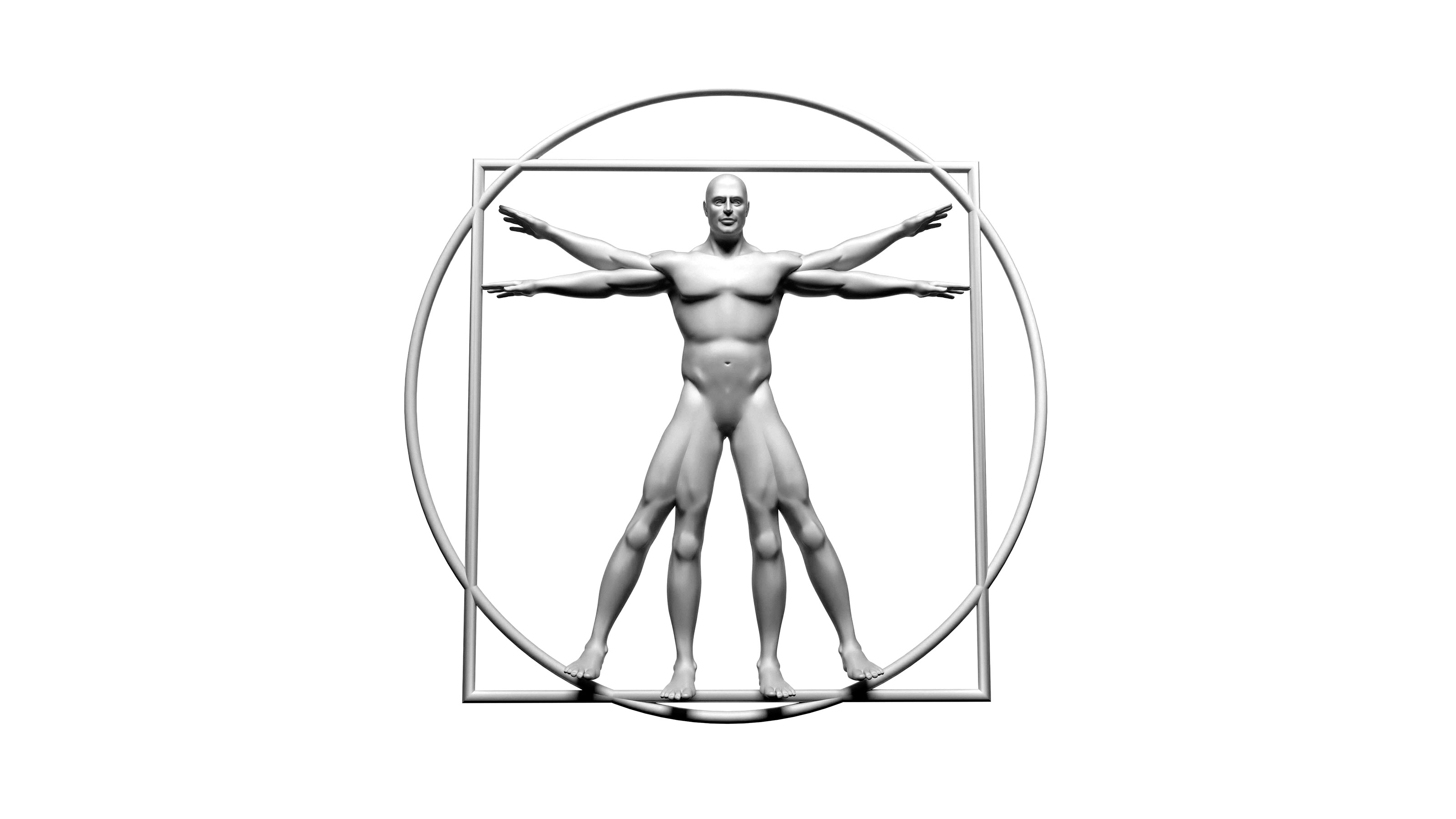
Improving Ergonomics in the Warehouse: Reduce Injury Risks, Improve Productivity
21 January, 2016
Need to keep up with the explosion of SKUs and demands for multi-channel fulfillment? The experts often advise adding automated material handling equipment (MHE) and advanced warehouse control software to improve productivity.
It is also important to focus on improving ergonomics in a distribution center (DC) to make your warehouse safer and less fatiguing and to improve the work environment for employees.
