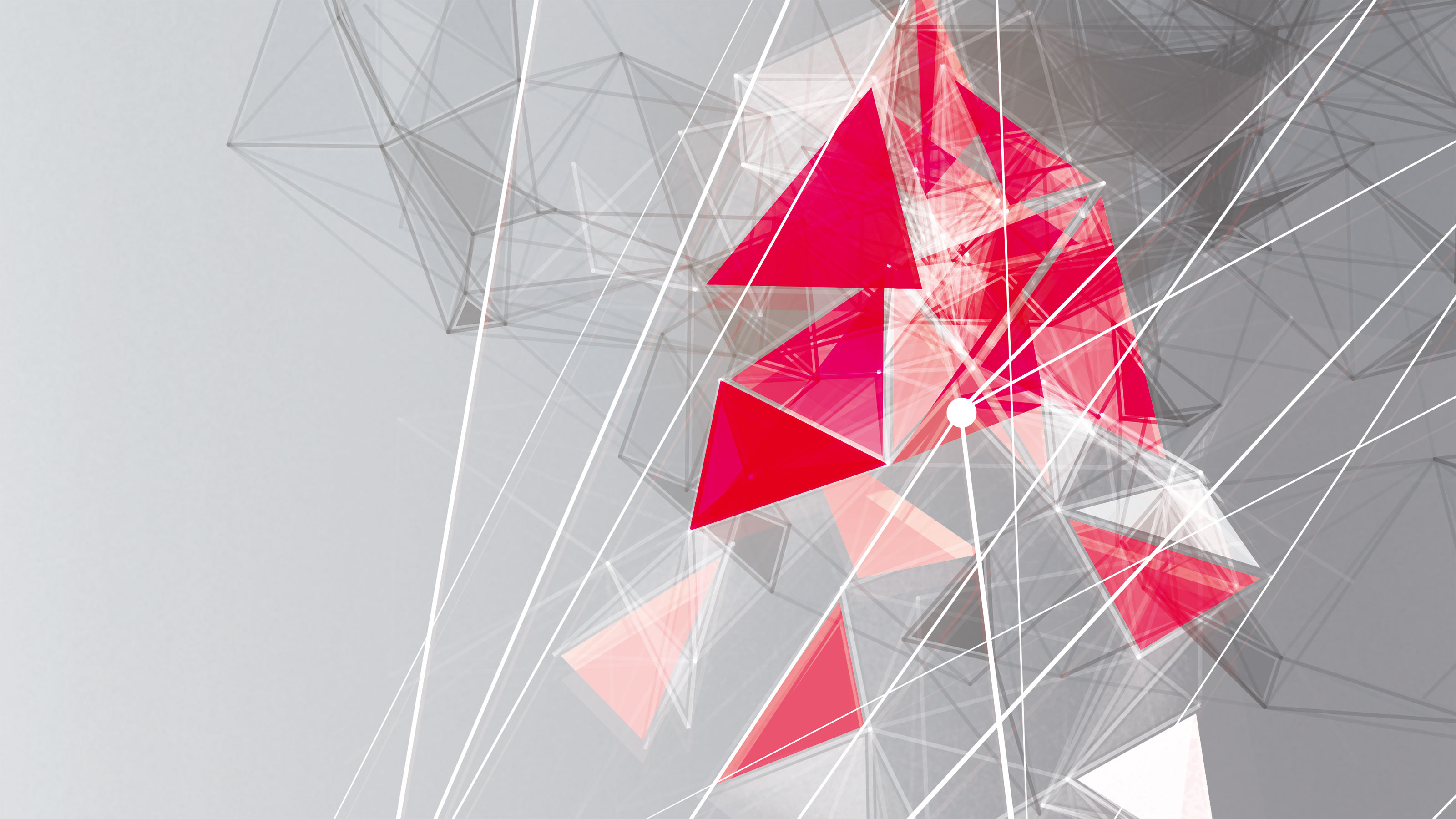
Industry 4.0: Interoperability – What is it and Why Should You Care?
14 February, 2017
What does interoperability mean for the future of your warehouse? Find out in our new post and learn three steps you can take today.
