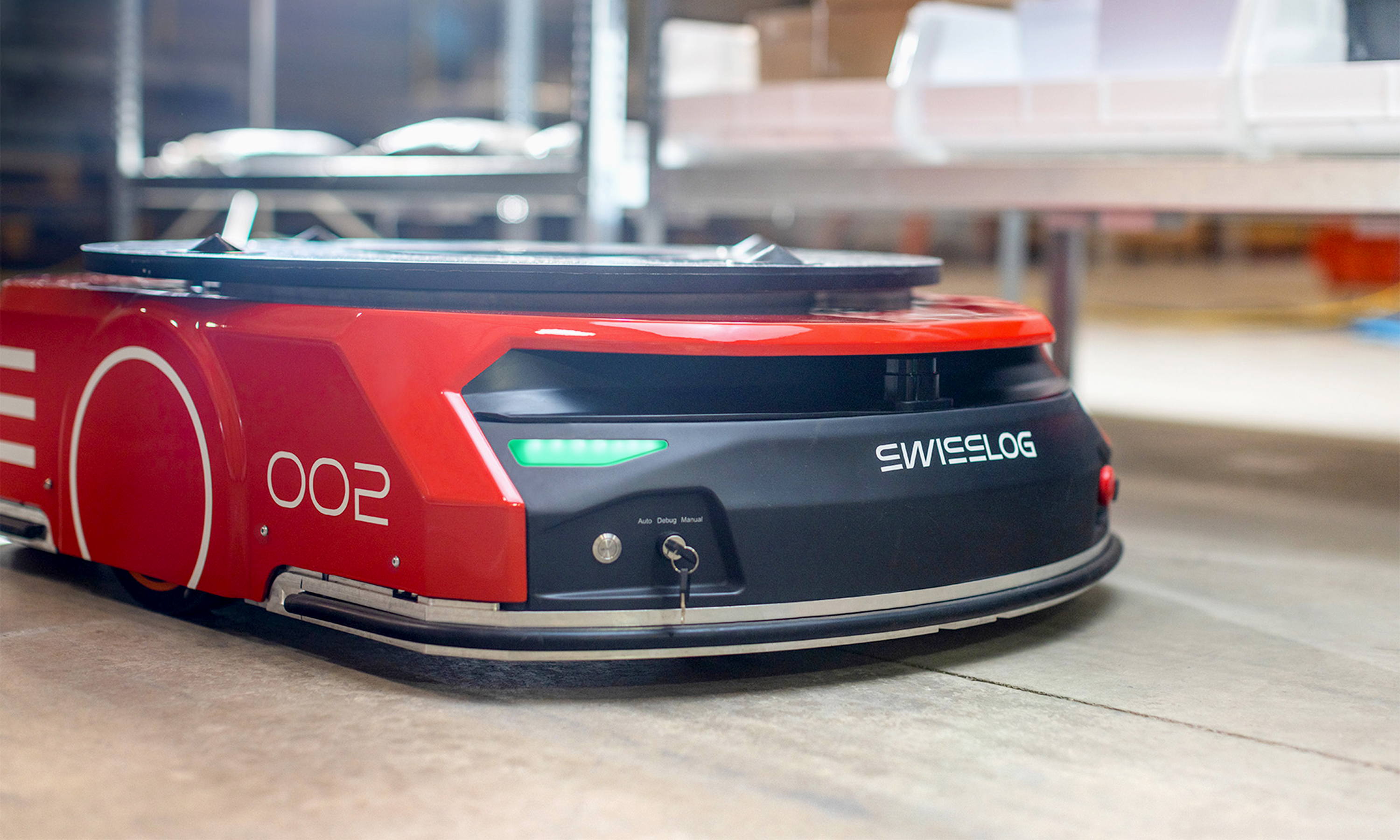
Four Robotic Systems Changing the Face of Warehouse Automation
25 September 2018
A new generation of modular, intelligent robots is quietly infiltrating warehouses around the world, delivering greater productivity and throughputs while enabling unprecedented flexibility. This post reviews four of the leading use cases for today’s warehouse robots.
What’s next for your warehouse? Increased connectivity to enable IoT? Migrating warehouse software to the cloud? Or maybe doing more with data?
Those are just some of the initiatives that seem to dominate the discussion of next-generation warehouse technology. Meanwhile, an equally powerful technology may be overlooked because it’s been around for decades: robotics.
Robots have been used in manufacturing for years, but they are relatively new to the warehouse. And the robots that are increasingly populating today’s warehouses are significantly different from the fixed, hulking robot arms found in manufacturing.
They represent a new generation of mobile, intelligent robots that are leveraging advances in vision, gripping and navigation technology to enable a better approach to warehouse automation. It’s an approach that delivers the productivity and throughput improvements of fixed conveyor systems while delivering the flexibility and scalability only modular and mobile systems can provide.
These robotic-automation solutions integrate a range of technological advances to bring down costs, enable new applications and improve performance. While more robots are coming to the warehouse, here are four systems that are already there:
-
CarryPick Autonomous Mobile Robots
Goods-to-person picking systems dramatically reduce pick times and improve the ability to adapt to fluctuations in demand. CarryPick is an efficient and scalable goods-to-person system that uses autonomous mobile robots to deliver products to ergonomic workstations where they can be assembled into orders. The scalable fleet of robots is controlled and monitored by the warehouse management system and works collaboratively to ensure a continuous flow of goods to the workstations.This is the solution chosen by Von Maur, a growing multi-channel U.S. retailer, to automate fulfillment within its warehouse while accommodating future growth. The modular design permits starting small and growing as needs change. It can easily integrate into existing structures, requires minimal modifications to enable autonomous navigation, and can even be set up in a small facility without a 30 to 40-foot ceiling height. As the operation grows, more robots and workstations can be added as needed and the entire system can be re-located to a larger facility if that becomes necessary.
-
AutoStore Automated Storage and Retrieval
The compact and flexible AutoStore system supports goods-to-person picking and is designed to handle high volumes of both fast- and slow-moving small-order and small-case-pick SKUs for fulfillment operations that require high storage density.
Hat World, which operates under the retail brand Lids, is using AutoStore to support fulfillment of its broad inventory through multiple channels. The organization has experienced a 20-time improvement in e-commerce pick rates and optimized storage capacity. The three-dimensional AutoStore grid, in which bins are stacked on top of each other, creates up to 60 percent better space utilization than other automatic storage systems and 300 percent better than conventional rack systems. Machine learning allows the AutoStore robots to identify fast-moving items and keep them at the top of the grid for faster access. -
ItemPiQ Automated Item Picking
Automated picking has been enabled by major strides in robotic vision and gripping technology as well as machine learning. Swisslog’s ItemPiQ is a robotic-based solution for picking single items from source bins and placing them into order bins. It features state-of-the-art sensor technology, a 7-axis arm, a multifunctional gripper, and an intelligent vision system. A single ItemPiQ robot can pick at a rate of 350 to 600 items per hour, depending on item characteristics. Advances continue to be made in this technology and a second generation of ItemPiQ is expected to be demonstrated in the near future. -
ACPaQ Automated Case Picking
The Swisslog ACPaQ robot provides a similar function as ItemPiQ for mixed case palletizing. It automates the process of creating customized mix pallets for individual stores from single-SKU pallets. ACPaQ is a fast, reliable and flexible solution that can deliver throughput of up to 1,000 units per hour – two to three times more than traditional solutions. It’s gentle gripping technology can safely handle a wide range of case types and palletizing software allows customization of the order to improve the efficiency of in-store replenishment and ensure the stability of mixed-case pallets.