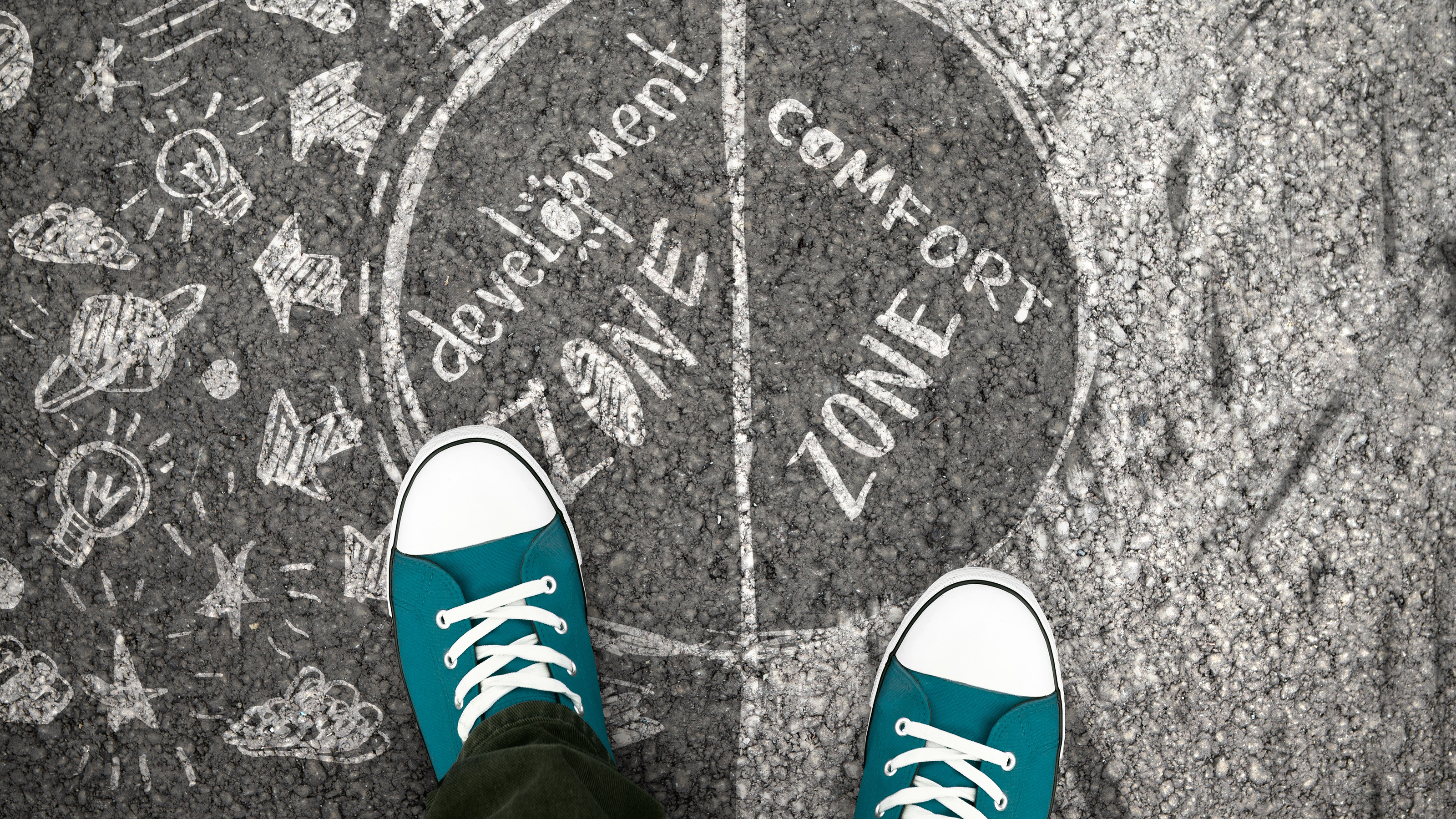
Getting Comfortable with Uncertainty
October 27, 2020
How to Prevent Dynamic Market Conditions from Paralyzing Automation Initiatives
Do you know what the demand on your warehouse will be tomorrow? How about in five years? Chances are you have a pretty good idea what to expect tomorrow but are a lot less certain what demand will be in five years.
Will the pandemic accelerate the shift to e-commerce as is being projected and if so, will we eventually see a plateau? Will new retail strategies be effective at attracting consumers back to brick-and-mortar stores? It’s essential to develop long-term business plans based on projections of what the future will bring, but if this year has taught us anything it is that it is almost impossible to know what to expect in the next twelve months let alone the next five years. The farther out we try to see, the greater the uncertainty.
Project management and software development methodologies refer to this as the “cone of uncertainty.” It's the reason organizations embarking on projects they haven’t previously undertaken have such a hard time committing to a firm schedule. The cone of uncertainty is so large at the beginning of the project they can’t develop detailed project plans because so much is unknown. As research and development proceeds and the project moves closer to completion the cone of uncertainty narrows and timelines become more accurate.
The challenge organizations face when planning material handling automation that will carry their business into the future is that the cone of uncertainty never really narrows. It’s tempting to think the market is extremely volatile today and if we wait a year, we’ll have more clarity into future requirements. But a year later it’s just as difficult to project where the business will be in five years and the decision gets delayed again. Meanwhile, some companies are moving forward with automation initiatives that will drive competitive advantage over organizations that fail to take action.
Some of this hesitancy may be due to previous experience with legacy automation systems that were incapable of adapting to new sales channels, expanding inventories and changing market requirements and so were functionally obsolete early in their expected lifespan. But material handling automation has evolved away from inflexible, bolted down systems to data-driven and robotic systems that have the flexibility to adapt to change quickly and efficiently.
For example, when the pandemic hit, Swiss e-commerce fulfillment specialist Competec saw a sudden and dramatic spike in its throughput and inventory requirements. Within two weeks from order placement they were able to add additional robots to their AutoStore system, originally implemented by Swisslog in 2012, to handle the higher order volumes. Over the next three months they maintained high throughputs while expanding the AutoStore grid and adding workstations to enable support for next-day delivery and manage continued growth.
Another example is the work we are doing for a large multi-channel retailer. Their shuttle system was designed for store replenishment but was being underutilized when the pandemic forced the closure of retail stores. They were able to quickly pivot to use the system to replenish their e-commerce warehouses and are now planning to add workstations to the system to enable it to support e-commerce overflow as e-commerce sales grow faster than expected.
It simply isn’t practical to design automation based on the needs of the business in five years. But it is practical with the current generation of material handling automation to plan the system based on the needs of today and adapt as needs change.
More than ever, automation needs to be a strategic priority and the price of delay has never been higher. At Swisslog, we can design and implement material handling automation that meets your requirements today while scaling or pivoting to future requirements as they emerge.