Interoperability is the ability of systems to transact with other systems. Typically this happens using industry-standard methods or protocols.
Pretty simple, huh? Yet discussions about interoperability can quickly devolve into highly technical references to standards, protocols and APIs. Those are necessary at some point, but for now we’ll keep the tech talk to a minimum and focus on:
- The challenges of managing systems that aren’t interoperable
- The role interoperability will play in Industry 4.0
- The steps you can take to enable interoperability
Interoperability is a challenge because many of the systems in warehouses today use proprietary communication protocols. These usually require expensive custom code to interface with other systems. Even worse, it makes it quite challenging to use data across systems to create automated reports.
For example, imagine your boss wants an answer to a question that requires you to pull a report from the ERP system. The ERP system doesn’t have all of the data you need so you also have to pull information from the WMS and LMS, which is output in Excel format. Then you find out you need data from a legacy AS400 system, which requires you to beg the one remaining AS400 programmer to help you.
Finally, you find you also need data from a production machine, which is sent to the MES but gets purged hourly. The machine provides logs in a proprietary format, so they have to be converted to Excel before you can merge the spreadsheets and do the calculations. You do the calculations, produce the required graphs and insert them into PowerPoint for your boss.
He’s happy and gives you a pat on the back. Everything worked out fine, right?
Not really. You spent hours compiling a report that could have been produced automatically if all the systems were interoperable. And, if that report proves useful, you may be stuck doing the same exercise every week for the rest of you career.
Longer term, interoperability is absolutely essential to transforming data into wisdom. Without it, it is simply too costly to manually generate the required reports.
But when we can easily access data across the supply chain, along with unstructured data from sources such as social media, it can be consolidated and analyzed at a lower transaction cost. You can then realize the vision of transforming data into information, and information into institutional wisdom. That wisdom, derived from both humans and machines, is essential to the intelligent, adaptive material handling systems that will emerge in Industry 4.0.
Interoperability and Industry 4.0
The evolution to Industry 4.0 is already beginning and will accelerate in the coming years. Digital devices, such as accelerometers, thermal sensors, vision systems, navigation sensors, and scanners are proliferating on everything from individual products to material handling equipment, robots and wearable devices.
These IoT-enabled devices will generate enormous amounts of information, which when collected and aggregated create the opportunity for collaboration across equipment and robots as well as supporting real-time decision making.
Ultimately, interoperability will enable the consolidation of the “digital exhaust” from every process, machine, and human across the supply chain. This will allow the transformation of material handling equipment and software into a smart warehouse that anticipates demand and makes fulfillment decisions autonomously based on the “wisdom” derived from data. That’s the promise of Industry 4.0 and it’s dependent on interoperability.
The Path to Interoperability
System wide interoperability won’t happen without planning. Here are three things you can do now as you move down the path to Industry 4.0:
- Assess your current platforms: Audit your existing systems and processes to identify systems that have proprietary protocols and those that use standard protocols and offer open APIs. In almost every case, it will be preferable to move away from proprietary systems as they can lock you into a single-vendor strategy or require expensive customer coding. Enough of the industry has already moved to standard protocols that there isn’t’ a strong business case for proprietary systems today.
- Do a Pilot Project with clear objectives but limited in scope: Prioritize the business issues where interoperability can deliver the most value in your organization. Speed, cost, accuracy, productivity, and uptime are all important, to some degree, to almost every fulfillment operation. This can quickly turn into trying to boil the ocean. Choose a project with a compelling business case, such as achieving a desired improvement in fulfillment times. Then, focus on interoperability across those systems that directly impact that metric. Key to the success of such a project is building a team of believers with a senior champion to clear roadblocks.
- Create a long-term roadmap: If you haven’t already, create a vision for the future of your operation optimized for collaboration and real-time decision-making. This vision will help ensure the investments you make in the coming years will support, rather than impede, future adoption of Industry 4.0 technologies.
Industry 4.0’s core tenets are already emerging within the supply chain today in the form of increased use of data and automation. Understanding where it’s going — and the role interoperability will play in its evolution — is essential to capitalizing on its potential.