Economic changes strengthen the business case for warehouse automation in Canada
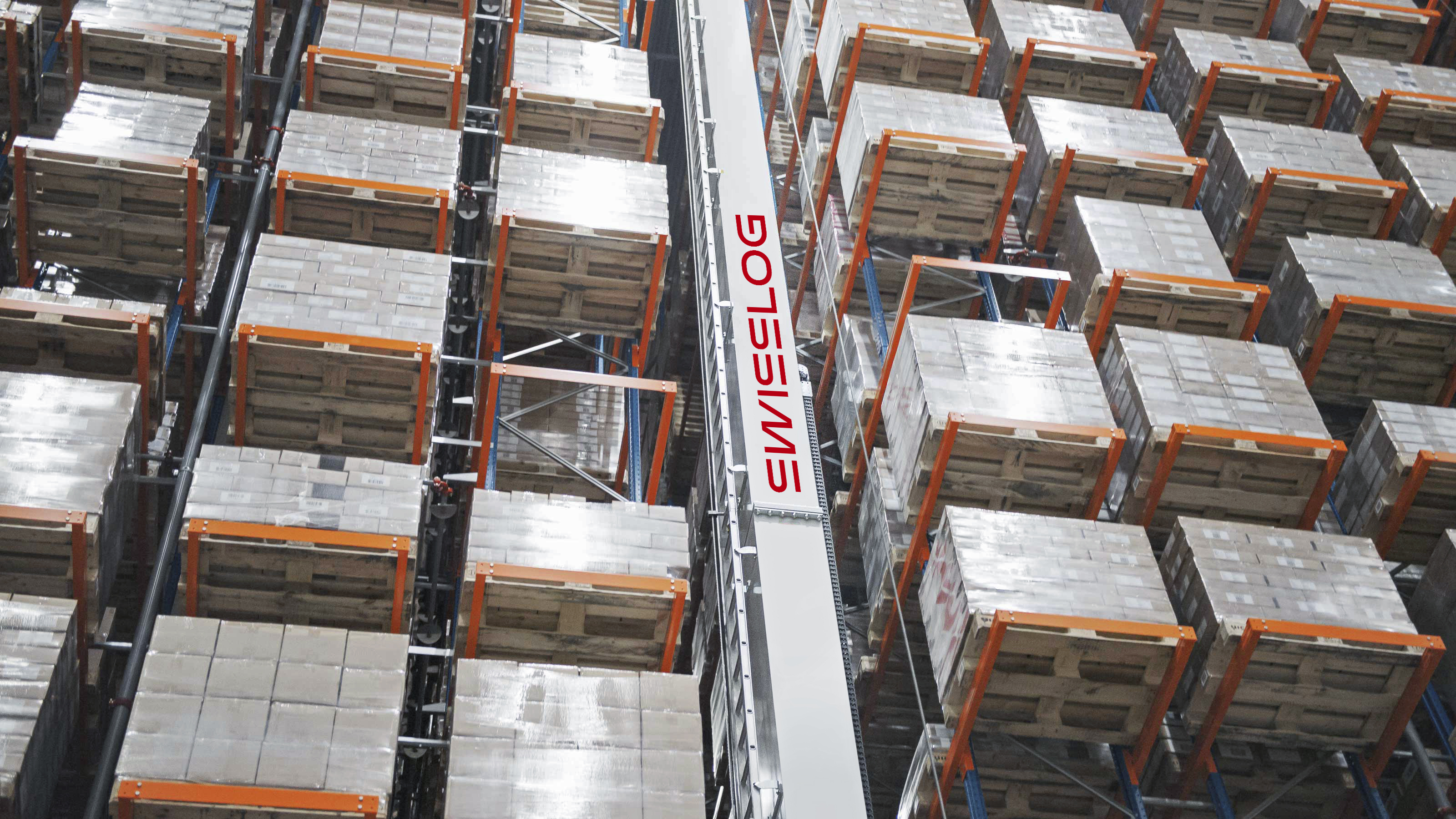
Automation solutions for the Canadian market
Automation solutions capable of increasing storage density offer relief from the pressures being placed on Canadian warehouse operators by rising lease rates and real estate costs. For example, pallet ASRS systems, like Swisslog’s market-leading Vectura cranes can significantly improve warehouse storage density and space utilization through their ability to handle multi-deep pallet storage layouts and operate at heights up to 50 meters. Our PowerStore pallet shuttle is ideal for pallet warehouses that require high throughput and high density, particularly where-ceiling heights are lower. And, both systems deliver excellent reliability and performance in ambient, chilled and frozen environments.
Automation can also offset higher labor costs by supporting huge productivity gains in processes such as each picking and palletizing. Swisslog offers a range of goods-to-person picking solutions that are proven to increase pick rates by 3-5 times. Our CarryPick mobile robotics solution, for example, offers a flexible and easy-to-implement goods-to-person solution while our versatile CycloneCarrier light-goods shuttle is ideal for high-volume e-commerce applications, omnichannel warehouses that need to store cartons and eaches in the same system, and as the engine for robotic palletizing.
