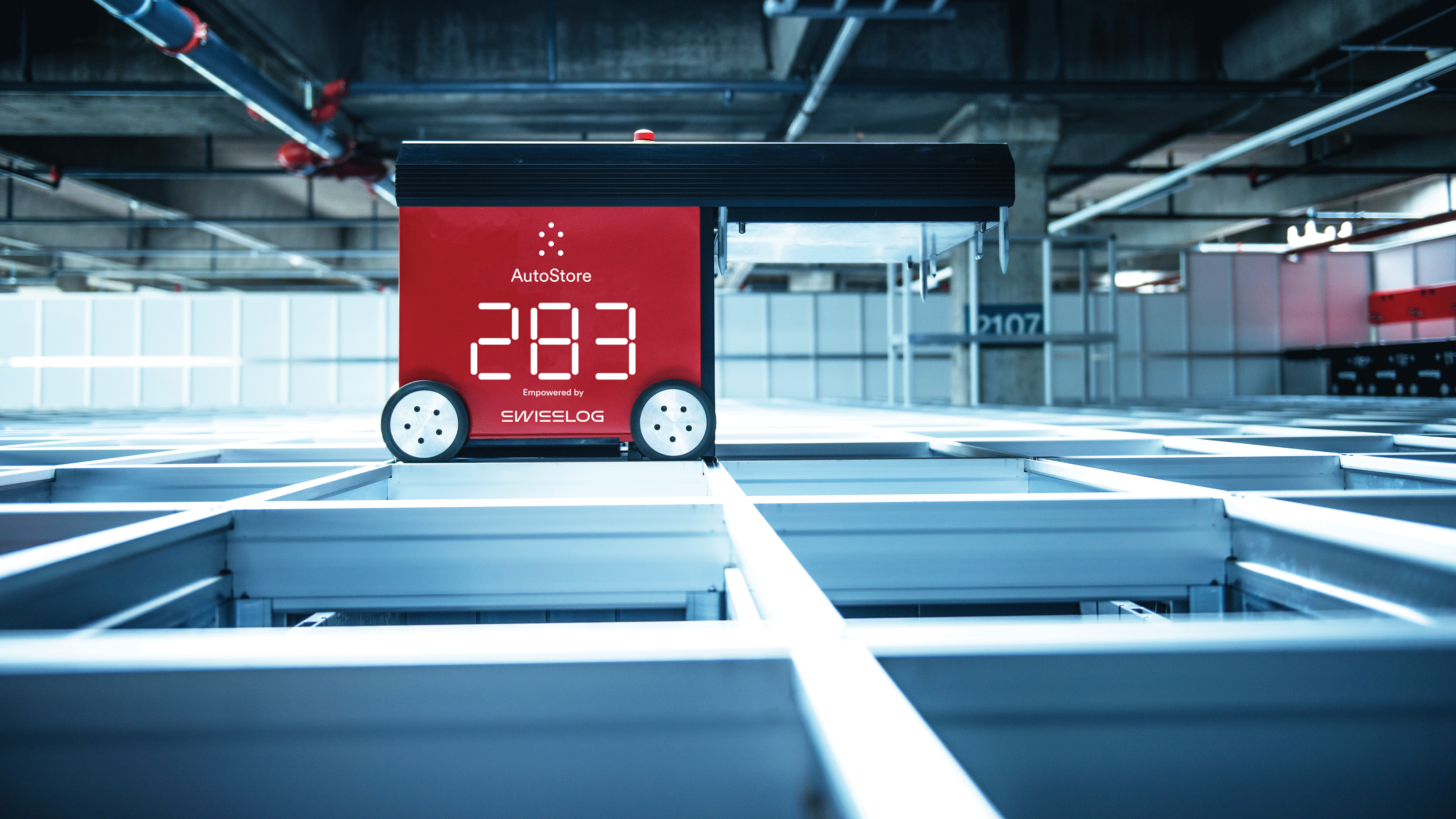
Can Robots Save the E-commerce Holiday Season?
1 October, 2019
It’s getting close to Halloween and that means it’s time for e-commerce fulfillment managers to start getting worried.
Not about tricksters or goblins, but about the availability of labor for the holiday season.
According to a recent article in Supply Chain Dive, “this year’s peak season promises additional challenges in recruiting new hires as the pool of available labor shrinks.” As the article points out, the U.S. unemployment rate hit a 50-year low in September 2019.
For stressed out fulfillment managers that can make even good news appear bad: the National Retail Federation projects holiday retail sales growth of 3.8% to 4.2% this year. Managing more orders with fewer people while responding to consumers expectations for faster delivery is exactly the scenario that keeps fulfillment managers up at night.
One solution is to up your recruiting game. But there’s no guarantee you’ll be successful, even if you choose to offer profit-draining bonuses or incentives. You’re not only operating in a historically tight labor market; you’re competing with everyone else in the retail supply chain for the small pool of available talent. The article points out that UPS has plans to hire 100,000 new employees this holiday season and FedEx is seeking to add 55,000.
Fortunately, there is another solution. This year may prove to be the tipping point for warehouse robotics that compensate for the shrinking labor pool by enabling the transition from time-intensive person-to-goods picking to productivity-enhancing goods-to-person picking.
The philosophy is simple. Instead of having pickers travel up and down aisles pulling products, store the products in a way that allows them to be presented to stationary pickers who focus exclusively on assembling orders.
This approach, which has gained significant momentum in the last three years, is enabled by compact, modular robot-based systems, such as AutoStore and CarryPick. They not only make better use of human resources, allowing more orders to be pulled with fewer people, they dramatically reduce picking times to help meet customer demands for faster delivery. They also don’t take breaks or go home at night so they can stage orders before human workers arrive on the job, effectively extending shifts without adding payroll.
Unlike traditional “bolted-down” automation systems, these modular systems provide the flexibility to scale to meet higher throughput resulting from sustained growth or peak demand. With either system mentioned above, robots can be added on-the-fly to support peak demand. Some warehouse operators even keep a reserve of robots idle for most of the year and then deploy them during the holiday season when throughputs hit their peak. They can also be moved to a new warehouse if the business outgrows the facility where they were initially deployed.
It’s become clear that fulfillment centers must reduce their dependence on human labor to continue to grow and meet changing customer expectations. Robotic goods-to-person automation systems provide a viable solution to do exactly that. The technology is mature, scalable and cost effective. To learn more about how these systems support sustained and seasonal scalability, read our white papers.