Take an exclusive look inside Nestlé’s new $77m UK 'distribution centre of the future'
December 12, 2019
The East Midlands Gateway building is being billed as one of the most advanced of its kind in the world
Next year, a new $77 million warehouse at SEGRO East Midlands Gateway, dubbed the Digital Distribution Centre of the Future, will start handling goods made by Nestlé, the largest food and drinks company in the world. Business Live’s Robin Johnson was given an exclusive tour of the building which is set to revolutionise the way products are delivered to customers.
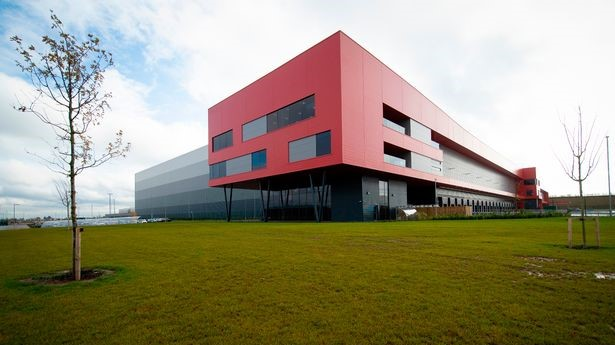
We all have an image in our head of what happens behind the doors of a typical warehouse. Lots of people handling boxes, forklift trucks buzzing about and a cacophony of noise.
Then you step inside the Digital Distribution Centre of the Future - a new $77 million facility at the SEGRO East Midlands Gateway, near Castle Donington.
Inside, there is technology that is set to revolutionise how goods are distributed - not just for the present time, but for the next quarter of a century.
Leased and operated by US logistics giant GXO Logistics, it will eventually handle products made by Nestlé, the largest food and beverage company in the world.
With a presence in 191 countries, Nestlé has more than 2,000 brands ranging from global icons to local favourites - not least its range of coffee Nescafé and Starbucks products, which are manufactured at Hatton, in Derbyshire.
In the UK, the company has 14 factories - including the one in Derbyshire - which together produce millions of units a year.
Once up and running, the Digital Distribution Centre of the Future, will handle the distribution of Nestlé goods made by 11 of these manufacturing sites.
However, the new warehouse has not just been built for the here and now. As its name suggests, it has been created to anticipate future demand for products over the next few decades.
It has been built with expansion in mind. Thousands of square feet have been set aside for growth and new machines as the volume of goods handled increases.
And it has been created at great expense. Of course, some of this cash has been used to create the actual building, which sits alongside the distribution sites of other big name companies, such as Amazon and Shop Direct.
But much of the investment has gone into the sophisticated technology inside.
The centre has been created thanks to a partnership between GXO, Nestlé and Swisslog - and has had a gestation period of around five years.
It has definitely been a team effort. All three companies have worked together to create a distribution centre which we believe is truly ground-breaking.
In terms of feet on the ground, the processes within are not as human intensive as neighbouring sites such as Amazon and Shop Direct. The size of the car park compared to its neighbours gives an indication of that.
That said, the centre will employ real people. Mr Williams argues that the technology is there to help humans do their job better, rather than replacing them. He said: “Because these are more technical roles, they are higher value jobs. The technology is there to give an improved employee experience. What we have created through the use of technology is a state-of-the-art facility that places great emphasis on safety, security and efficiency.”
In particular, technology developed by Swisslog has played a key role in making the centre a reality.
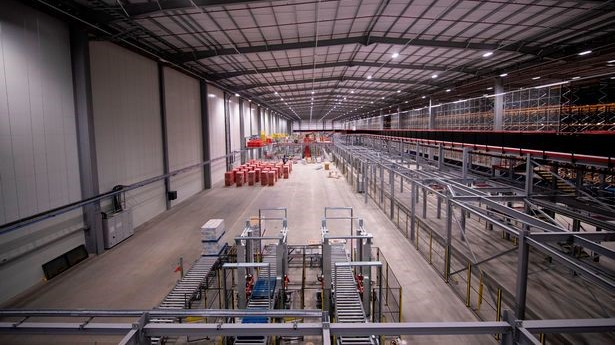
Its technology is a big feature of the custom-designed centre, which features advanced sorting systems and robotics alongside state-of-the-art automation.
According to James Sharples, managing director of Swisslog UK, the site’s digital ecosystem integrates predictive data and intelligent machines to deliver one of the most advanced distribution management centres in the world.
But as well as being a distribution centre, the building will have its own on-site laboratory, in which new systems will be tested and trialled, with a view to being introduced at some point in the future.
He said: “We’ve taken some of our existing technology and adapted and improved it to create this bespoke facility.
“But it does not stop there. Even when the centre is up and running we will be working with GXO, continuing to look at new ways of improving efficiency and increasing volume.”
In terms of how the distribution centre works in its current intended form, the whole process begins with the goods arriving at the building on pallets. These are then lifted by machine onto a conveyor and taken to a monorail.
Hung from an elevated pedestrian walkway, the monorail is a key element of the operation, transporting goods throughout the building.
The monorail takes the deliveries to the appropriate storage area. The centre is fitted out with huge areas of racking - some of which are temperature controlled, depending on the goods in question.
