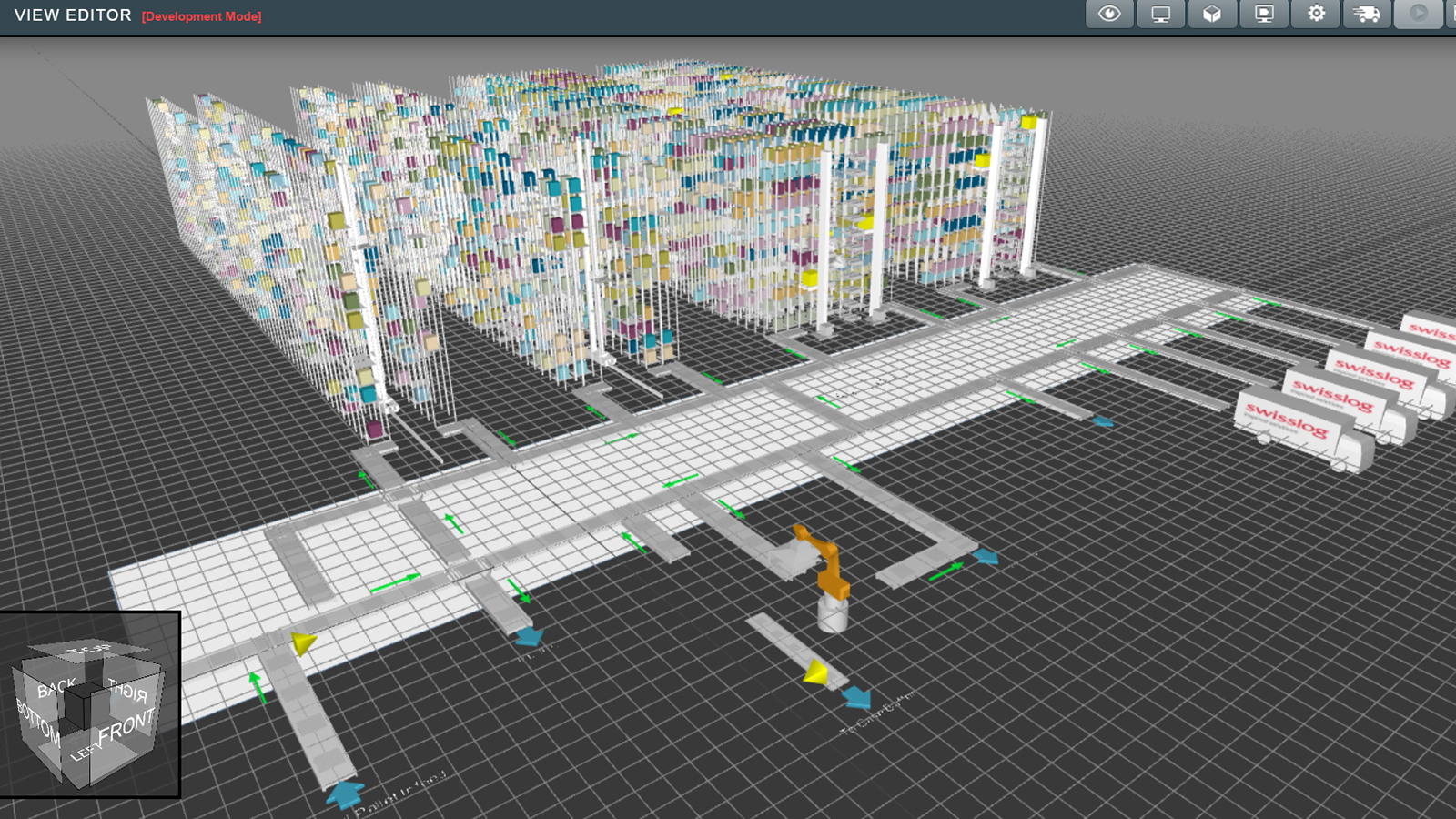
Using Real-Time Data to Improve Warehouse Operations
26 September 2017
Collecting, analyzing and visualizing real-time data is key to achieving the promise of Industry 4.0. Condition monitoring is delivering on that promise today. Find out how.
In my last Industry 4.0 blog post, I previewed some of the exciting developments that are occurring in the area of virtual and augmented reality as they relate to warehouse management. Powered by the 3D visualization capabilities in WMS platforms, virtual technologies allow a digital copy of the warehouse to be used to monitor material flows in real-time, enable remote service, and streamline the design and implementation of new facilities and equipment.
For this post, I want to dig deeper into one of the enabling technologies behind virtualization—and one of the core principles of Industry 4.0—real-time data.
It’s nice to have a digital copy of the warehouse, but if that copy is static it is of limited value. What makes virtualization such a promising technology is the ability to integrate real-time data from warehouse operations with 3D models to create a virtual view of conditions at any location in the warehouse at any time.
Digital devices, such as RFID, sensors, and scanners are now on everything from individual products and cartons to material handling equipment, forklifts, and robots. These IoT-enabled devices, as well as intelligent machines, generate the data required to transform static virtual models into real-time, 3D windows into what is happening at any location in the warehouse at any time.
Still, I know many warehouse operators read about virtualization and think, “that sounds great and I’m sure we’ll get there one day, but we are a long way from that today. We are so busy managing day-to-day challenges, we don’t even have time to think about virtualization.”
The thing to remember is that real-time data is not an all-or-nothing proposition. Just because you aren’t creating a holistic, real-time view of the warehouse, doesn’t mean the real-time data your systems are generating has no value. In fact, the opposite is true: there are “modular” approaches to using real-time data that allow you to focus your efforts on specific challenges, while building toward a bigger vision.
The best example is condition monitoring. Understanding the conditions that lead to equipment failure and being able to “see” those conditions as they are occurring so that corrective action can be taken before a failure occurs has been the goal of maintenance personnel for years.
Now, condition monitoring using real-time data makes that possible. Here’s how it works.
Within a particular intelligent system, such as a conveyor or pallet storage system, technical data from the devices that comprise the system is collected continuously and managed centrally in big data applications. This data is then analyzed for physical values such as variations, temperature and location of individual elements. The analysis calculates the error frequencies of individual components and the entire system to identify components and systems that are at risk of failure.
Whether it is the energy consumption of a system, the deceleration path of a stacker crane, or the number of movements of a shuttle, condition monitoring provides continuous evaluation of the condition of critical components within the warehouse. This information is then visualized through the WMS to provide employees an intuitive and accurate view of the systems being monitored, including showing the impact the failure of individual components would have on the flow of goods.
Based on that information, rather than a set preventive maintenance schedule, warehouse personnel can determine exactly what actions need to be taken to prevent failure and schedule those actions at a time that minimizes disruption.
We’re generating massive amounts of data within the warehouse. It’s time to start using that data to improve operations. Condition monitoring represents a realistic and high-value way to do exactly that.