We’re also one of the world’s leading integrators of the ultra-dense AutoStore goods-to-person system, with more than 400 deployments under our belt. In addition to our unmatched experience configuring and deploying AutoStore-based solutions, our AutoStore control software includes unique features that unlock productivity and throughput levels not available through other AutoStore control systems.
You can review some of our many customer references here.
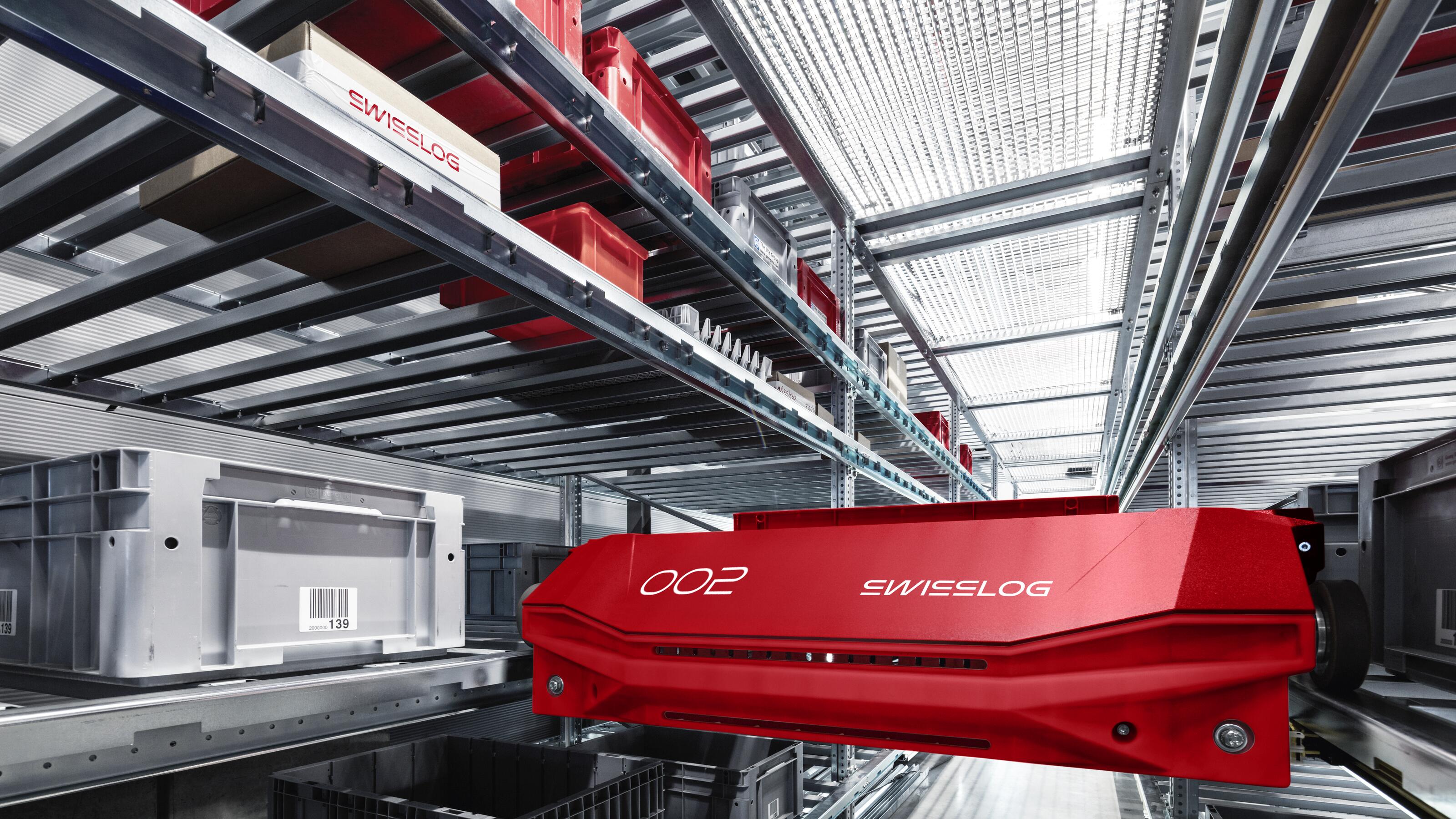
Software sets Swisslog solutions apart
Selecting the right technology is critical to the success of any automation project and we take a technology-agnostic approach to solution design that is driven by order data, site considerations and business goals. But the software that controls your automation is just as important as the hardware.
Our modular SynQ platform combines automation control, warehouse execution and warehouse management functionality in a fully integrated and globally supported platform. SynQ integrates easily with ERP, WMS and other software to ensure interoperability with your existing systems and its modular design allows our customers to deploy a single module to control one automation system or several modules to provide centralized control of fully multiple automation systems as well as manual processes. Because its fully integrated, SynQ provides single point of control across processes and systems to standardize the user experience, speed recovery from errors, and enable centralized visibility through 3D visualizations.