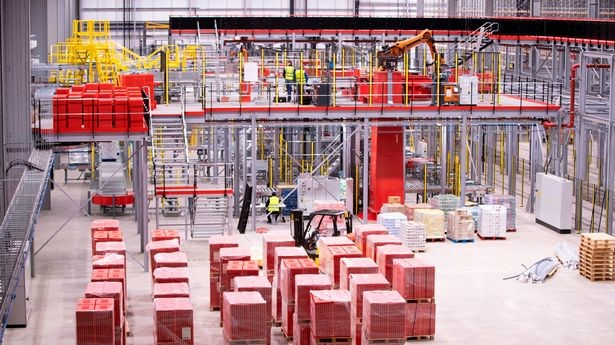
When it comes to distribution, one of the major benefits of the new centre is its ability to make up bespoke orders.
For example, a customer may not want to order a whole pallet of Kit-Kats.
Instead, they might want a mixed pallet of products - known at the centre as a “rainbow pallet”. To make up a mixed pallet, there is a very clever piece of kit that has been introduced by Swisslog. Called ACPaQ, this machine can make up a pallet with different products - a bit like a 3-D Tetris game. It can also work out which products should be on the bottom (namely the heavier items) and which should be at the top (the lighter products that would be likely to get damaged if they were on the bottom).
These pallets are then grabbed by another machine, put on a conveyer and sent to dispatch, ready to be loaded onto a lorry and off to the customer.
All of this is overseen by staff in an office, who are constantly monitoring the performance and health of the machines.
At present, the distribution centre is still in the testing phase, with engineers putting all of the machines through their paces and fine-tuning the processes. It is then hoped that the site will start operating for real some time in Spring 2020.
According to Nestlé’s director of supply chain David Hix, once up and running the East Midlands Gateway site will be one of the most advanced distribution centres in the world.
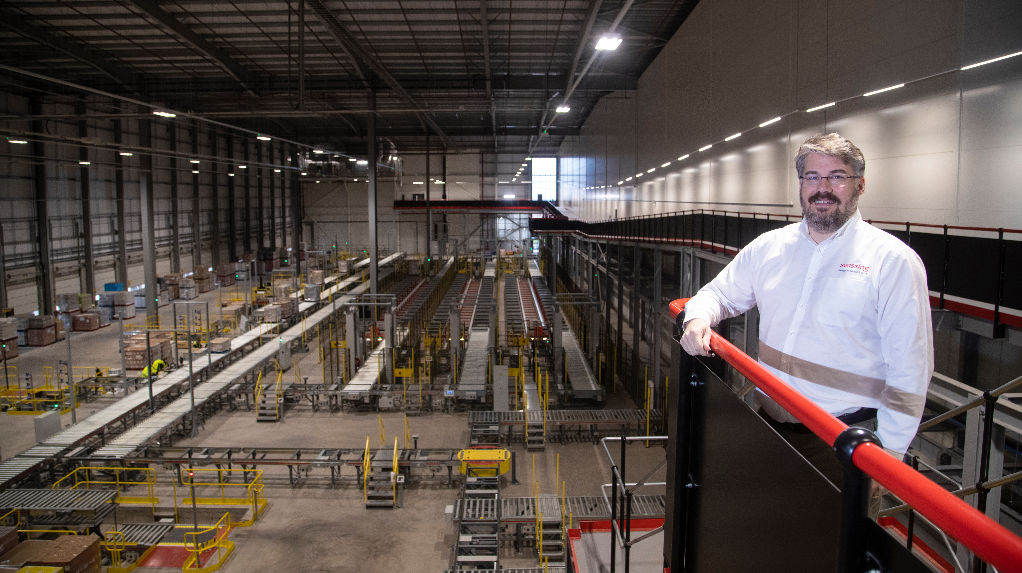
According to Nestlé’s director of supply chain David Hix, once up and running the East Midlands Gateway site will be one of the most advanced distribution centres in the world.
He said: “This is a world-first investment for Nestle that builds on a century and a half of proud history in this country.
“Our partnership with GXO and Swisslog will encourage innovation and experimentation in our UK logistics operations and help future proof our business.
“We will be able to be even more responsive for our customers across our brands, which include some of the most recognisable in the world.”
According to Mr Hix, going forward his company envisages that a key area of growth lies within the personalisation and customisation of products.
He said: “This is something that is becoming more and more popular. People are starting to be offered the choice of personalising products. For example, having their name printed on a box of Quality Street, which is something we’ve recently introduced in John Lewis stores.
“It is a big challenge to offer personalisation on a large scale, but the new distribution facility will help us to do this.
“It will also help us meet predicted demand. This new facility has been built not with the next couple of years in mind, but the next 25 years.”
Mr Hix also said he believed that East Midlands Gateway was the perfect location for the new facility.
While the distribution centre itself will handle a lot of boxes, Mr Hix said the site itself ticked a lot of boxes in terms of location and infrastructure.
He said: “Strategically, the location is excellent. It is central and has direct access to the M1 motorway for road transport.
“It is right next door to East Midlands Airport for cargo flights, and East Midlands Gateway will soon have its own on-site rail freight terminal, which is something that interests us greatly.
“We are extremely excited about this new distribution centre - and it will be a momentous day once it starts operations.”
Article courtesy of Robin Johnson from Business Live / Derby Telegraph. (Original article)