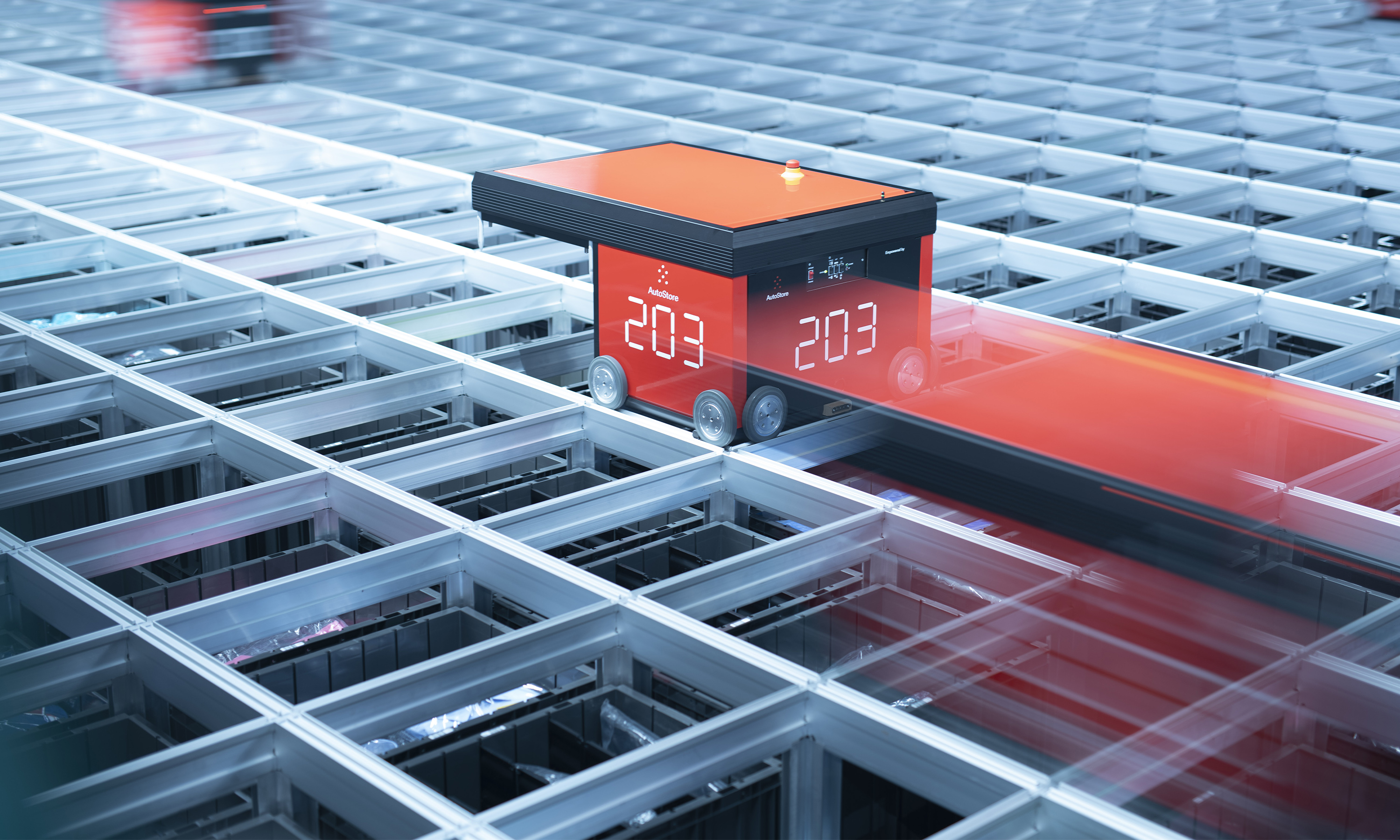
Logistics service provider selects Swisslog’s AutoStore
September 17, 2018
Swisslog will implement an AutoStore system at Versteijnen Logistics in Tilburg, The Netherlands. With the compact, automated storage and order picking system, the logistics service provider will take a new efficiency step in its cross-border fulfilment activities.
On its 12 acre European distribution campus in Tilburg, Versteijnen Logistics takes care of the logistics activities for a variety of customers, including workwear manufacturer Tricorp. “A rapidly growing customer, for whom we are doing more and more. Without changing the cut-off times”, says Managing Director Jorn Versteijnen.
The extra hands needed to carry out the growing amount of work on time are becoming increasingly difficult to find. Especially at the logistics hotspot from which Versteijnen Logistics operates. “That is why we started looking for a solution to execute this part of our activities faster and more efficiently”, continues Versteijnen. That solution was found at Swisslog, who will implement an AutoStore system in Tilburg for the storage and picking of - initially - 6,000 sku’s.
Goods-to-person
Versteijnen: “There were hardly any serious alternatives. We knowingly wanted a goods-to-person system and not for example a pick-to-light solution.” The AutoStore concept fits in seamlessly with the wishes of the service provider and the product range of its customer. Tricorp is Versteijnens first customer to use AutoStore to store and pick stocks. “However, we have more customers with a large assortment and relatively little stock, for example in the spare parts sector. This is also a perfect system for those customers. I am convinced that more customers will follow soon”, says Versteijnen. “In addition, the system offers us distinctiveness. AutoStore is incredibly compact and can easily be placed in our existing pallet warehouse. This will enable us to handle both pallet and parcel deliveries for the whole of Europe from the same stock location.”
Flexible, productive and efficient
Initially, the AutoStore system, which will be operational in January 2019, counts 20,000 bins, 18 robots and 8 workstations, 6 of which are for outbound and 2 for inbound. “However, the system is extremely flexible. When necessary, we can also use all stations for outbound”, explains Versteijnen.
Moreover, the modular concept is very easy to expand. By using more robots, the handling capacity increases. The orderpicking capacity can be increased by adding more workstations or by using a different picking methodology. And a growing need for storage capacity can easily be realised - without downtime - by expanding the storage grid. “In this way, high productivity, high efficiency and optimal service to our customers will continue to be guaranteed in the future”, concludes Versteijnen.