SynQ is also a mature and secure platform that has consistently been enhanced based on the needs of SynQ users. That continuous focus on user requirements enables the standard configuration of SynQ to meet the needs of most applications with little or no customization.
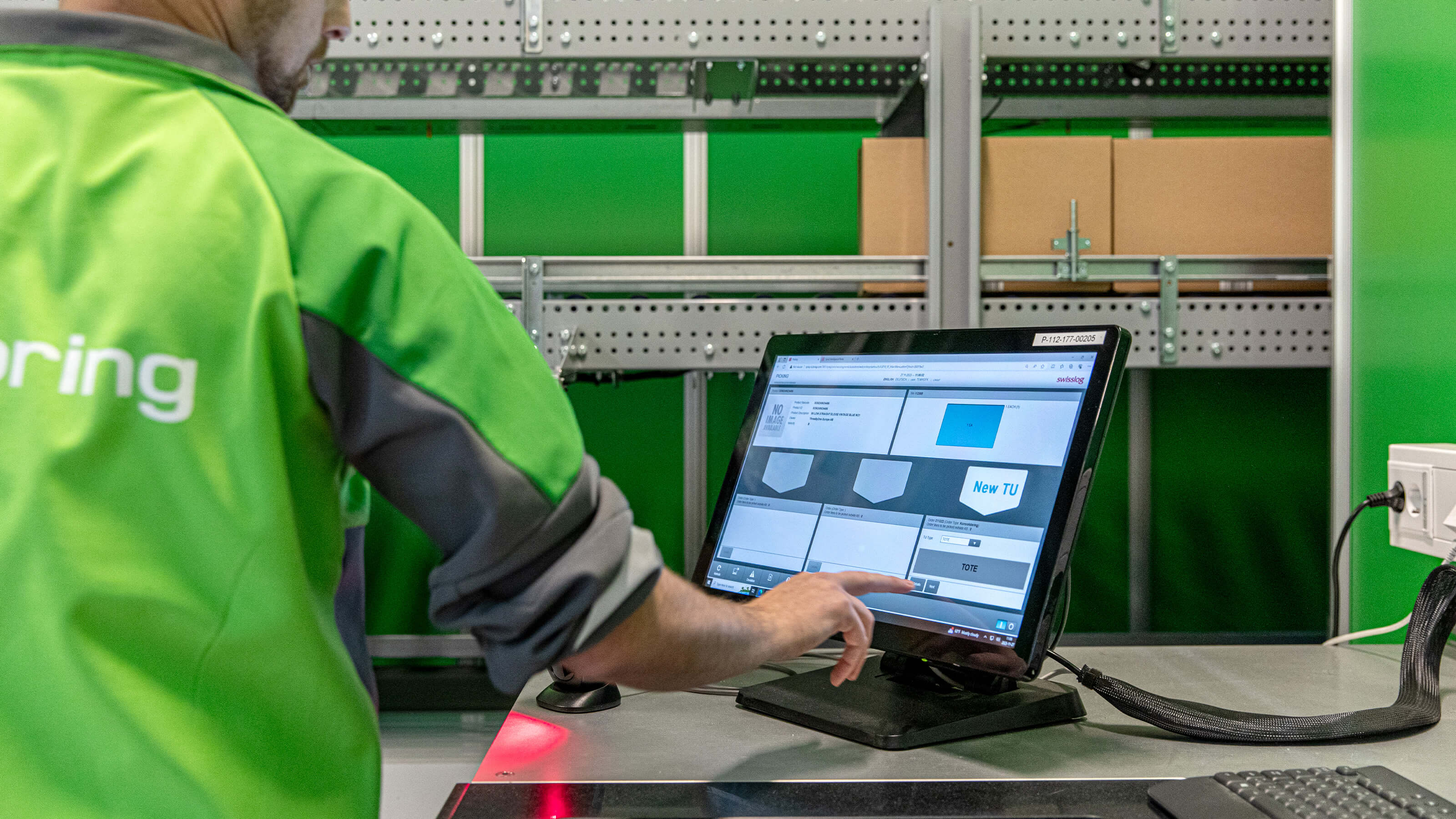
Local automation support for the Canadian market
Across Canada, we are seeing warehouse operators in just about every industry turn to automation to enhance utilization of increasingly valuable warehouse space, create protection from labor shortages, and drive down operating costs. That is already starting to put operators who rely on manual processes at a competitive disadvantage.
As a result, the business case for warehouse automation in Canada has never been stronger and Swisslog is expanding our in-country sales and service support to ensure Canadian warehouse operators have access to the best automation solutions with the local support they expect.
If you have a project you’d like to talk about, contact us.

AutoStore’s latest State of Warehouse Management and Fulfillment report, based on insights from 300+ global supply chain leaders, highlights 2025 warehouse priorities & benchmarks automation adoption.