enhances overall automation and efficiency, reducing reliance on manual labor and improving throughput across the warehouse.
3 Advantages and Disadvantages of Micro Load AS/RS Technologies
The technologies employed in Micro Load AS/RS each bring specific advantages that make them suitable for particular applications. Drawer systems, with their space efficiency and ergonomic design, are ideal for industries that require the precise storage and quick retrieval of small items. Small shuttles excel in environments where speed and agility are paramount, while carousels offer optimized storage solutions in both vertical and horizontal orientations.
However, these systems also come with certain limitations. The initial investment in these technologies can be significant, especially when custom configurations or high levels of automation are required. Additionally, the complexity of these systems necessitates skilled personnel for operation and maintenance, which can increase operational costs.
Despite these challenges, the benefits of Micro Load AS/RS technologies—such as enhanced space utilization, improved speed and accuracy, and better inventory control—often outweigh the disadvantages, particularly in high-throughput industries where efficiency is critical.
4 Industries Thriving with Micro-Load AS/RS Solutions
Micro-Load AS/RS systems are specialized for managing extremely small and lightweight items with high precision. These systems excel in environments where the meticulous handling of tiny parts or products is essential, often involving automated drawer systems, very small shuttles, or robotic mechanisms designed for micro-scale operations.
4.1 Electronics Manufacturing: Precision and Compact Storage
In electronics manufacturing, the handling of small components like microchips, circuit boards, and other tiny parts is crucial. Micro-Load AS/RS systems provide a perfect solution by offering high-density storage in a compact footprint. These systems ensure that even the smallest items are stored securely and can be retrieved with precision, reducing the risk of damage and improving the efficiency of the production process. By automating the storage and retrieval of delicate components, Micro-Load AS/RS systems help manufacturers maintain the quality and integrity of their products while streamlining assembly processes.
4.2 Medical Supplies Storage: Safe and Efficient Management
The medical sector benefits greatly from Micro-Load AS/RS systems, especially in the storage and management of small, high-value items like surgical instruments, pharmaceuticals, and medical devices. These systems offer the precision required to handle sensitive items while minimizing human contact, which is crucial for maintaining sterility and safety. In medical facilities where space is often limited, Micro-Load AS/RS maximizes storage capacity and ensures that critical items are easily accessible when needed, supporting both routine operations and emergency responses.
4.3 Small Parts Distribution: High-Density and High-Speed
Industries that involve the distribution of small parts, such as automotive or aerospace manufacturing, also find significant advantages in using Micro-Load AS/RS systems. These systems are designed to handle a large volume of tiny, lightweight items, ensuring they are stored efficiently and retrieved quickly to meet just-in-time manufacturing requirements. The speed and accuracy of Micro-Load AS/RS systems are particularly valuable in environments where rapid order fulfillment and minimal downtime are critical to maintaining production schedules.
5 The Strategic Value of Micro-Load AS/RS
Micro-Load AS/RS systems are tailored for industries where the handling of small, lightweight items with high precision is essential. While the overall concept of AS/RS applies broadly across various industries, Micro-Load AS/RS is specifically suited for environments that demand compact storage solutions, precise inventory management, and the ability to manage high volumes of small items. This makes Micro-Load AS/RS particularly valuable in electronics manufacturing, medical supplies storage, and small parts distribution, where space efficiency and accuracy are paramount.
6 Applications, Products, and Industries Utilizing Micro-Load AS/RS Systems
Micro-load Automated Storage and Retrieval Systems (AS/RS) are integral in various industries that require efficient storage and rapid retrieval of small items. These systems are particularly valuable in environments where high-density storage, efficient use of space, and quick access to a large number of small stock-keeping units (SKUs) are critical.
Applications of micro-load AS/RS are diverse, with one of the most common being order fulfillment. In goods-to-person order picking systems, micro-load AS/RS quickly retrieve and deliver small items to pickers, significantly speeding up the fulfillment process. Additionally, these systems are highly effective in managing buffer storage, offering a more efficient alternative to long conveyor systems by optimizing warehouse space. Micro-load AS/RS also excel in storing slow-moving items, helping to reduce handling costs and the need for extensive warehouse space. They are particularly useful in sequencing and buffering items in compact warehouse environments, enhancing operational efficiency.
Products typically handled by micro-load AS/RS include a wide range of small parts and components, such as electronic components, pharmaceuticals, small consumer goods, automotive parts, office supplies, and cosmetics. These systems are designed to manage small and often delicate items, ensuring they are stored and retrieved with precision.
Industries that commonly use micro-load AS/RS include e-commerce, where rapid order fulfillment of small items is essential, and electronics manufacturing, which requires the storage and retrieval of small electronic components. The pharmaceutical industry benefits from these systems for managing small drug packages and medical supplies, while the automotive industry uses them for handling and storing small automotive parts. In the retail sector, micro-load AS/RS are ideal for managing diverse SKUs of small consumer products, and in the aerospace industry, they are used for storing small, high-value parts.
Key Features of micro-load AS/RS include their ability to handle packages typically weighing 100 pounds or less. These systems are often integrated with other AS/RS systems to buffer and stage items and can be designed to store a variety of handling methods, including trays, sheets, and totes. Micro-load AS/RS provide high-density storage within a compact footprint, making them particularly advantageous in space-constrained environments.
Overall, micro-load AS/RS systems are crucial in industries and applications that demand efficient and accurate storage solutions for small items, ensuring rapid retrieval and optimized use of vertical space.