Some warehouses are completely automated, but the vast majority require employees to manually handle stock and product. As a result, the risks of costly accidents and repetitive injuries are high. These businesses also are not equipped to compete in a marketplace in which SKUs are growing in variety and volume, and where customers are placing smaller orders more frequently.
Ergonomics has a real business impact. Productivity is typically low in manual picking and packing operations compared to DCs with modern automation hardware and software. It's possible to automate warehouse material handling to levels of 90 percent or more. Whether you need to invest in automation to that extent depends on the size, shape and weight of products handled in your DC, among many factors. Here's what you should consider.
Driving the Need for Ergonomics
Three major factors impact the need to improve material handling methods:
- The pool of workers
- Market demands
- Customer order profiles
The workforce is aging. In 1972, the average age of U.S. workers was 28; today the average age is 46. Those 55 and older in the labor force are projected to rise to 25 million this year, and 32 million in 2025.
At the same time, consumers now demand multiple versions of all sorts of products, leading to ever-larger SKU volume and increasing size of pick zones. Consumers also expect rapid fulfillment and to be able to place orders via multiple media. To keep up, automation can be the solution for many distribution operations.
What Companies can Do
When manual material handling dominates the daily operations of a company, it is only reasonable to assume that companies would want to optimize this process.
Risks to workers' health and safety, along with higher medical and workers' compensation costs, are all too real. About 60 percent of all workers' compensation claims for lost-time injuries are associated with material handling in DCs. Automation can dramatically reduce the risk of repetitive motion and other injuries from manual material handling.
If products, material and tasks can be positioned so that employees can minimize reaches and work more consistently in the so-called golden zone, or power zone, then the employees' posture can be optimized. Ergonomic specialists refer to a zone that is optimal for lifting, handling and carrying material. The zone is generally defined as between the shoulders and the knuckle height of an average person when standing. In this zone, the employee can move his or her hands freely without too much biomechanical strain. Designing DC operations to stay within this zone improves productivity and reduces the risk of back and shoulder injuries.
Here are some common-sense ergonomic approaches that protect worker safety and improve productivity that are worth consideration:
- Slot fast-moving SKUs close to pickers.
- Design pick faces that are at a comfortable height and angle and are adjustable.
- Use MHE wherever possible for goods-to-person picking. Pick locations and order cartons/totes should be consistently placed at optimal work height.
- Don't try to automate everything. It's more efficient to pick some items manually (because of their size, weight or order volume). Automation is expensive, so invest in it where you can reduce the most risk and maximize productivity.
Case Study: How One Manufacturer Eliminated the Heavy Lifting
One North American company manufactures dense products and distributes them in multiple containers weighing 30 to 60 pounds each. In its existing warehouse, automated equipment handled only about 40 percent of this weight. Workers manually picked these heavy containers from pallets on the floor or racks and stacked them to customer order pallets.The company wanted to improve the work environment to minimize employee turnover, improve safety, avoid injuries, and reduce medical and workers' compensation costs. The goal was to automate handling of at least 85 percent of the weight.
Our solution: goods-to-person equipment combined with robotic palletizing and de-palletizing. By combining MHE and warehouse execution software, the company's DC could expect to exceed the goal of increasing automated handling from 40 percent to greater than 90 percent of the weight. Manual picking would be used only for lighter accessories that come in a variety of odd shapes and sizes.
Make the Business Case for DC Ergonomics
Companies pay for poor DC ergonomics through workers' compensation insurance premiums. They also pay in productivity losses as employees are commonly fatigued, or worse, sidelined by injuries and unable to work.Successful businesses treat ergonomics as seriously as they do accident prevention. Consider automation to reduce or eliminate floor-level lifting and stretching to reach loads above or below arm level. Automation also can avoid putting workers in positions that require excessive bending or stretching over long periods of time. Distribution centers should be designed to store heavier and high-use items within the golden zone, or power zone, or to employ lift-assistance equipment. DCs also should store lighter and low-use items in warehouse locations that are not heavily trafficked.
You'll trade some operational flexibility to improve ergonomics, but you can recoup your investment in automation with a significantly fresher, less stressed, more energetic workforce and reduced risks and costs of injuries.
It's possible with today's MHE and software to automate 90 percent or more of distribution operations. A trusted, expert partner like FORTE can help you determine the right mix of equipment and warehouse execution systems needed to provide a safer and more productive DC.